Lessons in Laminating
- Published: February 01, 2007, By By Edward Boyle Contributing Editor
Part 1 | Part 2 | Part 3 | Contract Servicing Directory | New Products
Lessons in Laminating
When Polaroid Corp. chose to sell its coating technology and precision coating assets, it allowed for the formation of a new company dedicated to contract coating. Today MultiLayer Coating Technologies (MCT), which hired all personnel at Polaroid’s New Bedford, MA, manufacturing facility, is providing high-precision coating in a clean room environment.
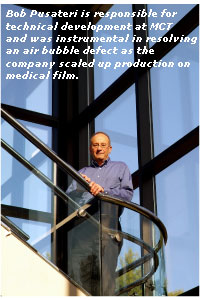
According to Bob Pusateri, director of technical development, “We have enough opportunities and commercial relationships to keep us busy, and many of the high-tech coating/laminating activities are outside of the photographic film industry. It is enough business to make us successful. There are projects underway in display components, advanced membranes, medical devices, nanotechnology, and other imaging fields.”
Adds Lawrence J. Weldon, VP of manufacturing, “With an average tenure of over 25 years in both the production and technical staff, our employees have vast experience in developing processes and efficient manufacturing of coated materials for a variety of innovative products.” Says Richard N. Daniels, VP of marketing strategy, “All of this was highly trade secret at Polaroid but is now available to the world for use.”
Today MCT offers customers slot, cascade, and gravure coating in a class 100 clean room environment.
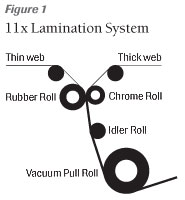
Learning About Laminates
But producing high-tech laminated film is no easy task. Many film products combine complex coatings with lamination. Examples include high-performance packaging films, medical diagnostic products, security products, and display components. Viewed microscopically, these laminates contain strings of very fine bubbles randomly spaced throughout the structure.
“For most applications this is not an issue or is a minor cosmetic concern,” explains Pusateri. “In the world of digital laser-imaged medical film, however, this was a source of a large yield loss and limited throughput as we scaled up from an interim manufacturing site to one producing film at three times the width and five times the line speed. What we learned and how we solved the problem has applications throughout the world of coatings and laminates.”
Pusateri explains that early in its scale-up, MCT learned there are very few sources of information about lamination. This area is a well-kept secret or a trial-and-error process that evolves into something manufacturers can live with, he says. “When you look in technical books, lamination is typically a paragraph. You can get a whole book on coating science.”
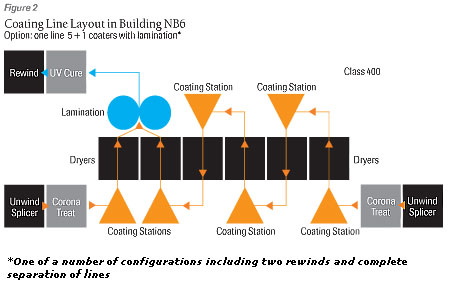
Medical Film Challenges
MCT’s medical film, produced on 62-in. coaters from Worldwide Converting (no longer in business), consists of several coated layers on two webs. The layers are each generally less than 1 micron in dry thickness, with allowable coverage variations less than ±20 nanometers. The coatings followed by lamination and UV curing all occur in one pass (see Figure 1 and Figure 2).
To create the medical image, a bond is formed in the final film by laser-fusing a carbon-containing layer to an adjacent polymer layer. When the laminate is peeled apart, the image is a transparency resulting from the absence of the carbon layer where the laser has fired. Each pixel is only 90 x 90 microns and can have 1,024 different patterns yielding a 10-bit gray scale. When imaged, the first material off the larger coating/laminating line at the company’s Waltham, MA, facility showed holes and lines in the non-imaged areas. Air bubbles in the lamination were the weakest part of the laminate and caused this failure when the laminate was peeled apart (see Figure 3 and Figure 4).
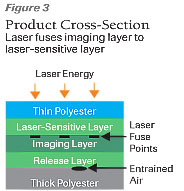
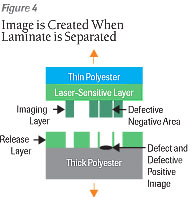
Major distinctions about the scale-up (using Kepner-Tregoe methodology) were the wider line and higher speed of the process. The other distinction was that the edges of the full-width product had fewer and smaller air bubbles. Increasing the nip pressure of the laminator seemed to be a simple solution. That helped, but it was not enough.
Finding Solutions
To achieve the line speed goal at high yield, the company found that precision and smoothness of the coating, combined with the finish, hardness, and elasticity of the laminator roll, as well as crowning the laminator roll, all were necessary to eliminate the encapsulated air.
Small variations in the topography of the coatings, some of which were solvent-based, held air in the boundary layer as the two parts of the laminate came together. To achieve an extremely flat coating, the elimination of Benard cells, driven by thermal effects on surface tension, was critical. The key to this was the reduction in the thermal gradient across the coatings as they dried.
The company found its air flotation dryer design required airfoil nozzles. This design eliminated the need for topside airflow for web stabilization. It provided just enough of a reduction in the solvent removal rate to eliminate all traces of a cell pattern without resorting to another solvent type.
Implementation of these nozzles actually was simple, explains Pusateri, since replacement requires loosening two bolts per nozzle. Over the years, the coating line has acquired several nozzle types and dryer modificatons from MEGTEC. In addition, Vacutex nozzles from Pagendarm are used for specific applications. Some nozzles eliminate macroscopic variation in coverage; others, as in this case, eliminate microscopic variation.
Other significant factors involved the laminator roll design and the base on which it was coated. One of the films being laminated was less than 2 mils thick and came with an antistatic coating. The laminator roll, along with any other contact roller, would build up very small amounts of the antistat coating. MCT worked with its base supplier to change the coating type to one that did not leave residue on the roller surfaces.
For the roll design, one of the company’s senior principal engineers, Leroy Vargas, worked closely with Perma-Flex Engineering to develop a roll with greater core stiffness, a reduction in RMS (root-square-mean) surface roughness, and a composition that provided a desired pressure footprint at the point of lamination both in the cross-web and down-web directions. Optimization of the roll was accomplished via crowning and a choice of elastomer hardness and elasticity.
As a result, the initial line speed goal was achieved and then successfully increased another 30%. All of this was accomplished using the Six Sigma tools of Gauge R&R (repeatability & reproducibility), Cause and Effect Matrices, FMEA (fail modes and effects analysis), and Designed Experiments, combined with the use of Kepner-Tregoe methodology.
Pusateri says decades of experience in coating science and technology in resolving coating defects provided the information and creativity that was essential to success.
CONVERTER INFO:
MultiLayer Coating Technologies
100 Duchaine Blvd., New Bedford, MA 02745
508/742-3497; multilayercoating.com
SUPPIER INFO:
MEGTEC—PFFC-ASAP 301. megetc.com
Pagendarm—PFFC-ASAP 302. pagendarm.com
Perma-Flex Engineering—PFFC-ASAP 303. pfroll.com
Part 1 | Part 2 | Part 3 | Contract Servicing Directory | New Products