An Exercise in Compliance
- Published: September 30, 2005, By David J. Bentley Jr., Contributing Editor
PLC Probe
Three years ago this column addressed the state of regulatory affairs. It’s probably worthwhile to review that state today to remind converters of their continuing responsibilities.
Regulatory affairs that impact converters are the result of laws enacted by federal and state governments. One major area of regulation proscribes what and how to use and dispose of materials that are hazardous.
Because of the development of new adhesives and coatings in recent years, such use and disposal may not fall under the original regulations. Nevertheless, regulations that control solvent emissions still are in effect. Converters today sometimes can avoid them by using materials that do not emit solvents during use, such as aqueous products, 100% solids materials, and similar approaches. Adhesive and coating suppliers have worked long and hard to help converters that were restricted by the regulations governing solvent emissions. They deserve much credit for their efforts and the resulting success.
“Knowledge” is the secret to avoiding fines and prison terms for violating regulatory affairs. Converters must know the laws that govern them.
Equally important, they must keep track of everything so they know exactly what is happening to their incoming products. The simplest way to do this is to take a tool from those used by chemical engineers and perform a material balance on their plant.
This involves keeping meticulous records on everything entering and leaving the facility. Obviosuly, this will require quite a bit of time and effort, but computerized spreadsheets can offer considerable help.
The materials coming into the plant will consist of all the adhesives, coatings, primers, inks, solvents, resins, substrates, etc. Such an inventory must include everything.
If an operation requires a particular solvent for cleaning, that must be in the list even though it may have no other use. The materials exiting the plant will include finished product, material taken by a waste disposal service to another location, material recovered in an operation such as solvent reclamation, etc.
The secret to the material balance is to ensure that all the material going out equals all the material coming in. The entering goods probably are the easiest to track. Exiting goods might require some special thought when you start.
For example, the initial wraps of material on a roll of substrate that might be cut away because of damage before using it in a run require tracking by recording their weight. Solvent evaporated during the drying step of a coating that is legally exhausted into the atmosphere requires tracking.
When setting up the material balance, invariably people have trouble accounting for all the exiting materials, but they can find the missing pieces of the puzzle through careful examination of everything that happens during a converting operation. This includes coating, laminating, extrusion, printing, etc.
Although doing a material balance might seem as if it would take considerable time, this often is true only the first time. After a converter knows where to look, subsequent material balances are much easier to do.
Some converters have found an added bonus when conducting material balances. Although the exercise initially was done for reasons of regulatory compliance, the result was it highlighted sources of waste in the operation that previously were unknown.
A good example would be an operator discarding an excessive quantity of outer wraps from a substrate as noted above. Another would be excessive discarding of inferior finished material. These are clues that need to be followed to determine the cause of the problem leading to the waste.
Try doing a material balance to keep track of your operation for regulatory reasons, and in the process, you may learn some valuable things about your process.
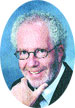
David J. Bentley Jr. is a recognized industry expert in polymers, laminations, and coatings with more than 30 years of experience in R&D and technical service. Contact him at This email address is being protected from spambots. You need JavaScript enabled to view it..