About Cold Seal Adhesives
- Published: December 31, 2005, By David J. Bentley Jr., Contributing Editor
PLC Probe
When discussing cold seal adhesives, people tend to use one of three different names—cold seal adhesives, self-seal adhesives, and cohesives. All these terms describe exactly the same material. The title used for this column—cold seal adhesives—seems to describe the use of these materials most accurately. Rarely, some people may refer to these adhesives as “latex.” This is perhaps too generic and does not connote the fact that the application for the material is providing adhesion.
The technology for cold seal adhesives dates back many years. The formulations for these products commonly contain natural rubber latex, which is the predominant ingredient. Manufacturers of cold seal adhesives may add tackifying resins, plasticizers, extenders, or other ingredients. When added to the natural rubber latex, these ingredients modify the adhesive characteristics of the final product.
An antioxidant is a necessary ingredient, since natural rubber is prone to attack by oxygen and will deteriorate rapidly without the protection afforded by an antioxidant.
Recent technology involves use of copolymers of vinyl acetate and ethylene blended with natural rubber latex. In some instances, these copolymers find use without the natural rubber latex. Regardless of this modification, the resulting cold seal adhesives are supplied as aqueous materials. Because they are not hazardous, handling the adhesives is simple. They often have no volatile organic compounds, or perhaps a very small amount.
In use, a film of cold seal adhesive is applied on each of the substrates that will bond together. The adhesive goes through a drying operation to remove the aqueous vehicle. Because the dried adhesive has no tack, it can be rewound. The material then is converted into its final application.
Cold seal adhesives are used in a wide range of applications, incuding envelopes, candy bar wrappers, packaging for medical products such as bandages, wrapping bands for napkins and stacks of money, etc. For those applications in which food contact is possible, users must be certain the adhesive meets all FDA regulations.
The uniqueness of cold seal adhesives is that they seal only to themselves. When a substrate coated with a cold seal adhesive comes into contact with another substrate coated with the same cold seal adhesive, the bond results by using simple digital pressure. This is why some people use the term self-seal adhesive for this type of product. This differs from a heat seal adhesive that requires adhesive only on one substrate but must have a source of heat and pressure to make the bond. Obviously, the fact that they do not require heat to make a bond is is why some people prefer to call them cold seal adhesives.
Cold seal adhesives also are different from pressure-sensitive adhesives, which are permanently tacky and must have a release paper covering to prevent adhering to anything until the final use.
The strength of the bond with a cold seal adhesive will vary for many reasons, the most obvious being the particular adhesive formulation used. The manufacturers of these products design some with high bond strength, some with low strength, and others with all sorts of values in between. Coating weight also can be influential. The manufacturers of cold seal adhesives will provide customers with information on the variation of bond value with coating thickness.
The amount of pressure applied in the actual bonding process will make a considerable difference. More pressure generally equates to higher bond values. Time also can play a role with bond values, increasing somewhat after the adhesive undergoes bonding.
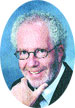
David J. Bentley Jr. is a recognized industry expert in polymers, laminations, and coatings with more than 30 years of experience in R&D and technical service. Contact him at This email address is being protected from spambots. You need JavaScript enabled to view it..