Fun with Force Gauges
- Published: February 29, 2004, By Timothy J. Walker TJWalker & Assoc. Inc.
In today's world of high-tech electronic gadgets, a force gauge may seem unglamorous, but I hope to convince you a force gauge is something you should have and use.
A force gauge essentially is a handheld bathroom scale. The scale doesn't know how much you weigh; it simply shows a number proportional to how much your weight compresses the springs. A handheld spring scale is the same, with the ability to measure force of compression or elongation in pushing or pulling directions.
For a handheld force gauge, I think 0-50 lbf is a good size; it is an amount I can pull by hand comfortably and has good resolution to 0.5 lbf. Most force gauges are pre-calibrated and have a zero-offset adjustment to compensate for the angle of measurement. It will have a threaded rod for attaching a hook or clamp.
I prefer a purely mechanical spring-based force gauge, but for techie bragging rights, an electronic force gauge will have better resolution, plus data storage and output. You also will need a few accessories, which I include in the description of each test method.
Measure dancer roller or nip loads
Wrap a strap around your nip or dancer roller and measure the force to move it. Make a calibration chart of nip or dancer force versus air pressure from zero to as much as you can pull. For higher force measurements, strap the force gauge to a fixed point. Even if you can't measure all the way up to your normal running pressure setting, you should be able to extrapolate from the data you have.
For dancers, measure this force in both the accumulating and dispensing directions, then divide the difference of these two readings to see the tension variations caused by hysteresis and friction.
Measure torque of bearings, brakes, and clutches
Attach the strap to the surface of a braked or clutched roller or core. Pull with the force gauge to measure the breakaway force and the force to keep it turning at a slow steady rate. Again, take multiple force readings with the air or amps off and at increasing increments. Multiply the force values by the radius of the roller or core to convert force to torque.
For slitters with differential rewinding, I highly recommend doing this to compare cross-shaft and shaft A-B variation. This shows how consistent your process is (or isn't).
Measure web-to-roller friction or traction
Wrap a strip of your web around a roller with the free weight on one side and the force gauge on the other. Holding the roller stopped, measure the force to slide the web around the roller, keeping the wrap angle constant. Measure this in both the weight lifting and falling direction. Use the capstan equation to calculate the friction coefficient from the two forces and the wrap angle in radians.
To quantify air lubrication, measure the force to keep a roller from turning at increasing speed or decreasing tension. As this force decreases, you are measuring web-roller air lubrication (though this test excludes the half of entrained air created by the spinning roller).
Measure web modulus
If you need a quick estimate for the modulus of a material, a force gauge and tape measure can be used as the poor person's tensile-elongation tester. Cut a long strip of web, fixing it at one end and pulling on the other end with the force gauge. Modulus is the change in stress (force/thickness/width) over the change in strain (percent change in length). This test isn't accurate enough for foils or thicker products, but it can estimate modulus within 20% for many webs.
Measure internal wound roll pressure
Make a sandwich of the steel feeler gauge in a sleeve of brass shim stock. The brass sleeve should be longer than your roll is wide and the
steel longer yet. Insert the brass-steel-brass sandwich crosswise into a winding roll so it sticks out both sides. When the roll is finished, use the clamping pliers to grab the steel and measure the force required to slide the steel relative to the brass.
With a little frictional algebra, you can translate this force into the local layer-to-layer pressure in the wound roll. There are roll width limits to this test, but it provides valuable and inexpensive insight into the pressures within a wound roll.
While you are all busy perfecting these new force gauge tricks, I'm taking mine out to the lake to weigh my latest catch.
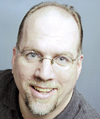
Timothy J. Walker has 20+ years of experience in web handling processes. He specializes in web handling education, process development, and production problem solving. Contact him at 404/373-3771; This email address is being protected from spambots. You need JavaScript enabled to view it.; tjwa.com