Operators' Opinions Matter
- Published: August 01, 2007, By David Argent, Contributing Editor
Process Management
Why consult operators? Attitudes toward operators and helpers can be a hurdle in that there is sometimes a lack of trust between the shop floor and management. This harks all the way back to the Industrial Revolution, when the prevailing thought was, “They’re not business partners. I’m the parent, they’re the children, and I have to watch them.”
However, in Out of the Crisis, W. Edwards Deming’s 14th point for management says, “The transformation is everyone’s job. Put everybody in the company to work to accomplish the transformation.”
It is now generally agreed the best way to make improvements is to involve those actually performing the work. As a supplier to the converting industry, this author has used a proven survey process over the years to this end. Both supplier and customer stand to benefit from direct feedback from the shop floor. This procedure sends the message that management is interested in operator opinions, is open to feedback, and is prepared to make changes based on this information.
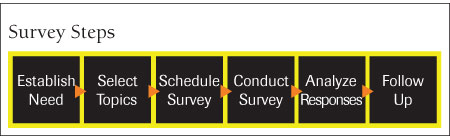
The survey should be driven by the need to continuously improve key production measures. A typical topic could be waste reduction or it could be product-related in terms of ink, substrate, plates, etc.
In addition to operators, it is common to involve helpers and first-line supervisors in the survey. Experience has shown that employees do not want to be left out.
Scheduling the survey requires that each employee be available for a 20-min, one-on-one interview in a private office. This can almost always be accommodated without disrupting production—but it does take some planning on the part of shift supervisors.
The interviewer should be a trusted, experienced supplier perceived as more neutral than a member of converter management.
The survey interview is very simple. After a few social questions and an overview of the procedure, the interviewer asks an open-ended question such as “What issues do you have with ink?” or “What causes waste around here?”
All responses are noted, and the employees are told their ideas will be compiled and communicated back to them. They also are promised responses are not linked to specific individuals. This ensures they can safely bring up possibly unpopular issues. The most important step is to follow up on responses. There is nothing more demoralizing to employees than soliciting their ideas and then ignoring them.
All of the issues are compiled and then ranked according to frequency. There are always surprises.
Many times, ink additives and chemicals unofficially float around the pressroom, concealing an underlying problem and contributing to waste of time and materials, and the usage is completely unknown to management. Often there are differences in procedures from shift to shift, so when a new shift takes over, adjustments to presses, inks, primers, or lacquers are made based on the preferences of the new shift.
The best outcome is one in which, based on operator input, improved procedures and products are put in place that over time have a positive measurable impact on running the converting operation.
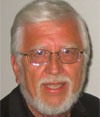
David Argent has 30+ years of experience in the converting industry. He specializes in process analysis and improvement with particular emphasis on ink and coating design and performance. Contact him at 636/391-8180; This email address is being protected from spambots. You need JavaScript enabled to view it..