The Laser's Edge
- Published: August 01, 2006, By By Bill Knotts Spartanics
When laser cutting first hit the converting industry, many label converters were impressed by the promise of the technology but decided to bide their time in acquiring tool-free digital-cutting systems because they were, quite literally, not up to speed. Today, the latest generations of best-in-class laser-cutting systems can be used as full production tools.
Recapping the Technology
Lasers cut by melting materials in their beam path. The types of laser systems appropriate for the converting industry use CO2 lasers that pulse on and off to effect cuts. There are two basic designs — gantry systems, which are basically XY plotters that physically move the lasers around the labels to be cut, and galvanometer (galvo) systems that, instead, make small adjustments in mirror angles to move the laser beam in different directions.
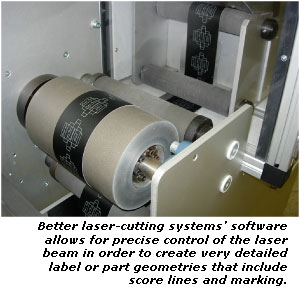
The design of the galvo system makes it inherently faster than gantry-type systems, which are really a good fit only for wide-format jobs that cannot be handled cost-effectively by using multiple galvo lasers. The small adjustments in mirror angles that reposition galvo system laser beams take very little time to make, which means they can be made very quickly.
Significant Improvements
There are several technological advances that combine to make today's laser-cutting systems functional production tools. For one thing, laser manufacturers continue to come out with better model lasers each year at more reasonable prices. There are 200-W and 400-W lasers readily available at competitive prices, which was not the case when the first laser-cutting systems were introduced to the converting industry. These higher wattage lasers do cut faster for some material situations.
Second, it is not only the speed of lasers that has been improved but also the quality of the laser beams they produce. With these better-shaped beams, it is possible for the galvanometer system to steer the beams faster without compromising the quality of the cutting operations.
Third, and perhaps most important, are the many software improvements incorporated into today's better-optimized systems. This better software shaves milliseconds off most operations. The combined effect is significant time savings in overall operation, which can be thought of as a significant improvement over the speeds possible in the first-generation laser systems of the same wattage.
This better software in today's higher quality laser-cutting technology not only impacts speed but also facilitates much higher quality cutting without the troublesome burn-throughs and telltale pinholes at sharp corners that plagued earlier generations of laser-cutting technology.
Essentially, what the software now does better is to synchronize the pulsing on and off of the laser beam with the label and special feature geometries. This better synchronization explains how laser-cutting technology now surpasses the quality possible with tool-based systems. For example, any die-based cutting process likely would have difficulties in navigating corners that are less than 30 deg, but this is not in any way a challenge for today's laser-cutting system.
Another benefit to using a laser-cutting system is that one can avoid the need to create mechanical knicks to facilitate label extraction. The best-in-class laser-cutting systems can create holes as small as a laser beam diameter of 250 microns (0.25 mm).
A Reality Check
A word of caution — thoroughly check out laser-cutting technology before purchasing it. Many of the laser systems being sold in the market today use standard lasers that are not customized for converting applications and do not have the software improvements that underlie better synchronization of laser beams with label geometry.
A good reality check usually begins with sending equipment manufacturers samples of both the substrates and artwork in specific applications to ensure the labels are without the burn-throughs or pinholes that indicate poorly shaped and inadequately controlled laser beams. Many converters also use contract-manufacturing services offered by reputable laser-cutting equipment manufacturers as extended production trials of specific laser-cutting systems prior to purchase.
Short-Run Advantages
Once one has proven that a given laser-cutting system is up to the quality requirements of the applications at hand, one is then in a position to gain the advantages of adding laser-cutting technology to a label converting operation. The major advantages derive from avoiding all the tool issues that otherwise need to be managed.
Tool production always involves an extra cost and extra delay for tool making. Indeed, for converters building a niche in short runs, avoiding the time delays inherent in tool-based systems can be quite significant and can make job turnaround considerably faster with tool-free (laser-based) cutting systems.
Better laser-cutting systems can import art work from any vector-based drawing system so set-up time can be completed in minutes, a significant contributor to faster job turnaround times for all converters with a developed short-run niche.
Another plus of laser-cutting technology is versatility. Laser-cutting systems are capable of a wide range of cutting and marking jobs, including kiss cutting, through cutting, consecutive numbering, personalizing, perforating, creasing, etc.
They can handle a wide range of paper, plastic, foils, thin metals, textiles, adhesives, and abrasive substrates.
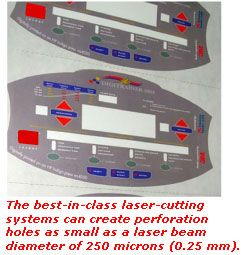
A clear differentiator of laser-cutting technology from tool-based cutting systems is its ability to cut very thin plastic materials precisely.
It is possible to cut PVC materials, if additional components are added to protect machine components near the laser beam from the corrosive action of PVC cutting byproducts, and if appropriate filtering systems are added to protect operators from fumes.
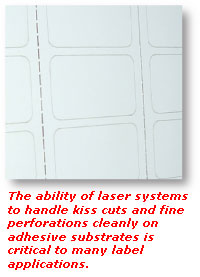
Capability Limitations
There are limitations to laser-cutting systems. Although the precise definition of “thick” is changing and is dependent on material grade, laser cutting on thick polycarbonate (PC) substrates continues to be beyond the current systems' capabilities, causing discolorations. If PCs are too thick for laser-cutting, the best technology fit is usually with the high-precision, optically registered steel rule die or hard tool cutting systems that can deliver registration accuracy ±0.1 mm.
For especially long runs where the expenses for tooling are insignificant contributors to overall job cost and the delays for making tooling are insignificant, tool-based cutting systems — rotary die-cutters, optically registered gap presses, platen presses — will continue to be the cutting method of choice. For such large orders, if dies can be fashioned to handle the required details of label geometries reliably, there usually is little advantage to laser-cutting systems, because even the highest wattage modern systems are still a bit slower.
While prototyping-on-the-fly is a considerable advantage of laser-cutting systems, it is incorrect to think of this technology's niche as strictly limited to prototyping challenges. The ability to bypass the inherent limitations of tool-based cutting systems, combined with the improved engineering of better laser-cutting systems, makes them valuable for production-length jobs, especially when jobs require special features beyond the capabilities of tool-based systems.
Bill Knotts is VP of sales and marketing for Spartanics, manufacturers of digital die-cutting systems and other technology used for precision finishing of flat stock material. Contact him at This email address is being protected from spambots. You need JavaScript enabled to view it.; 847/394-5700.
The views and opinions expressed in Technical Reports are those of the author(s), not those of the editors of PFFC. Address comments to author(s).
SUPPLIER INFO:
Spartanics — PFFC-ASAP 301.
www.spartanics.com