UV/EB a Bright Spot in Economy
- Published: February 28, 2005, By Richard M. Podhajny, Ph.D., Contributing Editor
Material Science
The US ink market for radiation-curable inks and coatings was estimated to have reached $360 million in 2002. The bulk of these sales have been in UV-curable screen, offset lithography, letterpress, and narrow web flexo printing inks.
In recent years, the US printing ink industry has struggled through some tough times, much like other segments of US industry. The radiation-curable sector has been one of the few growth areas.
Even this bright sector, however, is under pressure from rising raw material price increases. Recent shortages of acrylic acid exemplify the problem of raw material supply and its impact on the price stability. Last year saw various price increases in raw materials, and this trend is continuing into this year. As a result, it is anticipated raw material price fluctuations will impact UV/EB products negatively.
The strongest segments of UV ink use are folding cartons and labels. Whereas folding cartons are printed primarily by lithographic sheet-fed inks, labels typically are printed flexo narrow web. Use of UV gravure is negligible, as is UV wide web flexo.
Hybrid presses that allow the combination of different printing methods with UV continue to be popular.
Odor issues associated with some free-radical UV systems have caused some printers to turn to cationic UV inks and coatings in odor-sensitive flexible packaging applications. The use of cationic UV products still is small in comparison to conventional free-radical UV products.
The bright star for radiation-curable inks and coatings is the UV-curable digital ink jet arena. This new sector continues to show rapid growth. Although the usual reasons apply, such as elimination of VOCs and lower energy consumption, the primary reasons for the current interest in UV-curable jet inks are the following:
- UV jet inks offer broader adhesion range and can be printed on many different substrates.
- Increased productivity, as press speeds can be higher than with use of conventional water- or solvent-based ink jet.
- The inks are stable, without the tendency to clog the jet nozzles.
- They offer better product resistance, such as gloss, lighfastness, etc.
- They allow in-line post-printing operations, such as embossing.
Technological advances continue to improve the chemistry as well as the equipment in UV/EB applications. Clearly there is less odor, better viscosity characteristics, and more color stability in today’s UV inks. Higher-intensity lamps are available with better heat control in the lamps and reflectors. New UV lamps that offer instant on/off features are in development and may offer new capabilities approaching some of the advantages of EB curing.
Use of external photo initiators can be reduced with the use of "photo-sensitized" resins and oligomers that can absorb the UV energy and catalyze the photo polymerization.
Today, many printers are not interested in new products unless they benefit their bottom line. The price of UV/EB inks is "the coin flip," while the productivity is "the ball game."
Improved productivity is the main driver for energy-curable inks and coatings. Faster press speeds, broader substrate application, consistency, and eye appeal continue to support the growth of UV/EB inks and coatings.
Although UV/EB materials remain attractive to environmentalists because they reduce solvent emissions from printing sources, the application of these products in the food packaging industry would be a major event.
UV technology has reached a mature point, and printers are looking to see the promised cost reductions based on increased volume. However, price increases of raw materials and slow growth have put a damper on any expected price reductions. A more likely scenario is price increases. Price instability in the raw materials will continue to play a significant role in the near term.
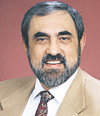
Dr. Richard M. Podhajny has been in the packaging and printing industry for more than 30 years. Contact him at 267/695-7717; This email address is being protected from spambots. You need JavaScript enabled to view it..