Die Options Explained
- Published: December 31, 2004, By Bill Knotts, Spartanics
Die-cutting
The wide range of specialty packaging items now being ordered by customers—from packages in the shape of Chinese food containers to pyramids or baseball diamonds—often makes optically registered die-cutting systems the better method for cost-effective and high quality die-cutting. However, new types of dies make it important to reacquaint yourself with your options when using an optically registered die-cutting system.
First, a quick recap on the advantages of optically registered gap presses when die-cutting a wide range of printed packaging jobs. Because this type of die-cutting system allows for quick job changeovers, it is a popular choice for converters looking for an easy way to expand their manufacturing capabilities and break into new markets—especially the specialty advertising market.
Changeovers between jobs are quick and easy with top-of-the-line optically registered die-cutting systems that position the die in the same place every time. Optically registered gap presses also have the advantage of easily running in-line with other equipment such as digital printers or laminators that can accommodate coil or sheet-fed materials and easily can be paired with different extractor modules.
The best types of these systems also have a modular design that allows you to remove only the malfunctioning part in the event of a breakdown and replace it with a loaner module from the equipment manufacturer.
These better-engineered systems also offer unsurpassed registration precision. They can achieve ±0.005-in. or better cut-to-print registration in three axes (X, Y, and Theta), and they re-register with each press stroke.

High-precision, optically registered die-cutting systems also can work with a range of different dies, depending on the job at hand. But before thinking about using new or different dies, you need to check some important features of your die-cutting system.
It is not uncommon for manufacturers of die-cutting systems to create proprietary designs for their machines, so you can use only the dies they manufacture. If you are considering making an investment in a high-precision, optically registered die-cutting system, look for manufacturers that offer a universal die holder that can be adapted to work with any die.
This is important especially where more expensive, longer-life dies are concerned. A universal die holder guarantees you will be able to get the best use out of your optically registered die-cutting equipment.
Steel Rule Dies
Steel rule dies are a very popular choice for converters using their die-cutting equipment for short-run jobs, particularly for the specialty advertising market. Steel rule dies are inexpensive, easily can be made in any shape, and can be delivered to a converter in a matter of days. Well suited to short-run jobs, they typically last for 250,000–1,000,000 cycles before they need to be resharpened, depending on the material being cut and the type of cut being made.
Male/Female Hard Tool Dies
For long-run jobs that are repeated over and over, male and female dies (or hard tools) are the best option. These dies last much longer than the steel rule dies—up to 3 million cycles before they need to be resharpened—and can be resharpened 12–15 times.
These male and female dies offer the highest edge-cut quality and die-line accuracy, but they are considerably more expensive than steel rule dies: One set of male/female dies can cost roughly $30,000 compared to a few hundred for the steel rule die. However, these dies have a much longer lifetime, and this results in the lowest cost per unit for longer runs.
Taking the numbers mentioned above, a standard 3-up die then can produce 3 million parts after each of the 12 times it is sharpened (3 x 3,000,000 x 12) for a total of 108,000,000 or more parts in its lifetime. This comes out to about $0.00026/unit.
Now, these types of dies are available for 10-up systems, such that the cost optimally can come out at $0.00019/unit. For long runs of 100 million or more units, this type of die is the best choice.
Mini-Dies
A lower-cost alternative to the standard male/female dies is something called a "mini-die." The mini-die is a modified form of a male/female die that also provides high edge-cut quality and can be sharpened up to 12 times, yielding 750,000–1,000,000 operational cycles.
Though they have a lower up-front cost than the male/female dies, they ultimately have a higher cost per unit. If you take 1,000,000 (parts per cycle) x 3 (for a 3-up die) x 12 (sharpenings) you get 36,000,000 units, which translates to $0.00033/unit. Given the lifetime costs, this type of die is best suited to orders of less than 100 million units.
Modular Dies
Another alternative for runs of less than 1,000,0000 is the "modular die." This recently developed die is designed to bridge the gap in quality and cost between the male/female dies and steel rule dies.
Modular dies are priced around $6,000, in between the more expensive male/female dies (at about $30,000) and the steel rule dies (at about $400). Modular dies last for about 500,000 cycles, but unlike either the steel rule or male/female dies, they cannot be re-sharpened. If you need a high quality cut approaching that of a hard tool, but it is impractical to invest in hard tooling because of the cost, the modular die is ideally suited to the job.
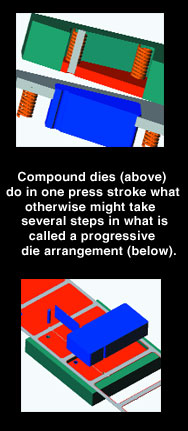
Progressive and Compound Dies
For more complex jobs that require a number of different cuts, scorings, etc., you have a choice between a compound and progressive die.
A progressive die system works by moving material through a series of stations, each of which adds a feature. For example, the first station will put in a score line, the second will cut out the entire shape, and so on. Unlike many other die-cutting setups, you do not need a special extraction system for the end of the cycle.
The downside of a progressive die system is that the accuracy of the die-cutting depends on the precision of the system that moves the material between stations and the accuracy of the printing. In general, you should expect any features on the package to move around within 0.010 in. as a job moves through progressive die stations.
An alternative to this is the compound die, a die designed to cut all special features into the package in one press cycle. Multiple tools are built inside each other, eliminating the several steps required for the progressive die system. This method is much more accurate than the progressive die system, since variations in printing and in print registration are no longer an issue.
With a compound die, you can expect a much greater level of accuracy, with special features correctly placed within ±0.0005 in. But unlike the progressive die system, the compound die must be used with some sort of extractor or knock-out to remove the die-cut part from the scrap material.
Once you are familiar with the advantages and disadvantages of each type of die that can be used with top-of-the-line, optically registered die-cutting systems, you can confidently pick the right die for the job. Whether you are doing a short run of a special promotional package or doing a job for a long-time customer of 150 million units or more, there is a die uniquely suited to your needs.
Using the right die for the job will save you money in the long run, and when this is combined with the flexibility of high- precision, optically registered die-cutting systems, you are guaranteed the best return on your investment.
SUPPLIER INFO:
Spartanics—spartanics.com
Bill Knotts is president of Spartanics, Rolling Meadows, IL, makers of a range of automated, optically registered technology used in the graphic arts and converting industries, including steel rule die-cutting and punching systems. He can be reached at 847/394-5700; billk@spartanics.com.
The views and opinions expressed in Technical Reports are those of the author(s), not those of the editors of PFFC. Please address comments to author(s).