Slitting Debris: Cracking the Case
- Published: October 31, 2004, By Timothy J. Walker, TJWalker & Assoc. Inc.
Dust and debris are a common but unwanted side product of slitting. Slitting debris comprises the small particles that break off a product's edge during the slitting process. It is created through fracture and abrasion. Uncontrolled slitting debris will lead to defects in your customer's product and equipment downtime.
When you slit your product, you use knives to concentrate stress mechanically, breaking the web along a narrow line. The product splits when a crack forms. When the stress is high enough, the web will snap apart like breaking glass. Though the stress-induced crack usually is contained within a high-stress zone, the cracks will bifurcate (split or fork). Like ice cracking along a river's edge, if two cracks rejoin, they may create an unattached chip.
Even if the fracture process doesn't create debris, it may leave a ragged or slivered edge that will chip away easily if touched. All three conventional slitting methods (razor, crush, and shear) require the freshly fractured edge to drag along the blade's flank as it passes downweb. The side load and relative motion during contact cause abrasive wear of both web and blade, creating a dull blade and slitting debris.
Which materials create the most debris? Slitting brittle materials generates the most debris. Think about the difference between cutting soft bread and brittle toast. Since brittle materials reach their fracture stress quickly, the cracks in the slitting or abrasion zone will bifurcate more, forming more unconnected material.
Which slitting method creates the least debris? It is rare to try all three methods on one material, so my empirical comparison is biased by real-world applications. Material plays a dominant role in which method makes the best edge or is easiest to apply. Also, consider how stress is concentrated to create fracture stress and how much inherent web-knife abrasion there is. Given those caveats, I rank the slitting methods — from least to most debris generation — as shear, razor, crush, and shear.
Shear is listed twice as it is both the best and worst debris generator. Done poorly, with nicked, dull knives and arbitrary geometry, shear slitting can be a debris factory. Worse yet, shear slitting can create angle hair (long strings of skived material) and double cuts. Shear also can be the cleanest, most precise slitting method. Shear slitting's tip-to-tip stress concentration can be more focused than razor or crush slitting. The rotating knives reduce web-knife relative motion and abrasion debris. Precision shear slitting, with tight control of runout, engagement, and sharpness, is the cleanest (and most expensive) slitting method for many products.
Razor slitting creates a small fracture zone when sharp, but this will diminish continuously by dulling abrasion over time. Oscillating or hard coating a razor blade will reduce dulling rates, but due to their low cost, most people opt to just change razor blades frequently. If your slitting is relatively inaccessible, prohibiting frequent blade changes, razor may be a poor choice.
Crush slitting blades work with the dullest blade edge (a.k.a. tip radius), but when used on brittle materials, the slit edge will be surprisingly crisp. Like shear slitting, the rotating knives have little relative motion with the web's edge, so abrasion wear is minimal.
Where does slitting debris go? It is most obvious at the point of slitting. Dust and debris will build up on knives and pile up below knives. Slitting dust can get into bearings and cause early failure. Slitting debris also will go downstream, clinging onto the top, bottom, and side surfaces of slit edges. Rubber rollers downstream of slitting will develop dust rings aligned to the slit edge contact. Without a mechanism to transport the debris laterally, slitting debris will stay near the web's edge.
How can you minimize slitting debris? Minimize the two sources of debris: uncontrolled fracture and avoidable abrasion. Sharp knives with proper geometry and loads are a good start. Take care to avoid abuse in handling, installing, and running your knives. Higher slitting zone tensions will provide a starting point to reach fracture stress and encourage the web to neck away from the knives after fracture, reducing abrasive wear and debris.
If you have a slitting debris problem, look into improving your existing process before pursuing alternatives. For new materials, consult with material or slitting equipment suppliers on their recommendations.
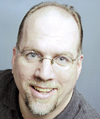
Timothy J. Walker has 20+ years of experience in web handling processes. He specializes in web handling education, process development, and production problem solving. Contact him at 651/686-5400; This email address is being protected from spambots. You need JavaScript enabled to view it.; tjwa.com.