Cleaning the Right Way
- Published: March 31, 2005, By David J. Bentley Jr. Contributing Editor
PLC Probe
Whether a converting operation that uses adhesives and coatings is clean or messy as a rule, ultimately cleaning is necessary. Spills and splashes happen.
Material used during a job may dry on the equipment for one reason or another. Runs using one particular adhesive or coating end, and the next run may require a different adhesive or coating. Sometimes equipment needs cleaning. At times the surrounding area such as the floor needs cleaning.
Cleaning has two important goals. The first one is obvious: Be certain the surfaces are clean and free of any residual adhesive or coating. The second one is less obvious: Be certain the cleaning operation does not create any hazards to the personnel doing the cleaning or to the environment.
Unfortunately, people sometimes become so obsessed with ensuring they achieve a totally clean result, they may neglect the personnel and environmental safety issues.
The first step in any cleaning operation is to consult the literature from the manufacturer of the adhesive or coating. Because of their different physical form and chemical composition, different materials probably will require different cleaning methods.
Some simply may require washing with water. Perhaps others will need soaking in solvent or a repeated wiping with cloths soaked in solvent. Still others will require scraping with a tool.
Regardless of the cleaning method, the first step is for people doing the cleaning to don the necessary protective gear. Safety glasses always are necessary. Respiratory equipment may be essential. When using solvent, be certain no sources of ignition are present. If the item being cleaned is a piece of machinery, the equipment must be off and locked out.
Disposal of the cleaning materials requires serious attention. Again, supplier literature may be helpful. Local, state, and federal regulations regarding disposal often have very strict restrictions on disposal.
If the adhesive or coating being cleaned is an aqueous material, the best method for cleaning is probably to dilute it and then wipe it with a wet cloth. Depending on the applicable regulations for disposal, the liquid resulting from the cleaning may require special disposal. Flushing it down a drain or sewer may be illegal.
Rags containing solvent that have been used to clean adhesives and coatings supplied in solvents require special disposal. When allowed to accumulate in a container, they can start a fire by spontaneous combustion.
Heat sometimes is applied when cleaning extruders, application equipment for hot melt products, and the like. This requires specialized attention as well, so personnel are not burned during the operation. Excessive heating of extrusion products or hot melt materials possibly could cause them to decompose or otherwise emit fumes. Breathing such fumes can be unhealthy.
Purging extruders results in materials that require disposal when they cool to room temperature. Again, disposal of these materials must comply with all local, state, and federal regulations.
All these precautions make cleaning sound complex.
Unfortunately, that is simply the reality today.
Some people opt for another approach that can cause serious problems. Rather than clean between the use of one adhesive or coating and another, they simply run the first product until the equipment is almost completely empty of product. Then they add the new adhesive or coating.
Obviously, this results in some material that contains a mixture of two adhesives or two coatings.
If the intention is to discard the final product made with this mixture, this may be an acceptable practice. If the aim is to use this as finished product, the converter should be fully aware such material is unique in its own right and is neither individual product. Using it as finished goods could lead to unwanted problems for the end-user.
This approach to cleaning is probably one that everybody should try to avoid at all costs. The potential headaches simply are not worth the possible problems.
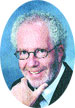
David J. Bentley Jr. is a recognized industry expert in polymers, laminations, and coatings with more than 30 years of experience in R&D and technical service. Contact him at This email address is being protected from spambots. You need JavaScript enabled to view it..