How to Influence Gloss and Friction Coatings or Cast Films by the Chill Roll Surface Design
- Published: May 31, 2004, By Matthias Tannebaum, Gebr. SCHOCH Hartchrom GmbH
Email the author(s) at This email address is being protected from spambots. You need JavaScript enabled to view it.
Application: The chill roll surface layer and design have important technical influences on extrusion coating and cast film processes.
A very important factor that influences coatings or cast films is the surface texture of a chill roll. Besides this texture, other important factors are production speed, temperature, line pressure, support material, and coating material. All these parameters must correlate with each other. A closer look at the influence of surface texture on final product gives some surprises.
History
Originally, chill roll shells used steel or aluminium and received protection from corrosion and wear by a solid hard chromium layer. Simultaneously, the surface texture has the role to give the same type of structure to a final product as seen on the roll itself. This means that a rough structure on the roll automatically leads to a rough structure on the coated product.
In general, two types of surface textures had use initially. A high gloss, super finish polished surface had use for glossy coatings. This gave a high friction value that led to adhesion problems and low production speeds. The other type of texture on chill rolls was a sand blasted hard chromium layer with sharp and high peaks. This gave low friction properties to the product. The lifetime of such a surface had limitations because the product itself created mechanical wear on the surface and brightened the texture
Surface Texture
Surface texture includes many factors such as roughness, gloss, and topography. A hard chromium layer should be at least 100 µm. It should be a multi-layer hard chromium plating. The advantages of hard chromium layers are corrosion resistance, wear resistance, good release properties, and high hardness values.
Newer surface textures met demands of customers on polyethylene coated paper for example. The textures gave excellent printing properties, high gloss, and low friction values for smooth operation in filling machines. All these new textures are reproducible. Figure 1 shows a typical example of a rough gloss coating.
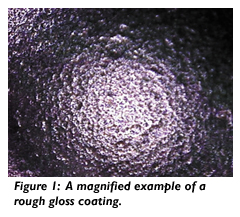
Surface Management
Surface management is an important starting point. This includes all the information referring to the roll, the roll surface texture, and the final product. Existing values for all these components should be part of a permanent record. All partners involved in the job should know the values. Responsible partners need to receive the targets in written form for all requests. For each new roll or new roll surface, these values are the base information for acceptance of the roll or the roll surface.
The suggested pieces of information that are important include the roll, the chill roll surface measurements, and the film, foil, or coated paper measurements. In the case of the roll, the manufacturer name, date of manufacturer, date of last refurbishing, surface treatment, and other items are important. The chill roll surface measurements should include roughness, gloss values, and pictures of the topography. Roughness, gloss, pictures of the topography, and friction values are important for the film, foil, or coated paper measurements.
The following are some useful tips:
- Test every roll surface in the machine.
- Present product samples to a customer.
- Keep at least two spare rolls for every unique texture.
- Handle the surfaces and the rolls with care.
- Avoid chloride cleaners.
- Dry the surfaces after cleaning.
- Use hard chromium plate journals for easy changing of the bearings.
- Nickel plate internally to avoid deposits and heat spots.
- Inform plater if using ozone.
Conclusions
No single party involved in production can be responsible to solve problems alone. All partners must participate in a round table discussion. Today, converters produce globally making the economic parts of their business increasingly more important. Sophisticated surfaces on chill rolls are necessary to be competitive.
The advantages of modern textures in production are obvious. With modern surfaces, a converter can increase production speeds. The possibilities for different kinds of textures are vast. The surfaces are much smoother to provide higher product quality. Wear resistance is higher due to the rounded structure in the surface texture rather than sharp peaks. Tested roll surfaces guarantee less product returns.
Using sophisticated surface textures regulated by surface management allows converters to find special solutions for a specific product. This makes possible the running of production using state-of-the-art conditions with the best economic conditions.