The Buzz on Remote Diagnostics
- Published: August 31, 2004, By David J. Bentley Jr., Contributing Editor
Walk into any room these days where numerous people are assembled and mention “remote diagnostics.”
Immediately, you will become the central attraction. Well, maybe this would not happen with any group, but it undoubtedly will at any meeting of people that work in technical fields.
Everyone wants to determine the solution to a problem using a telephone line that connects the location of the problem with the location of the problem solver. This is remote diagnostics.
Once the subject of remote diagnostics is introduced, the first few bits of conversation usually will concern the use of offshore call centers, which are becoming more common with each passing day. Many companies now use remote locations outside the US with local residents that handle calls for assistance with computer software or hardware problems. Some callers to these centers delight in trying to ascertain the location and actual name of the person answering the telephone.
To discuss other remote diagnostics, consider two locations: A and B. One location has a problem, and the other location will try to solve the problem. At each location, two possibilities exist: a person or a computer. Now four possible methods of communication exist:
- A person at A location can communicate with a person at B location.
- A person at A location can communicate with a computer at B location.
- A computer at A location can communicate with a person at B location.
- A computer at A location can communicate with a computer at B location.
The first possibility is the “old-fashioned” method, examined in greater detail shortly. The second possibility requires the person at A location to log onto the computer at B location and examine the values of all the parameters the computer is measuring. Using the example of an operation involving an adhesive lamination, the person at A location will study remotely oven temperature, nip temperature, line speed, etc., to try to determine the reasons for a specific problem.
The third possibility is very similar to the second, except the person at location B provides the necessary information such as given for the previous example to the computer at location A. Then the computer examines the data it receives to try to determine the cause of the difficulty.
The fourth possibility involves two computers communicating with each other. We humans are not privy to the exact specifics of such “conversations,” but we do know the two computers exchange information much like the second and third possibilities to solve a problem.
Do remote diagnostics as exemplified by the four possibilities listed here actually work? Sometimes yes. Sometimes no. Why does this occur? As everyone probably has guessed, obviously the answer is the ability of a computer to solve a problem depends solely on the excellence of the programming that operates the computer. If the computer “knows” to examine every possible variable, theoretically it can solve any problem. Unfortunately, the person who wrote the program may have neglected to include considering the degree of wrap on a heated nip roller, the use of urethane-grade solvent to dilute a PU adhesive, etc.
The “old-fashioned” method is, therefore, often the best way to solve a problem, especially if it's a complex one. In fact, a modification may be required that wouldn't be evident unless the people involved at each location actually meet face to face.
Consider the example of a converter making an adhesive lamination that consistently gives low bond values on Friday mornings during cold months of the year. The solution to the problem was evident only after a visit from the adhesive supplier on such a Friday morning. A trash collector who came every Friday always propped open two doors in a far area of the plant to make his many trips in and out of the building easier. This resulted in a sufficient drop in temperature so the adhesive-coated web cooled slightly on its way to a slightly cooler running nip roller. The likelihood of a computer being programmed to discover this cause is very small.
Because of this type of scenario, remote diagnostics will not replace old-fashioned problem-solving completely in all instances.
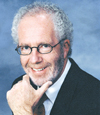
David J. Bentley Jr. is a recognized industry expert in polymers, laminations, and coatings with more than 30 years of experience in R&D and technical service. Contact him at This email address is being protected from spambots. You need JavaScript enabled to view it.