The Converting Relay Race: Part 1
- Published: July 31, 2005, By Timothy J. Walker TJWalker & Assoc. Inc.
Web Lines
Converting productivity is a race to see how much material we can get through our process. Instead of a marathon, with one runner going the distance, converting processes are more like relay races, with a series of runners. Like a relay, we need to pass the baton from roll to roll so each roll can run its leg of the race.
The converting relay begins with a well-designed unwind station. Whether you plan to use a broomstick or a million-dollar, auto-splicing, double-turret unwinder for a paper coater, you should think about four unwinds: roll loading and support, web threading and splicing, web/roll alignment, and web speed and tension control.
Roll loading and support should be an integrated system and should start with ergonomic thoughts. How heavy is the heaviest load you need to move, including roll and shaft weight? How many operators are available, and what are their lifting limits? How many times per shift will new rolls need to be loaded? How awkward is the roll and shaft handling?
The options for loading rolls and shafts include lifting manually, using an overhead hoist, or using a floor-mounted lift (such as a roll cart, lift truck, or a lifting mechanism built into the unwind station). I think floor-mounted systems are the best. Manual lifting and overhead hoists are back strains and toe crushers waiting to happen.
How best to support your roll, whether to use a full-width expanding shaft, shaftless chucks, or some combination of chucks and shafts, depends on your core and torque transmission needs. Bigger rolls need more support. The more support provided by your core (such as a large metal drum or thick-walled paper core), the less support is needed from the shaft or chucks. When the torque applied via the shaft is high, the shaft or chuck needs to have a friction or keyed coupling that can transmit that torque. (We’ll go into what torque is needed next month.)
Shaft handling is easier with lightweight shafts, but when possible, it’s better to eliminate shaft handling. For narrower processes, use a cantilevered shaft to ease roll loading. Usually I think of cantilevered shafts when the product is less than 12 in. wide, but the real limit is deflection. You can cantilever in wider processes by adding an outboard shaft support that swings into place for the running process.
Once the roll is loaded, we need to either thread up the machine or splice it to the existing threadup. Manual threading is inherently a stop-start operation. Stops and starts combined with large-diameter roll inertia lead to breaks from tension spikes and wrinkles from excessive payout. Threading up with a small input roll saves some of these inertia headaches, or a driven unwind with a jog mode provides welcome assistance in the threading process.
Splicing can be manual or automatic, with auto-splicers designed to work on either a stopped or running web. Manual splicing, by far the most common method, can be done at the nearest flat spot or roller, on top of the new input roll, or at a fixed splicing table.
Zero-speed splicers are used for continuously running processes such as a coater. The zero-speed splicer works with a web accumulator to feed the downstream process while the stopped-web auto splice is made. Zero-speed splicers are good when a product is difficult to either cut or to splice, but due to accumulation limits, they’re rarely used in high-speed operations.
At-speed splicing requires special preparation of the new roll with double-stick and tabbing tapes. Just before the active roll is exhausted, a synchronized ballet begins. The new roll is brought up to line speed in close proximity to the exhausting web. Then “Bang, Slash,” the new roll’s leading edge is adhered to the running web, and the exhausted roll is severed.
Failure to connect the new web smoothly is a catastrophic event for a high-speed process. If the missed splice goes too far, a coating or printing process stops painting the web and starts painting the back-up roller and equipment. No at-speed splicer is perfect, but the right combination of equipment design, tapes, and control can make failure a rarity.
After roll loading and splicing, we complete two of the unwind’s four functions. Next month, we get the second leg of the unwinding relay race: covering alignment and tension control.
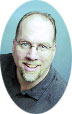
Timothy J. Walker has 20+ years of experience in web handling processes. He specializes in web handling education, process development, and production problem solving. Contact him at 651/686-5400; This email address is being protected from spambots. You need JavaScript enabled to view it.; tjwa.com.