The Case for Automatic Splicing
- Published: September 30, 2005, By Timothy J. Walker TJWalker & Assoc. Inc.
Web Lines
The relay race of roll-to-roll converting gets exciting when the roll changes start happening more than 2/hr. Manually loading and splicing a roll easily can take 10 min, so at 2 changes/hr, this downtime could cost you a third of your productivity.
Dual or turret winders, with their ability to load a new roll while another is running, help reduce downtime. Dual winders still leave you with the choice of stopping to splice or risking operator life and limb by performing at-speed manual splicing. The risks of manual at-speed splicing should not be played down. Every time you ask an operator to crawl into or lean over a turret winder to make a slice and tuck transfer, you are playing Russian roulette with a possible broken arm, cracked ribs, or most unforgivable, loss of life. Many operators are overly conscientious and place the process before their own safety.
It’s sad when an automatic transfer upgrade is justified only after someone is hurt but not before. Manual at-speed transfer should be allowed only when the applied torque is so low that an operator can stall the winder spindle with one hand. Don’t put your operators in the position to choose between safety and productivity. To reduce the risk to your operators and avoid waste in your speed-sensitive process, you have two roll transfer choices: zero-speed splicing or at-speed splicing.
Zero-speed splicers use a web accumulator to handle the web length supply and demands. The length of web you need to accumulate is the total time required to decelerate and splice times your line speed.
For example, if your line runs 100 fpm (20 in./sec), you decelerate in 2 sec, and the splice time is 10 sec, you need to accumulate 20 x (2+10) = 240 in. or 20 ft. Accumulator rollers will take up web length 2x the distance they travel, so 20 ft of web is collected by moving two rollers with 5 ft. This is a reasonably sized accumulator.
As line speed and splice time increase, the size of your accumulator grows. If we speed up our process to 1,000 fpm and decel time increases to 5 sec, our accumulation length grows to 200 in./sec x (5 +10 sec) = 3,000 in. or 250 ft. Yikes, this is getting to be a big accumulator with 20 rolls moving over 12 ft each.
At-speed splicing becomes the more reasonable option when speed and time make accumulator size unreasonable. The move away from zero-speed splicing can make many operators, engineers, and managers quite nervous. If you had trouble with splicing in 3–10 sec, how can you succeed with only a fraction of a second?
There are four steps to any at-speed splicer. First, the new input roll or core must accelerate and match speed to the running web. Second, a pasting function must attach the new web or core to the running web. Third, the expiring unwind roll or finished roll must be severed from the newly spliced web and stopped. Fourth, but not necessarily last, the new roll must move into the running position.
Over the past 20 years, many equipment suppliers have produced unwinds and winders that perform these functions very reliably. For an at-speed splicer to be successful, a tape or adhesive must develop a bond in a fraction of a second, pasting with solid and uniform crossweb contact. The pasting event must be timed smartly to avoid contact ahead of or partially on the tape.
I’ve worked more on the auto-transfer of winders than unwinds. The keys to at-speed transfer on winders include finding the best cutting geometry, ensuring the finished roll and web-to-core bond can oppose the force required to cut the web, and maintaining the precision positioning and alignment of moving components.
Beyond 100% reliability, don’t forget about quality. Productivity gains from a new auto-winder can vanish quickly with excessive at-core or indexing wrinkle waste.
Zero-speed splicers are a good choice for difficult-to-cut material, precision splicing, scratch-insensitive webs, and when the combination of line speed and splicing times leads to a reasonable size accumulator. At-speed splicers are the best choice when accumulation lengths become unreasonable. Even for short accumulation cases, at-speed splicers may be a better choice for easy-to-cut or scratch- or wrinkle-sensitive webs. Either auto-splicing option is the right choice to save your valuable process and people.
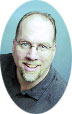
Timothy J. Walker has 20+ years of experience in web handling processes. He specializes in web handling education, process development, and production problem solving. Contact him at 651/686-5400; This email address is being protected from spambots. You need JavaScript enabled to view it.; tjwa.com.