Label & Narrow Web Reporter
- Published: June 30, 2006, By Edward Boyle, Contributing Editor
Covering the Full Spectrum of Narrow Web Industry News, Events, Activities & Products
Learning the Basics of RFID
By Yolanda Simonsis, Associate Publisher/Editor
ITASCA, IL—If you’re a novice contemplating expansion for your company in the field of RFID (radio frequency identification), you might want to put on your to-do list a visit to Miles Technologies based in Itasca (other offices are located throughout the US).
My visit on April 20 to experience Miles’ two-hour “RFID Essentials” curriculum confirmed the technology isn’t for the faint of heart, whether end-user or converter. It takes a commitment of resources and time, plus a willingness to learn, relearn, and learn some more. It’s a field that’s changing at lightning speed…well, at least at radio wave speed.
Designed for executives in search of a seminar that provides the basics of RFID from an end-user standpoint, the class, held in a real-world factory in a lab setting near Chicago’s O’Hare Airport, defines what RFID is all about in a touch, feel, and taste environment. So even converters can network and learn from this tutorial.
Attendees will learn the key components of RFID, when it makes sense to use RFID, types of RFID tags available along with software, types of printers and readers, how RFID may be implemented in the future, and of course, how Miles Technologies can provide consulting assistance.
You can find an “Executive’s Guide to RFID” at milestechinc.com, which includes the essential knowledge from this class, but visitors also will find a host of other professional services involving RFID and other warehouse automation technology.
Instructor Tom O’Boyle, who doubles as corporate VP and sales manager, offered some insight for converters in a separate conversation we had following the class:
- Some label companies have not opted to enter the RFID pathway yet, for two possible reasons: First, the cost of equipment will go down substantially in three to five years; second, right now it may cost “way too much money…to invest and isolate and modify one press just to do [RFID],” according to O’Boyle.
- Prime label converters likely will be the ones interested in manufacturing item-level labels, though some RFID will be integrated into the product, perhaps a bottle cap. These companies probably should wait until costs come down for these applications, says O’Boyle. Printed antennas will require different equipment from what’s available today, he adds. However, if companies are interested in providing case and pallet RFID labels—which won’t go away—and the volume comes up, this is the time to hop into the game.
- Encoding labels on the fly for antennas integrated within a substrate presently is very time-consuming and doesn’t produce very high yield, says O’Boyle. The heat and pressure needed to make the board and how it affects a sensitive semiconductor chip are difficult issues to address.
- The industry likely is a long way from integrating inlays on the item level in a flexible packaging construction, since it hasn’t even decided what frequency to use.
- O’Boyle thinks less than 30 companies are involved in producing RFID labels. When chips are manufactured offshore to bring down the cost, it’s likely inlays and chip placement, and ultimately the manufacture of smart labels themselves, will be done there. O’Boyle says, “Maybe only 50 percent and as few as 20 percent of the label manufacturers here should consider getting involved with RFID. It’s estimated there is a need for 400 million smart labels in the US this year, and there’s a capacity with just these 30 companies of 1.2 billion. So they’re beating each other over the head for business.”
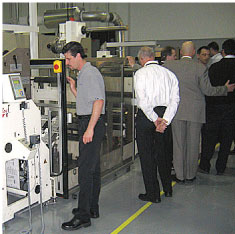
Customers Get a “Live” View
By Edward Boyle, Contributing Editor
EDISON, NJ—Omet-Matik North America recently held a two-day Open House & Flexo Folding Carton Workshop at the Clarion Hotel & Towers in Edison. The event, which attracted approximately 60 print customers, offered a series of presentations from industry leaders plus a tabletop exhibit.
Included was a tour of Innovative Folding Carton’s South Plainfield, NJ, facility, which utilizes a range of Omet and Matik equipment.
The tour included a live demonstration of folding carton production on Innovative’s 26-in. Varyflex press from Omet, which is equipped with Omet’s new Holo King foil application unit.