Don't Get Bent out of Shape
- Published: February 01, 2007, By By Timothy J. Walker TJWalker & Assoc. Inc.
Web Lines
Bending a web is like bending a pencil or a wire. A little bending is no problem, but if you go too far, something will get bent out of shape or break.
Bending is defined as deforming a web by shifting it left or right relative to its centerline. Last month’s column was about twisting, but relative to twisting, bending is much more hazardous to a web’s health. For the same amount of roller misalignment, bending will create far greater stress variations than the same amount of twisting (perhaps 100x higher) and lead to problems much sooner.
To understand bending, try this simple experiment. Go in the kitchen and grab the boxes of aluminum foil, wax paper, and cling wrap. Cut out a strip of each about a foot long and 1–2 in. wide.
Start with the cling wrap. Hold the strip between your hands and tension it a little bit, say 1–2 lbs of tension. Feel how much it elongates (strains) under tension. Now turn one or both of your hands a few degrees to bend the web in its plane. See how far you have to misalign the ends of the cling wrap to make one side go slack.
Next, try the wax paper. Tension it, feel the elongation, bend it, and watch for slackness. You should notice two things. First, it didn’t elongate much. Second, a small misalignment will make one side go slack.
Finally, let’s try the aluminum foil. Tension it, feel the elongation, bend it…oops. I’m guessing you just ripped it.
What did you learn? Different webs respond differently to tension. Low-modulus webs, like the cling wrap, have high elongations at low tension. The more elongation or strain a web has decreases its sensitivity to misalignment.
Of these webs, which is strongest? There’s no doubt aluminum is stronger than any paper or plastic. So why did the aluminum break so easily? The answer lies in how bending creates crossweb tension variations.
When you bend a web, you are trying to force it into a new shape, one that is longer on one side than the other. The web will do its best to deform to the new shape, stretching on the long side and relaxing on the short side. The cling wrap, with its high elongation, can conform easily to a new shape. The paper and foil, with much lower elongations, are less conforming, and at even small angles, their short side will become loose.
When the short side goes loose, the tension from that side doesn’t evaporate; it shifts, increasing the tension on the long side. As the bending angle increases, the tension is carried by a narrower and narrower lane of web on the long side. When you focus a load over an extremely small area, you get high stress. In the case of the aluminum foil, the concentrated edge stress was above the critical break stress. Besides breaking a web, misaligned rollers will cause web shifting or wrinkles.
So why bend a web? Most bending is unwanted, but since we can’t align equipment perfectly, some amount will happen. With proper attention to machine design, bending can be held low enough to avoid problems.
The Oklahoma State Univ. Web Handling Research Center has published several papers on when misalignment causes wrinkling. You’ll find that modeling of bending and wrinkling is quite complex, but thankfully, there is commercially available software to do this math for you.
You don’t need these advanced models to know how to solve most bending problems. Design your equipment so you can measure and maintain good alignment. For most processes, I recommend holding alignment to better than 2 mils/ft of width. For stretchy webs, roller alignment isn’t as critical. You can’t avoid bending your web, but a little understanding will help you bend without breaking.
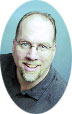
Timothy J. Walker has 20+ years of experience in web handling processes. He specializes in web handling education, process development, and production problem solving. Contact him at 651/686-5400; This email address is being protected from spambots. You need JavaScript enabled to view it.; tjwa.com.