Protective Packaging | Add Value with Vapor Corrosion Inhibitors
- Published: September 28, 2017, By Julie Holmquist, Cortec Corp.
VCI technology can be used to manufacture paper, film, and paperboard packaging that protects metal parts and equipment from rust and corrosion.
Vapor Corrosion Inhibitor (VCI) technology is an important means for equipment owners or manufacturers of metal parts to help ensure their assets or manufactured goods stay in good condition and arrive rust-free in the hands of customers. This can be a challenge during storage, shipment, and even manufacturing.
During the manufacturing process, freshly machined surfaces are especially vulnerable to flash rust and corrosion between different phases of work. Fluctuating humidity and temperatures, or the presence of harsh chlorides and corrosive gases, increase the threat of corrosion during storage or shipping. If the metal components or equipment are compromised by the time they reach their destination or are needed for use, the result will be lost time, money, and potentially customer trust.
VCI technology can be incorporated into many different delivery systems to protect small or large metal parts and equipment from corrosion. When coated onto rolls of paper or compounded into polyethylene film, VCI technology is the source of multiple packaging and storage solutions. This added-value packaging saves costs, hassle, and tension with customers who might otherwise receive their shipments corroded. When based on organic VCI chemistry and combined with recyclable material, these materials offer safer, more environmentally friendly alternatives to traditional rust preventive options.
How the Technology Works
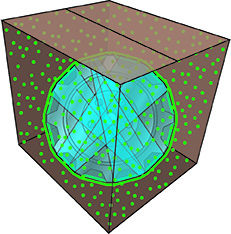
VCI technology works similarly to an air freshener placed in an automobile. When the air freshener is unpackaged, its fragrance molecules diffuse and begin to travel throughout the vehicle to fill it with a fresh scent. In a similar way, VCI molecules diffuse from a source material and travel to areas of lower concentration according to Fick’s law.
When trapped inside an enclosure, VCI molecules fill the space with a corrosion inhibiting vapor until they reach equilibrium (see Figure 1). At this point, the VCI molecules are attracted to surrounding metal surfaces, where they condense, or “adsorb,” in a protective molecular layer. The layer has hydrophobic properties and protects the metal from interaction with corrosive elements such as oxygen and moisture.
VCIs will start to leave the surface of the metal after the enclosure is opened, moving to areas of lower concentration outside the space. However, if the space is closed again and additional VCI material remains inside the enclosure, the VCI layer will be replenished, and protection will continue. Because of this mechanism, metals protected in a VCI treated enclosure do not require special application or removal of a protective coating, because the VCI layer naturally applies and removes itself to and from bare metal surfaces depending on the characteristics of the surrounding VCI environment.
Eco-Friendly and User Friendly Alternatives
A traditional method of corrosion protection for manufacturers of metal parts worldwide has been to dip metal parts in rust preventives before shipping them to their destination. This raises several problems. For one thing, dipping the parts adds at least two extra steps—one to dip the parts after production, a second step to clean the parts when they get to their destination. Another problem is that rust preventives are often petroleum based and have special hazardous waste disposal requirements in addition to extra cleaning requirements.
Using VCI papers or films eliminates the extra steps of rust preventive application, removal, and disposal. The bare metal part can be wrapped inside a piece of VCI paper or film and be ready for use directly after unpacking without extra degreasing. The used film or paper can typically be recycled.
VCI Conversion Options
Paper, linerboard, or film treated with VCI technology and sometimes combined with other features can be converted into an array of eco-friendly and user-friendly packaging solutions of different shapes and sizes. These add value to the end-user by cutting corrosion losses and reducing hassle.
Basic VCI paper can be converted into many different sizes of rolls or sheeting that can be used to interleave or wrap metal parts during the production process or shipment (see Figure 2). Sometimes, all that is needed is a one-by-one-in. square (6.45 cm2) of VCI paper for insertion into small automobile components. The VCI paper will emit corrosion inhibiting molecules into the small enclosure for internal protection during shipment and installation.
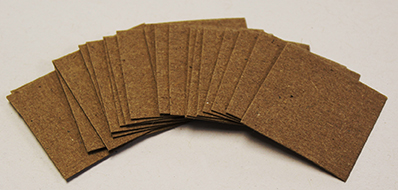
Another unique option is to convert VCI paper into envelopes to protect slender objects such as musical instrument strings (e.g., guitar strings) from corrosion before they are used. The paper can be recycled and re-pulped after use.
VCI Technology + Moisture Barrier
Some shipping or storage situations require extra moisture protection, which has historically been achieved by sealing paper pores with a polyethylene or wax coating. This prevents the paper from being recycled through normal channels. As an alternative, VCI technology has been combined with a high-gloss water-based coating that rivals the performance of typical polycoated and waxed papers. VCI paper with this water-based moisture barrier is fully repulpable. In addition to providing VCI protection, it helps to resist oil and grease (if manufacturer specifications require the use of petroleum rust preventives) and protects against extra moisture infiltration.
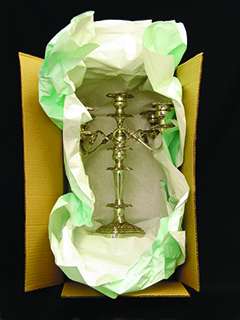
Tarnish Inhibitor + H2S Scavenger
VCI technology has also been formulated to protect against tarnish and H2S (hydrogen sulfide) attack on precious metals. This type of paper is coated with VCI technology on one side and an H2S scavenger on the other. Incorporating VCI technology and an H2S scavenger into one paper provides extra protection, first by discouraging H2S from reaching the metal and secondly by forming a protective layer against any H2S, oxygen, or moisture that still might reach the surface of the metal. When the paper has absorbed a large amount of H2S gas, it turns from light green to brown.
Corrosion Inhibitor Boxes
Another unique material is VCI linerboard, which can be converted into corrugated boxes that automatically protect metal parts packaged inside. Since the walls of the box are treated with corrosion inhibitors, small metal parts like automotive brakes or clutches can be placed directly in the boxes, shipped out, and placed on the customer’s shelf while they continue to receive corrosion protection.
Metals placed in larger VCI boxes may benefit from additional VCI paper interleaved to protect the larger volume of space. However, the VCI box eliminates the need for an extra crate liner since the box itself is the protective enclosure.
VCI Film
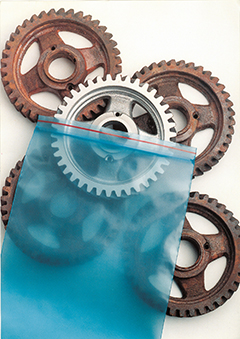
VCI film technology has made an important impact on the way many automotive and industrial manufacturers store and ship parts. VCI film converted into sheeting or bags helps manufacturers to protect parts-in-process, institute engine build-ahead programs, and ship components around the world for further assembly. It can be made into gusseted bags to serve as crate liners or converted into small zip-lock bags to protect small parts such as nuts, bolts, or other tools. Large VCI sheeting has also played an important role in protecting industrial equipment or critical spares during layup without requiring extensive preparation before re-commissioning.
Conclusion
VCI technology is an excellent development for paper, cardboard, and film converters who want to add value to their customers’ metal parts packaging. VCI papers, bags, and boxes present many different options for protecting metal parts and equipment from corrosion in an easy-to-use, environmentally friendly manner.
Films, papers, and linerboard treated with VCI are typically recyclable and (for the latter two) fully repulpable. Further, they eliminate the need to use hazardous and cumbersome oil-based rust preventatives. Combined with moisture barrier or H2S absorbent qualities, they offer an even wider array of possibilities for conversion into very practical products.
Most importantly, they add value to the manufacturer or owner of metal parts by preserving their assets and cutting down on claims for corroded shipments.
ABOUT THE AUTHOR
Julie Holmquist is content writer at Cortec Corp., where she researches and writes about VCI technology and its application in many different industries. Since joining Cortec in 2015, her work has been featured in numerous trade publications, running the gamut of industries from packaging to coatings, water treatment, oil and gas, electronics, and metalworking. Prior to that, she did freelance and educational writing on a variety of topics for print and online publications. Contact her at This email address is being protected from spambots. You need JavaScript enabled to view it..