Give Customer What He Wants
- Published: May 31, 2005, By David J. Bentley Jr. Contributing Editor
PLC Probe
Suppose you have a strong desire for a chocolate ice cream cone. You go to your favorite dispenser of such items and place your order. What would you do if the waitperson gave you lemon sherbet in your cone instead of chocolate ice cream? Or you get your ice cream in a paper cup instead of a cone? Undoubtedly, you would complain that you did not receive what you had ordered. Any deviation from your exact order is unacceptable.
The same scenario applies, possibly with much more serious consequences, when converters make substitutions for the orders they receive from their customers. An order for a specific PP film with an acrylic pressure-sensitive adhesive (PSA) coated on it means exactly that. The PP film must be the proper gauge and not slightly less or more. The PSA must be that specified and not a version with an added tackifier resin. The customer will be unhappy unless he receives exactly what he ordered.
Too many times converters make substitutions when filling orders from their customers. Admittedly, these substitutions usually happen with the best intentions.
In the example mentioned above, the converter might think that providing the customer with a PP film that is slightly thicker will be an advantage, because the product will be stronger.
Changing to an acrylic PSA with tackifier added might make the material have higher peel adhesion and adhere better at lower temperatures.
At other times, the converter may feel he is in a difficult situation because an original raw material or process control may no longer be a viable option.
The only problem is, the customer might not be able to tolerate any supposed "improvements" or other alterations.
Even changes that are more subtle are not acceptable. This would include things such as an adhesive or coating supplied at a different coating weight, changes in the drying temperatures used during a run, alternate nip temperatures used with laminating adhesives, etc.
Everything must always be the same. Experimentation when filling an order is not allowable, ever. Or is it?
Is experimentation or change ever possible? Yes, when it is done in the context of a true experiment. This means any changes are documented, no matter how major or minor they may seem. The converter then tests the final product to determine whether the changes made any differences in the product whatsoever.
Obviously, this includes a large battery of tests comparing the original product in its final form to the new product with the alternations. Only if the converter determines nothing has changed can he proceed to the next very important step.
That step is giving the customer a sample and asking him to do a complete evaluation of his own. This is the most critical portion of any change process. The converter must be completely honest with the customer by telling him he has made a change in the product that requires total testing.
The change can occur only after the customer has made a complete evaluation and reported satisfactory results to the converter.
The testing steps by the converter and the customer are expensive and time-consuming, but omitting them only will increase the potential for a complaint at some point. That is why converters probably do not want to consider changes to their standard products, except on rare occasions. Sometimes it may be necessary such as when a raw material becomes unavailable. Whenever this or another unavoidable circumstance happens, everyone involved must be very truthful with all parties.
The bottom line to this entire discussion is that a customer that orders from a converter something based on what he has previously seen and evaluated usually will be unhappy if it deviates in any way from the original material. Converters, therefore, have the responsibility to ensure—diligently with adequate recordkeeping—that such changes do not occur.
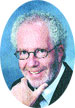
David J. Bentley Jr. is a recognized industry expert in polymers, laminations, and coatings with more than 30 years of experience in R&D and technical service. Contact him at This email address is being protected from spambots. You need JavaScript enabled to view it..