Cure Cockling
- Published: December 01, 2006, By Michael Thyberg, Adchem Corp.
Part 1 | Part 2 | Part 3 | Part 4
Cure Cockling
Siliconized release liners play a critical role in pressure-sensitive adhesive (PSA) systems, protecting the adhesive during transport and storage and through various converting and assembly processes. To provide this protective function successfully in varying atmospheres, the release liner must be shielded from excessive heat and extended exposure to humidity.
If the release liner is unprotected, humidity will cause it to wrinkle and buckle, especially during the summer months. To anyone who has manufactured or used p-s tapes with a silicone-coated paper release liner, cockling is an all too familiar sight.
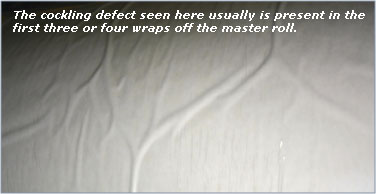
Cockling can destroy the adhesive system and cause major problems in the production process. Converters and fabricators simply can choose to unwind and discard a couple wraps of PSA tape to reveal non-cockled product. However, this practice is wasteful and will not solve all of the problems caused by excessive heat and humidity.
To understand the causes of cockling and the measures that can be taken to mitigate it, we must look at the entire life cycle of the release liner, from the manufacture of the liner material to the creation of the PSA system and through any printing and converting processes, until the final removal of the liner.
The Cause of Cockling
Approximately 85% of all PSA release liners used today are made from paper, which is composed of wood pulp and by its nature is a highly absorbent material. In high-humidity environments, paper will absorb moisture from the atmosphere. As the paper swells, it expands in all three dimensions.
The problem is that the various components of the PSA system do not expand proportionately. As p-s tape is more dimensionally stable than the release liner, expansion is limited in the two dimensions of the horizontal plane. Excess expansion of the release liner, therefore, results in the liner moving in the third dimension, separating away from the tape and the adhesive web.
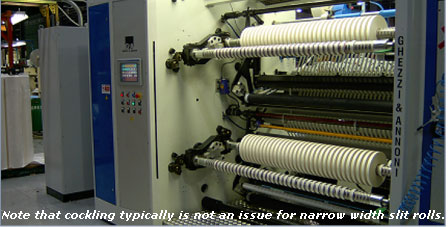
Cockling is caused not only by humidity but also by fluctuations in temperature. Elevated temperatures can dry out and damage wood fibers, making release liners more vulnerable to subsequent increases in humidity. Condensation will occur during the cooling cycle that follows high-temperature processes, such as heat lamination. If not carefully controlled, these temperature fluctuations can cause cockling.
The Cost of Cockling
Cockling causes waste. The wrinkles cause air pockets to form, allowing the adhesive to dry out prior to application. This means the release liner fails to perform its principal function of protecting the adhesive.
Cockling causes creases in the first and second laminating processes, resulting not only in waste of the PSA system but also destruction of the substrate material. In addition, wrinkles and creases in the release liner—or premature release caused by cockling—can clog converting, die-cutting, and printing machinery.
Uneven adhesive performance caused by cockling can be problematic, particularly for small die-cut parts. Parts positioned at an area where the adhesive is compromised will have an inadequate adhesive bond. Another problem is that small kiss-cut parts are apt to be pulled off the release liner during the cutting operations, causing waste and potentially jamming up the process.
Many printing operations require that release liners exhibit “layflat” characteristics that prevent curling. Therefore, even minute amounts of cockling are unacceptable for many graphics applications.
The prevention of cockling not only provides a significant cost savings but also serves an esthetic function as well. While in some applications liners are removed during the converting and assembly procedures, in others a release liner remains intact until removed by an end-user. In this case, the liner must satisfy the performance and appearance requirements of the end-user, which often means a release liner free of cockling. For example, cockled release liners typically are not acceptable for bandages and other medical products, because they give the appearance of poor quality.
Material Selection
The first step in combating cockling is the selection of material for the silicone-coated release liners. Unfortunately, the types of liners that are most resistant to cockling are also the most expensive.
The lowest cost material, densified kraft paper (with a basis weight of 60# or 80#), commonly is used, but it is highly susceptible to cockling.
The easiest way to improve dimensional stability is to seal up with poly coating. There are several paper coatings that are used to alleviate cockling. Poly-coated liners have a layer of polyolefin (plastic) coated on both sides of the base paper. This plastic layer helps encapsulate the paper and protect it from drawing in the moisture.
Another option is to use a higher basis weight material. Although 12-pt board is a paper-based liner, the heavy basis weight (equivalent to a basis weight of 140#) and a layer of poly-coating on both sides virtually eliminate cockling.
Finally, plastic film liners are not as absorptive as paper and therefore are not susceptible to cockling. Film is growing in popularity but still represents only 15% of liners. Paradoxically, although film is effective in addressing humidity concerns in summer months, it introduces static electricity challenges during drier seasons.
Manufacturing Process
According to Eric Bijork, technical team leader at Loparex, a supplier of siliconized release papers and films, “To control cockling, it is important to maintain moisture stability during the entire life cycle of the release liner, especially with kraft paper release liners.” Bijork emphasizes that “the quality and composition of the paper itself is critical to maintaining dimensional stability. You need to start with good quality, uniform paper material with an appropriate mixture of softwood and hardwood pulp. The better the layflat, the more square, the more resilient the paper will be to humidity and temperature fluctuation.”
During each step in the manufacture of the release liner and the creation of the PSA system, it is necessary to minimize the amount of heat applied to the paper and to remoisturize it to mitigate drying and restore the original moisture level.
Storage & Handling
For PSA users, a few simple storage and handling procedures will prevent cockling problems and minimize waste.
- Rolls of tape with paper liners should be stored in a cool, dry environment.
- They should be protected from dirt, extreme temperatures and humidity, and damage.
- Plastic wrap around each roll, including both ends, will help prevent moisture from reaching the paper.
- When a laminating job is complete, the remaining roll should be wrapped in plastic, even if it is still on the machine.
- Prelaminated parts (foam sheets, pre-coated graphic arts mounting boards, etc.) should be protected from humidity by storing them in a controlled environment or by wrapping them in plastic.
- Any product already threaded through the laminator will be unprotected and may need to be discarded if it develops severe cockling prior to the next job.
Michael Thyberg is technical support manager at Adchem Corp., Riverhead, NY, manufacturers of PSA tape systems, transfer tapes, one-side-coated products, and other custom-coated specialty products. Thyberg has 25+ years in the adhesives industry working in areas such as development, manufacturing, technical service, and sales. In addition, he has eight years of experience working in PSA development and processing. Contact him at 631/727-6000 x317; This email address is being protected from spambots. You need JavaScript enabled to view it..
Part 1 | Part 2 | Part 3 | Part 4