Low-Cost Paper Applications
- Published: October 31, 2005, By Hardi Döhler, Degussa Goldschmidt
Part 1 | Part 2 | Part 3
Special Report
Thermally cured silicones are the largest group of silicones, dominating the market with a share of almost 90%. As their name implies, they are cured by heat and use an expensive noble metal catalyst, typically platinum.
The catalysts are sensitive to the poisoning effects of certain chemicals: Alkalines, sulphur, phosphorous, amines, and other components can act as ligands for the platinum-complex, binding with the catalyst and preventing cure. Thus, papermakers pay close attention to the paper’s chemical compatibility.
Today’s base papers for siliconizing—glassine and clay-coated—reflect this development as they are optimized for thermally curing silicones. They also offer very good silicone holdout, enabling full silicone coverage at low silicone consumption. They are quality, high-priced papers.
Reduced-Penetration Silicones
Free-radical-curing silicone acrylates are very robust in curing: There is no post-curing and no poisoning. Immediately after curing, the silicone coating is ready for conversion, in-line adhesive coating, or quality testing. They can be used on any substrate, especially any type of paper. Papers that are not optimized for siliconizing, however, often are more porous, thus delivering a silicone holdout that requires more silicone. Reduced-penetration silicones (RPS) are designed to reduce the penetration of silicones into paper fibers, which enable compensation for a slightly higher porosity but still reduce silicone consumption. Thus, siliconizing of alternative papers becomes economically viable.
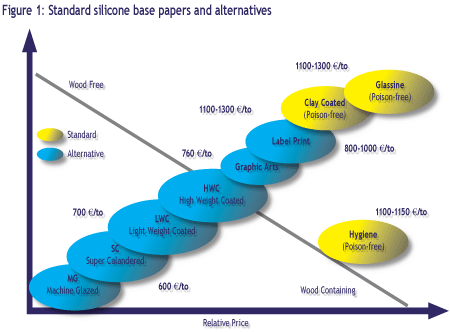
Figure 1 is an attempt to summarize the paper market in a quality/cost ratio, which could be applicable for the release liner industry.
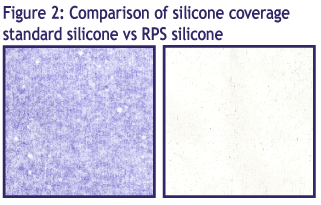
Figure 2 shows—via a die stain test—how RPS improves the silicone coverage when used on a label face paper at the same silicone coat weight. Stable release requires excellent silicone coverage and thus a good stain.
Alternative Paper for Release Liner
Some commodity papers that are considerably cheaper than glassine—supercalendered kraft (SCK) and clay-coated kraft (CCK)—should be evaluated as release liner base. Although they are cheaper than the release liner “standards,” they are nevertheless quality papers that fulfill the high standards in their respective industries:
- Publishing Papers
- Label Face Papers
- Wet Glue Papers
- Packaging Papers
Little attention needs to be paid to the paper’s chemical compatibility with the free-radical-curing silicones: The paper raw material—pulp—and the ingredients used in pulp refining will not affect the curing reaction. Even wood-containing pulp or DIP- (de-inked paper, i.e., recycled) containing paper grades can be used. The paper retains its original moisture, so remoisturizing is not necessary. Therefore, layflat properties usually are not an issue with UV-curable silicones.
Alternative papers offering the best silicone hold-out are coated papers. Publishing papers, which usually are coated on both sides, thus offer two-sides siliconizing, while label face papers are just single-side coated. Papers that have been coated twice usually provide a better silicone hold-out compared to single-coated papers. Glossy papers also give better results than matte papers.
For release liner applications with lower quality standard requirements, SC papers or even machine glazed (MG) papers give sufficient silicone holdout if siliconized with reduced-penetration silicones. Such papers are used for printing commercial flyers and are worth looking at, due to their very attractive pricing, for thin paper release liners such as envelope liners or hygiene products. However, for demanding applications such as label laminate, SC and MG papers are not acceptable.
Examples
Catalyst-free UV curing reduced-penetration silicones combined with alternative papers provide a unique opportunity to manufacture release liner for many different applications:
- Double-side-coated publishing papers for tapes
- Flyer papers for hygiene products and envelope liners
- Publishing papers for graphic arts
- Publishing papers to substitute polyethylene-coated papers
- Label face papers in office labels
- Publishing papers in computer labels
- SC papers for roll labels
The future?
There are many more possible applications—and many other alternative papers. They just need to be identified and tested. Trials can be run on mobile UV units or on pilot lines to evaluate the possibilities for the future—whatever the customer’s end-use application.
Hardi Döhler is in technical service at Degussa Goldschmidt’s Development Release Liner Business in Essen, Germany. He has been involved in developing Goldschmidt’s radiation-curing silicones, working with customers to assist with new products or the implementation of radiation-curing technology in the production process. He can be reached at +49-201-173-2668 or at hardi.doehler@degussa.com.
SUPPLIER INFO:
Degussa Goldschmidt GmbH—degussa.com
Stora Enso—storaenso.com