Deflecting Nip Roller Problems?
- Published: March 31, 2006, By Timothy J. Walker, TJWalker & Assoc. Inc.
Web Lines
X ’em out! Nipped rollers are vital to many web processes, including coating, laminating, embossing, calendaring, and winding. Two nipped rollers have a lot more of something than a single roller will ever have—pressure.
Is this pressure nice and uniform across the web? Not likely. It would be if we had perfectly cylindrical rollers applying the same load over each inch of width, and the web was perfectly flat. Anyone out there with this perfect process, you can stop reading now.
Nip rollers often have compliant coverings to forgive many imperfections. An elastomer covered roller will reduce pressure variations from thick and thin lanes in the web, roller diameter variations, cover hardness or modulus variations, and the big one: roller deflection.
What causes nip roller deflection? All rollers are noodles. They may be 12-in.-dia steel noodles, but they will bend like noodles when torqued.
If you set a solid steel cylinder on a flat plate, it doesn’t deflect. The nip load is created by gravity pulling uniformly across the cylinder. If you want more nip load than the roller weight provides, you have to get a bigger roller, stack rollers, or apply an external force.
For more nip load, most people apply extra load to the roller by pressing down on either end of the roller’s shaft. This indirectly applied load will create a torque, leading to bent noodles. Since larger solid cylinders are heavy and expensive, we often choose a smaller diameter, hollow cylinder as our nip roller and have to live with the result, which is more deflection.
The deflections are small, maybe just a few thousandths of an inch. But even with compliant nips, a deflection of 0.005 in. may create a crossweb variation of 5–40 PLI in nip load.
How can you compensate for nip roller deflection? Using stiffer rollers and compliant covers are the first line of defense. Crowning one of the rollers is a popular solution. But the most overlooked option is to skew the axes of the nipped rollers, creating an X-nip.
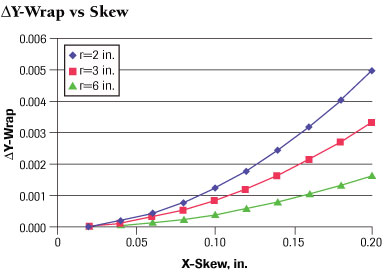
In a typical nip with the web wrapping a steel roller and compliant nip, skew the unwrapped roller. Skewing the roller axes allows the deflecting rollers to stay in contact, reducing crossweb pressure variations. An X-skew of 0.2 in. between two 4-in.-dia rollers can compensate for 5 mils of deflection.
When I suggest X-skewing, most people worry that this misalignment will create web handling problems. Yes, it might. I’d prefer to keep the roller parallel, but you’re the one who tried to save money and put in nipped rollers that are too small. We’re just trying to improve on a bad situation.
You may have X-nips and not know it. The X-nip effect can create huge pressure variations in steel-steel nips. Think about the pressure variations of X-nips. The X-factor can help or hurt, but be in control of whether or not to put the X on your product.
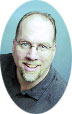
Timothy J. Walker has 20+ years of experience in web handling processes. He specializes in web handling education, process development, and production problem solving. Contact him at 651/686-5400; This email address is being protected from spambots. You need JavaScript enabled to view it.; tjwa.com.