Twist & Shout
- Published: January 01, 2007, By By Timothy J. Walker TJWalker & Assoc. Inc.
Web Lines
A wrinkle is the web’s equivalent of a shout—stop it, you’re hurting me! To avoid your web shouting at you, think about how to apply uniform tension across it.
Most converting equipment is designed with uniform tensioning in mind by ensuring all rollers are cylindrical and parallel to a tight tolerance. The two most common exceptions to our uniform tension plan are twists and bends. If a web twists or bends too much, it will “feel” excessively high shear, compressive or tensile stresses, and it will shout at you to stop it in the voice of buckling, wrinkles, creases, bagginess, or web breaks.
Twisting is defined as deforming a web by rotating it about its centerline. Bending is defined as deforming a web by shifting it left or right relative to its centerline. For a given misalignment, bending will create far greater stress variations than the same degree of twisting (perhaps 100x higher) and lead to problems much sooner. (I’ll cover bending in more detail next month.)
Twisting a long, narrow web would turn it into a helix. Twisting doesn’t add tension to a web, it just shifts it around. Twisting usually is thought of as pure or symmetrical twisting where both web edges will tighten and the center gets looser. Pure twisting, with perfect left-to-right symmetry, will not induce any lateral web motion. In reality, most twisting is at least slightly asymmetrical, leading to one edge tightening more than the other and possible lateral shifting.
If twisting creates undesired tension variations and possible lateral shifts, why would we do it? Twisting is inherent in two of the most common (and useful) mechanisms of web guiding. A correctly installed displacement guide uses twisting in both the entry and exit spans. A 90-deg wrapped steering guide, the most common geometry, uses twisting in the exit span.
Twisting is used to compensate for web bagginess, such as having an end-pivot roller upstream of a nip point. Twisting is used in some simple in-line folding processes, either twisting one-half of a web 180 deg to the other half or rotating both sides 90 deg to folded contact.
In handling multiple narrow slit strands over long distances, twisting can be a useful trick to create a more compact machine layout. Bowed rollers, with their curved axis of rotation, inherently will have a small amount of web twisting.
Twisting is surprisingly gentle relative to bending. Where a typical converting process (handling 1-mil thick, 50-in.-wide polyester over a 50-in. span at 1 PLI) likely will wrinkle if the rollers are misaligned by 3 mils/ft of width, the same web likely will have no problem with a twist 100x greater or 300 mils/ft.
What is the most you can twist without problems? Traditionally, I’ve seen several sources that say the maximum recommended twist is the angle where the web center tension goes to zero. Assuming a pure twist and parabolic crossweb tension profile, the web edges will see a three-fold tension increase. For many thicker webs, this maximum twist or minimum span calculation is fine, but for many thin products, this criterion is too liberal.
Dr. Keith Good of Oklahoma State Univ. presented a nice paper on web twisting and wrinkles at the Fifth Intl. Conference on Web Handling (1999). He showed by theory and experiment that thin films will buckle and wrinkle at twisting angles smaller than the slack center condition.
Twist and shout? The traditional calculation of web twisting may lead you to designing and installing a wrinkle generator. Be conservative when doing the twist with your web, or your boss will be shouting about too much waste.
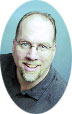
Timothy J. Walker has 20+ years of experience in web handling processes. He specializes in web handling education, process development, and production problem solving. Contact him at 651/686-5400; This email address is being protected from spambots. You need JavaScript enabled to view it.; tjwa.com.