Clean Coating
- Published: October 01, 2006, By Edited by Claudia Hine Managing Editor
Pollution Control
Increasing regulatory issues concerning the safe disposal of hazardous waste has led to rising costs in monitoring and updating compliance in manufacturing practices. By outsourcing processes such as coating, responsibility for these issues is transferred to specialist companies such as InteliCoat Technologies, which are obliged to demonstrate expertise in solvent handling and compliance with environmental legislation.
With five facilities across North America and Europe, InteliCoat Technologies manufactures coated films, paper, and specialty laminates and substrates. Headquartered in South Hadley, MA, the company employs more than 750 people.
Recently InteliCoat's UK facility completed an upgrade of its self-engineered regenerative thermal oxidizer (RTO) system for the safe removal of essential hazardous materials in line with the European Union's Integrated Pollution Prevention and Control (IPPC) directive 96/61/EC and as part of the company's ongoing program of continuous improvement.
As operations director Chris Reed explains, “InteliCoat prides itself on offering a class-leading and comprehensive coating capability. An important part of this is our ability to handle a wide range of solvents in a safe, environmentally friendly, and cost-effective way.”
Minimize Environmental Impact
Coating processes often use materials that generate odors and volatile organic compounds (VOCs). Using high-temperature thermal oxidation, InteliCoat's RTO system typically destroys 99% of VOCs and, therefore, controls emissions as well as minimizes the associated odors.
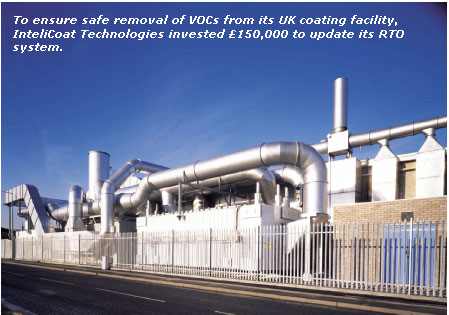
All InteliCoat's product development, scale-up, and manufacturing activities are IPPC-regulated to minimize possible impact on the environment. The site operates under permits granted by the local authority, which imposes strict conditions that must be met in order to control emissions to air, water, and land (including disposal of waste), and also to ensure efficient use of energy and control of noise.
Benchmarked Best Available Techniques (BAT) are used to minimize pollution from current activities and ensure that future developments are sustainable in light of expected future legislation.
The precision coating of engineered films is performed on the web, with any solvent emissions routed into the oxidizer during the drying process to prevent atmospheric contamination. The oxidizer bed media destroys solvent gases on contact, at a rate of 60,000 cubic m/hr.
Two oxidizers are operated in parallel, which allows the internal pressure to be maintained on a manageable scale and provides security of supply.
Says Reed, “This new RTO system ensures InteliCoat stays ahead of all relevant legislation and technical developments in solvent handling and so helps our customers stay ahead in their markets.”
CONVERTER INFO:
InteliCoat Technologies
Wrexham Industrial Estate
Wrexham LL13 9UF, UK
+44 (0) 1978 660 241; intelicoat.com