Which Ink for Which Substrate?
- Published: March 31, 2005, By Dr. Richard M. Podhajny, Ph.D. Contributing Editor
Material Science
Every new ink project begins with an analysis of the substrate to be printed. In just minutes, the complexity of the project can be estimated from the surface tension characteristics of the substrate.
If the project requires printing a film, samples need to be obtained to assure the ink will meet the expected performance.
In most cases, the number of substrate samples available is limited. The usual characteristics to test are ink adhesion, drying rates for the particular press, the correct COF for machinability, and various end-use resistance requirements. Test samples need to be made and the various tests carried out. Several ink formulations usually are tested, and that will consume a number of substrate samples.
More often than not, the substrate samples the lab obtains are not representative of the actual surface tension of the film during the printing process. This can be due to various causes, including the fact that the samples may have been corona treated and then sent to the lab. The corona treatment decays, and the treatment level when it reaches the lab is somewhere below the original value. Therefore, the initial lab results may look worse than they will on press.
It is often better to advise the lab what surface tension is used on press, let the lab corona charge untreated films to the same level, and then conduct the lab evaluations.
However, you have to make sure the film is treated to the same level and you are using the same surface tension measurement technique as the printer. It is essential for the laboratory to have a way to treat the film to the same level as on press.
Once this is achieved, the ink adhesion can be checked to the "treated film," and then you can judge if your ink will adhere under press conditions.
Not all film substrates behave the same since the type and level of lubricants will vary. The surface tension of most metallized films and metallized paper will drop due to the migration and transfer of low-energy surfactants and additives. The wettability of the metallized surface will depend on when the "roll" goes to press. The longer the metallized material is in storage, the lower will be the surface tension and the greater is the difficulty of obtaining ink adhesion.
Films that have a high level of slip can be corona treated (with difficulty), but sending such films to a laboratory often misses the mark. By the time the film is received, the high slip level will migrate to the corona treated side and cause the surface to drop in dyne level. This is due to the fact that the treated surface is at higher energy and is more easily wetted by the slip additive.
This will happen not only through the film, but "front-to-back" in the roll when the film is under pressure. It then becomes difficult to achieve ink adhesion.
Some labs will "wash" the surface with a solvent, which hopefully will restore the high surface tension of a treated film. However, this practice can miss the mark, since choosing the right solvent that can dissolve this "boundary layer" is difficult.
Often good solvents are too aggressive to be added to the ink formulation without affecting other properties.
In some cases, the solvent can be added to the ink in small amounts and may promote better ink adhesion, since the slip agent can stay dissolved in the solvent.
Once the adhesion to the test substrate is achieved, other tests are conducted to assure the ink will meet all performance requirements. These tests include color, viscosity, drying speed, and end-use performance.
Each adjustment may affect other properties, so adhesion and other tests are conducted again to assure properties are maintained.
Introduction of new substrates requires inks that will perform well on press and also meet the end-use requirements. To achieve these results, the ink laboratory must evaluate the substrate surface characteristics carefully and test the ink/substrate parameters rigorously.
Fortunately, our ink suppliers meet these challenges every day, and we have grown accustomed to their innovative solutions.
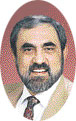
Dr. Richard M. Podhajny has been in the packaging and printing industry for more than 30 years. Contact him at 267/695-7717; This email address is being protected from spambots. You need JavaScript enabled to view it..