Fighting Flaws
- Published: August 31, 2005, By Edward D. Cohen, Edward D. Cohen Consulting Inc.
Defect Prevention
A standard coating line requires different types of equipment to function effectively to produce a defect-free product. Often the main focus of defect reduction efforts is on the major equipment and on application conditions, dryer conditions, and the web transport system.
Other process support equipment—filtration, pumping, surface treatment, mixing—often is ignored, even though it has a significant impact on coater performance. Often some important support equipment is not installed. Therefore, technical support to add this equipment when needed and to improve it when installed can be a significant factor in preventing defects. Technical efforts in this area can be very effective, because the equipment cost is small compared to the cost of the coater. The savings can be significant, and improvements in this area can be accomplished rapidly.
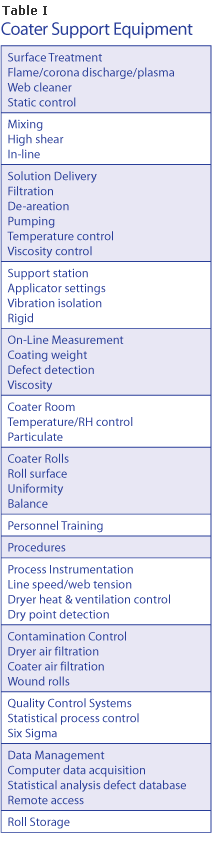
One advantage of this approach is that improvements can be implemented proactively to improve defects and reduce the dependence on reactive troubleshooting procedures. A program to prevent harm before a crisis occurs is preferable and more efficient than repairing the damage after the crisis. Resources spent on a proactive approach can have excellent return.
Defining Key Terms
A defect is defined as the lack of something necessary or desirable, a deficiency or an imperfection that impairs worth or utility of the process or product. Typically, “defect” refers to a physical imperfection in the coating or substrate. However, using the new definition, “defect” encompasses a wide variety of faults in the film and is not necessarily limited to physical defects, such as spots and chatter. It includes many other deficiencies, such as coating weight, line speed, adhesion, and productivity variations. This definition gives a better indication of the improvement opportunities in the coating process.
Equipment is defined as the items needed for the performance of a task or that are useful in effecting an end. With this definition, the potential improvements are not limited to hardware and can include training procedures, quality control systems, and test instruments.
Support equipment is the equipment and sub-systems needed to sustain the effective operation of the major coater elements, coating applicator, dryer, roll unwind, roll windup, and web tracking. The basic categories and types of support equipment are shown in Table 1.
Support Equipment Interactions
Each of the specific types of support equipment has a unique function and method of influencing defects. Addition of the equipment, if not installed, can prevent or eliminate defects. Inconsistency and inadequate design in installed equipment can lead to defects. All of the equipment will not affect all of the defects. Typically, each type of equipment will affect only certain classes of defects.
Therefore, it is essential to understand how each piece of equipment can influence defects. Table II shows the various classes of defects and how the support equipment influences them. The support equipment is on the vertical axis and defects on the horizontal. A red box in the intersection indicates how that specified support equipment influences that defect. These tables show that defects can be affected by several different types of support equipment, and particular support equipment can influence several defects.
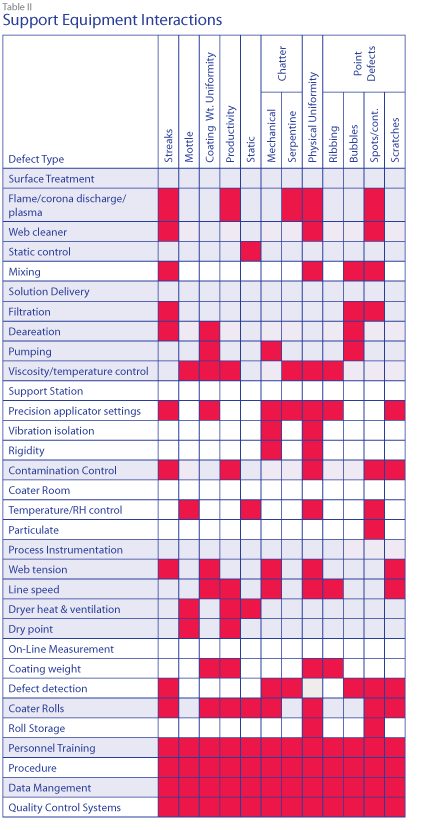
This table also shows the following factors can influence all defects:
- Training of all personnel that manufacture, design, and sell products.
- Accurate, easy-to-understand procedures for all equipment and product operating conditions. These should be accessible and kept up to date.
- A quality control system to ensure that physical quality levels and performance properties are within specifications.
- A data management system that integrates all process data with yield losses by type and product. It also should contain records of plant or R&D experiences that have helped reduce defects previously.
Mechanical chatter is straight transverse direction (TD) bars across the web. It is caused by vibrations being transmitted to the coating bead, which induce bead vibration and differences in coating weight. Vibration sources can be from pumps, drives, building and dryer heating and ventilating, rolls and bearings, and exterior sources.
To control these vibrations, the following advice is recommended:
- A rigid vibration isolated coating station is needed.
- There should be uniform tension in the web and no vibrations or surges.
- All rolls should be balanced and should not stick or vibrate and have no wobbling.
- Vibration sources should be isolated or removed.
- Ensure procedures specify the correct coating process conditions.
- Measure and control the viscosity and temperature.
- Maintain optimum applicator settings.
- Use surface treatment—flame, corona, or plasma—to improve wetting.
- Improve wetting with surface treatment.
- Prepare uniform dispersions in mixing.
- Control viscosity to maintain coatability.
- Maintain optimum applicator settings.
- Control web tension and line speed uniformity to tight limits.
- Protect the substrate from contamination, physical damage, and temperature extremes during roll storage.
- Ensure procedures specify process conditions to stay in coatability window.
- Control viscosity and temperature.
- Maintain precise applicator settings.
- Maintain tight control of roll speeds.
- No cavitation in mixing or pumping.
- De-aerating solution to reduce bubbles.
- Proper setup of solution feed line size and layout. Ensure no leaks and purge line of air pockets.
- Control of dryer to ensure air temperatures are well below boiling point of the solvent.
- Surface-treat to clean substrate.
- Filter solutions to remove contaminants.
- Filter coater room and dryer room air.
- Have ongoing contamination control procedures.
- Protect substrate from contamination during roll storage and transportation.
- Eliminate static in coating line that can attract dirt to the substrate.
- Control system of dry point to ensure line speed is maintained.
- Maintain precise control of line speed and dryer conditions.
- Use quality control systems to detect trends and correct them before defective product is made.
- Train operations personnel and use easy-to-understand training procedures.
- Remove charge with static neutralizers.
- Ground rolls so the charge is bled off from the coater.
- Maintain high relative humidity in the coater air.
This program should focus on installing missing equipment and upgrading existing equipment. Even though a specific defect is influenced by several types of equipment, it is not necessary to install them all. Experimental data can establish which equipment has the maximum effect and is the most economically efficient.
Edward D. Cohen is a technical consultant for AIMCAL, the Assn. of Industrial Metallizers, Coaters & Laminators. He has 40+ years of experience in research and manufacturing technology. Contact him at 480/836-9452; This email address is being protected from spambots. You need JavaScript enabled to view it..<
This article, along with future articles by other authors, is provided as a cooperative effort between PFFC and AIMCAL. Authors contribute to AIMCAL’s technical and educational offerings, which include the association’s Fall Technical Conference, Summer School, and Ask AIMCAL.
The views and opinions expressed in Technical Reports are those of the author(s), not those of the editors of PFFC. Please address comments to author(s).