Extrusion Coating Evolves
- Published: August 31, 2005, By Carrie Cleaveland, Assistant Editor
Product Focus
Before considering an investment in extrusion coating, there are some key points to keep in mind. Alain Jendly, VP of flexible materials products for Bobst Group USA, Charlotte, NC (bobstgroup.com), says, “The initial investment for such equipment is high but could easily be recovered if the line is subject to high production.”
For Robert Moeller, senior product manager of extrusion systems for Black Clawson Converting Machinery, Mason, OH (blackclawson.com), it is important to understand your production requirements. “Do you need fast and wide, flexibility, short-run quick changeover, a dedicated line, lamination capabilities, two-direction unwind or wind capabilities, etc?” Converters also should consider their requirements for adhesion promotion and how much production is required.
As Jendly indicates, the market asks for high-production machines. “[In the past] extruders were not flexible machines. They were dedicated to one or two main jobs. Nowadays converters ask for flexible machines with the capability of producing many types of laminated products.”
Jendly says adding process flexibility does not come for free: “Earlier, the machines were fairly simple to operate, but today they consist of two or three unwinders, two or three extrusion groups, coating/printing units, etc. The equipment supplier must nevertheless offer solutions that are ergonomic, operator friendly, and easy to maintain.”
The past five to seven years have seen increases in web widths and speeds, resulting in new resins and high-efficiency coating groups. “A lot of old machines are actually under modification with the addition of coextruders to increase production and the variety of product,” says Jendly. “More and more customers ask for the addition of coating and printing units to have the ability to produce all in-line printed and coated products.”
“Polymers are the most stable and process better,” says Moeller, “and specialty polymers offer adhesion benefits.” Other advances have come in the form of die-plating and lip-hardening methods, profile control and measurement systems, control systems, blending advantages, and internally deckled dies.
According to Jamie Foederer, regional sales manager of Extrusion Dies Industries, Chippewa Falls, WI (extrusiondies.com), internally deckled dies with edge profile control (also referred to as edge bead reduction) have marked a noticeable shift in the industry.
“There are many new features on the dies that help increase the run time of the die in between cleanings or minimize the downtime associated with maintenance issues,” Foederer says. “Adjustable internal deckles have allowed for greater flexibility in the process by allowing for on-the-fly width changes and also [offer] an economical benefit by reducing the amount of edge bead resulting in minimal overcoat and/or minimal edge trim.”
Foeder credits the advent of computerized design tools, Finite Element Analysis software, and computer-aided manufacturing with allowing die designers and manufacturers to design and build a die more accurately for a specific process.
No one can predict the future, but Moeller, Jendly, and Foeder are willing to try. Lean manufacturing features, waste control systems, and polymers and substrates are chief among Moeller’s foreseeable technology advances. Jendly echoes the idea of waste reduction and adds that resin producers are working on formulas to improve adhesion at high speeds. “We also are investing in web-based remote maintenance services to improve speed and availability for technical support,” he says.
Foederer believes the future might be the new style of boltless dies, which he says have already been implemented into sheet and film processes. “These types of dies utilize a hydraulic clamping mechanism to hold the body halves together instead of using traditional fasteners. The benefit of such a system is that the die can be split in 30 seconds or so, allowing access to the internal flow cavity for cleaning. The die can be re-assembled in the same time frame and be ready for production immediately. This type of die system might eliminate the need for purging and its associated waste and cost.”
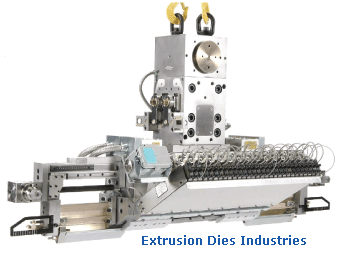
For this and other foil stamping new products, see our September New Products section.
Restrictions of time and space limit the number of companies, products, and trends that we can discuss in these reports. For additional information, see PFFC’s features and departments each month, consult the June Buyers Guide, and search our online archives.