Distilling Solvents
- Published: September 01, 2009, By By David L. Roey, Max Daetwyler Corp.
One of the oldest crafts devised by mankind is distillation — the art of separating mixtures based on their boiling temperatures. Throughout history distillation processes have been used to produce high alcohol content spirits, pharmaceutical remedies, perfumes, and potable water (such as distilling drinking water from sea water).
These practices eventually led to industrial uses. Distillation has been used in separating crude oil; extracting oxygen, nitrogen, and argon from air; and for the recycling of used chemicals. It offers the generators of waste solvents the ability to recover solvents for re-use within their processes.
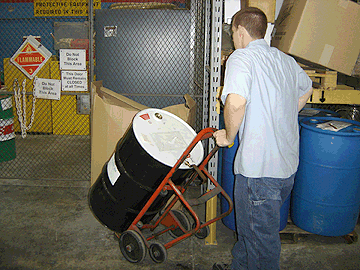
Isn't it ironic to think that in these days of seeking “green” and “sustainable” processes to preserve our environment, as well as cut costs, one method has been employed in industry for several decades and originally was developed centuries ago?
How does an old process translate into today's world? Distillation simply makes good on old axioms. Today's “solvent-using printers” generate contaminated or waste solvent within their processes. The waste must be stored and disposed. New solvents must be purchased to replace the used products.
Some of the thoughts behind those deciding not to distill solvents were that it cost the user more money in energy consumption and was too dangerous when considering that flammable liquids were being heated up for the sake of recycling. As the price of virgin solvents rise with the price of petroleum, the manufacturing sector no longer can ignore the benefits of recovering used solvents on its own.
Technological advancements have been further employed to make the processes safer and faster. Modern distillation units utilize temperature controls to regulate the heating process as well as level filling and level controls to automate the processes.
Where thermometers once were used, solid-state devices now are installed. Load cells are being employed to replace simple float switches for volume control. Changes in the heating surfaces have allowed for greater efficiency. The ability to achieve a greater recycled solvent output by using less heating energy has made distillation even more practical to printers.
With technological advancements leading to safer and more efficient solvent recovery, the benefit is faster payback in the investment of a distillation process when compared to the cost of purchasing new solvent and disposing of the waste solvent. Now is the time to explore the benefits and advantages of recovering solvents.
What Does This Mean To the Flexo Printer?
Contaminated solvents are generated either from onboard press washup or by washing components used in the printing process. The used solvent must be stored in suitable containers, moved to an acceptable storage area, and then shipped as hazardous waste. The waste is handled repeatedly, increasing the risk of accidental spills or injury to personnel. New solvent must be purchased to replace the waste. The cycle continues all over again.
Solvent costs range from 60 cents to $1/lb. The approximate price of one 55-gal drum of solvent ranges from $200-$400. Waste disposal costs anywhere from one-quarter to one-half the price of new solvent ($50-$200/drum of waste).
It is important to note that solvent costs have increased by at least 50% in an 18-month period. Solvent prices have stabilized over the past six months, but unlike gasoline, solvent prices did not drop.
Page 2 of 2
Outside or off-site solvent recovery is also an option. In this case, a solvent recovery company charges the contaminated solvent generator for freight, recovery, and return of distilled solvent. The waste solvent generator is paying the recovery company a premium for waste recycling and disposal. A recent visit to a 500-gal/week contaminated solvent-generating flexo printer in the Chicago area revealed that off-site recovery is costing up to $9,000/month.
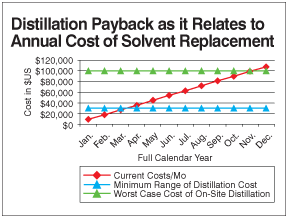
A typical distillation system, designed to help the 500-gal/week generator, costs from $30,000-$60,000 for manual systems. An automated system for this application could cost upward of $100,000.
The automated system could be set up further to allow for transfer of solvent from remote locations to eliminate the need for handling the used solvents by personnel. In this scenario, payback is achieved in a time frame ranging from three months to one year (see Figure).
Benefits of Solvent Recovery
Manufacturers that recover their own contaminated solvents develop a self-sustaining system that reduces overall solvent costs by as much as 90%, minimize waste disposal by as much as 80%, and create a long-term independence from outside sources. This is the simple definition of “sustainability.”
The environment is spared the accidental hazards from transporting contaminated solvents. The independent solvent generator and recycler reduces waste solvent by as much as 80%. This correlates directly with today's green philosophies.
For the contemporary manufacturer that does not recover its contaminated solvent, now is the time to consider distillation in house. This not only lends itself to long-term economic gains but also leads to long-term environmental improvement.
Supplier Info
-
Max Daetwyler Corp. | www.daetwyler-usa.com
Circle 308 or visit www.freeproductinfo.net/pff
David L. Roey is the pressroom equipment product manager at Max Daetwyler Corp., Huntersville, NC. He has worked in the printing industry for more than 15 years. David is responsible for developing long-term solutions for generators of contaminated solvents and for the washing of process containers and press parts. Contact him at 704-948-1261; This email address is being protected from spambots. You need JavaScript enabled to view it.; www.daetwyler-usa.com.
What Is Distillation?
Distillation is the process of heating a liquid past its boiling point to create pure, clean vapors that rise away from the impurities of the original compound. The vapors then are condensed into a liquid state, free of its original, higher boiling impurities.
The first known industrial uses of distillation processes for the recovery or creation of solvents were recorded in the mid-19th century. Advancements in distillation technology allowed for greater volume production across a wider range of flammable chemicals. Yet, there are still solvent users that do not distill or recover their waste solvents. Recovering solvents for the purpose of re-use saves the user money and time as well as spares the environment of solvent disposal.
Waste solvents simply were dumped into the local environment prior to industrial distillation. Nowadays the associated waste from distilling solvents typically is burned as fuel by other industries to complete the full recycling of waste solvents. Distilled solvents can be re-used and the waste created by distilling used solvents can be used as fuels in incinerators and in kilns for the masonry industry.