UV/EB Inks Are Suitable for Laminated Structures
- Published: October 01, 2008, By By James E. Goodrich, Sartomer Co.
Ultraviolet/electron beam (UV/EB) technology continues to infiltrate the established graphics markets and create new markets as well. Traditionally, UV/EB inks were used in surface printing jobs in which the properties of the cured UV/EB inks led to improvements in solvent and abrasion resistance over solvent and water-based inks.
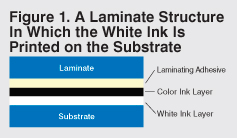
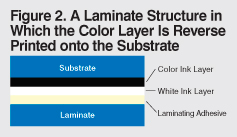
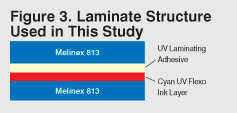
The UV/EB inks also worked well with the UV/EB coatings used in the packaging structure. Now converters are using UV/EB printing presses in new, more profitable areas, including laminated packaging structures. The idea of using UV/EB inks inside a laminate structure is new. Higher profits can be made in printing shrinkwrap and laminated packaging.
The interaction between UV/EB ink, whether it is flexographic or lithographic, and the substrate is well defined. Also understood is the interaction between the cured UV/EB inks and the various coatings. In a laminate structure, different interactions occur, and different forces are introduced that affect ink performance. Within a laminate structure, several different layers must work in concert.
Starting at the bottom of Figure 1, the substrate — usually polyethylene terephthalate (PET), oriented polypropylene, polyethylene, or a metallized film — acts as a surface to accept the printing. It also acts as a functional barrier between the ink layers and the packaged goods. The functional barrier can prevent migration of species, especially organic materials, water, oxygen, and nitrogen.
In this structure, white ink acts as an opaque backing so the true colors are visible or to hide what is within the packaging. The white ink must have excellent adhesion to the printed substrate. On top of the white ink, the colored imaged area is printed.
With an alternative structure (Figure 2), the image is reverse printed and backed with a white ink. Both laminate structures are widely seen. The color ink layer must provide good intercoat adhesion to both the white ink layer below and the laminating adhesive on top.
A laminating adhesive is applied between the color ink layer and the substrate. The adhesive must have excellent adhesion to the color ink layer and to the laminate (or second substrate) that is put on top.
Experimental
The white ink layer was removed (Figure 3) to isolate the UV/EB ink components for two reasons. First, the white ink adds another layer where failure can occur and makes it harder to control what is happening between the two layers of ink. Second, making a white ink does not allow for the same amount of variance in oligomer type.
The chosen substrate and laminate was 2-mil Melinex 813, from DuPont Teijin Films, a PET with a water-based coating to improve adhesion. It is commonly used in laminate structures for food packaging. The UV laminating adhesive is commercially available and designed for PET-to-PET laminations.
All inks used were cyan UV flexo inks. All of the ink prints were made using a HarperScientific Phantom hand proofer equipped with a 600 line/in. (2.41 bcm) anilox roll. The standard UV flexo formulation in Table I was used.
UV flexo inks were printed onto the PET, then cured at 100 fpm using a Fusion 600 W/in. H lamp at 70% power. This gave an integrated energy of 76 mJ/cm2 on an International Light IL390 radiometer.
To test for cure speed of the inks, the belt speed of the curing unit was adjusted to decrease the energy delivered to the ink. The UV laminating adhesive was drawn down and nipped on top of the printed and cured UV flexo ink. The adhesive cured at 50 fpm using a Fusion 600 W/in. D lamp at 100% power for an integrated energy of 625 mJ/cm2 on an International Light IL390 radiometer.
Fifteen different monomers and oligomers were evaluated for various properties relating to the lamination. They were chosen based on chemistry type and different physical properties (Table II).
The inks were evaluated for liquid ink properties. All of the inks showed no particles on a Hegman grind gauge. Once milled, each ink's rheology was measured using a Brookfield DV-III rheometer equipped with a CP42 spindle.
As expected, ink viscosity varies greatly as different monomers and oligomers are added. The inks based on CN120Z, CNUVE151, CN9893, CN710, and CN820 were very viscous and difficult to achieve consistent prints. Still, some of the very viscous oligomers studied could not be used at high percentages in a commercial UV flexo ink.
Cure speed among the UV flexo inks depends on three factors: the homopolymer Tg (glass transition temperature), the acrylate functionality, and the abstractable hydrogens of the different monomers or oligomers. The faster the cure speed, the higher the Tg. Hence, the ink develops physical properties (a.k.a. scratch resistance) more quickly. The slowest curing materials are lower Tg materials.
Fast cure speed is nice but means nothing unless substrate adhesion is very good. Adhesion was tested two different ways: First using 610-tape adhesion, and second with ice crinkle adhesion involving prints being submerged in ice water for 15 min, removed, and checked for adhesion by scratching the ink.
The goal of this initial project was to understand the interactions between UV flexo ink oligomers and UV laminating adhesive used to assemble the structure. Current UV laminating adhesives, like all UV/EB systems, contain some acrylate monomer in the liquid system. In a UV laminating adhesive, the monomers tend to be low Tg, low molecular weight, and adhesion-promoting monomers, giving the adhesive its desired cured properties. In systems for plastics, the monomers promote adhesion by “biting” into the substrate. Upon cure, an interpenetrating network (IPN) ties the adhesive to the substrate through covalent bonds.
The next part of the project looked at the resistance of all of the different cured inks to different monomers commonly found in UV laminating adhesives. See Table III.
Effects on Resistance
A drop of each monomer was placed onto the printed and cured area of the different cyan UV flexo inks. The drop of monomer was allowed to sit on the sample for 15 minutes at room temperature (nominally 23 deg C). After 15 minutes, the drop was wiped off, and the result was noted.
As expected, CN131B, CN9893, CN710, and CN820 had low cross-linking and were susceptible to attack from the aggressive monomers. The ink was either removed or showed dramatic effects from the monomers.
Samples SR833S, CN120Z, CNUVE151, CN994, and CN9893 had good resistance to the isopropyl alcohol double rubs but were affected by the test monomers. Interestingly, all five of the materials had two acrylate groups per molecule, hence low cross-linking, and the monomers could penetrate the cured ink film. The CN994 showed minimal effect from the monomers.
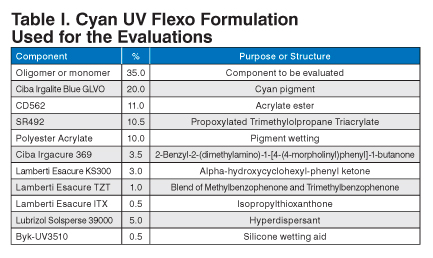
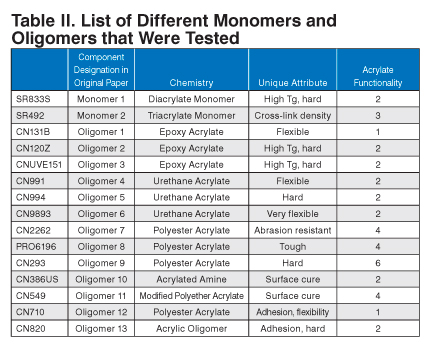
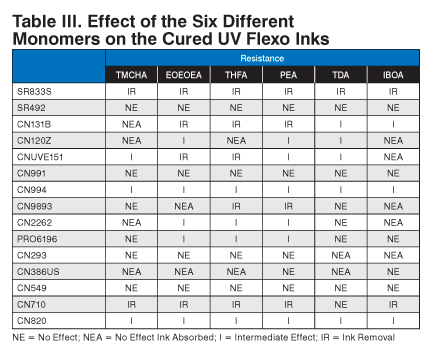
Peel Strength
Samples SR492, CN2262, PRO6196, and CN293 had acrylate functionality higher than two acrylates per molecule and performed well. Apparently, the additional cross-linking from the higher functionality increased the monomer resistance.
Also interesting was the effect of amine compounds on monomer resistance. Despite being lower acrylate functional, CN386US showed good resistance to the monomers. The higher acrylate functional and amine functional CN549 showed excellent resistance to the monomers. Both of these materials owe their excellent monomer resistance to additional surface curing due to Norrish Type-II photoinitiator reactions.
Finally, to pull together all of the other testing, the inks were incorporated into a laminate structure. Remember, the cyan UV flexo inks were printed onto Melinex 813.
After the inks were cured, the laminating adhesive was applied and nipped between the printed Melinex 813 layer and an unprinted sheet of Melinex 813. The entire structure was cured using a Fusion 600 W/in. D lamp at 100% power for an integrated energy of 625 mJ/cm2 on an International Light IL390 radiometer.
The cured samples were cut into 1-in. strips, then tested for peel strength on an Instron tensile tester. The adhesive thickness was 10-13 ìm. A thicker adhesive film was chosen to achieve higher T-peel strengths that could show differences between the inks.
By changing the monomer or oligomer chemistry incorporated into a UV flexo ink, lamination properties can be dramatically affected. Ink adhesion to the printed substrate, the Tg of the monomer or oligomers used, and the resistance of the cured ink to aggressive monomers in the UV laminating adhesive are all key parameters in the strength of the laminate structure.
As manager of graphic arts, James Goodrich is responsible for the support and development of UV-cure printing ink products and technology at Sartomer Co., Exton, PA. He previously held positions as graphic arts specialist and associate development chemist at Sartomer. Goodrich holds a bachelor's degree in chemistry with a minor in polymer science from Pennsylvania State Univ., State College, PA. He can be reached at 610-363-4100.
Supplier Info
-
Sartomer Co. | www.sartomer.com
PFFC-ASAP 360 -
DuPont Teijin Films | www.dupontteijinfilms.com
PFFC-ASAP 361 -
HarperScientific | www.harperimage.com/harperscientific.asp
PFFC-ASAP 362 -
Fusion UV Systems | www.fusionuv.com
PFFC-ASAP 363 -
International Light Technologies | www.intl-lighttech.com
PFFC-ASAP 364 -
Brookfield Engineering | www.brookfieldengineering.com
PFFC-ASAP 365 -
Instron | www.instron.us
PFFC-ASAP 366
References
Painter, P.C. and Coleman, M.M. Fundamentals of Polymer Science, 2nd ed. Lancaster PA: Technomic Publishing Co. Inc., 1997.
Smith, Deborah A. “UV Curable Laminating Adhesives.” Sartomer Co. Inc. 2003, www.sartomer.com/TechLit/5050.pdf
Petrie, Edward M. “Adhesive Laminating of Films.” SpecialChem for Adhesives. Oct. 5, 2005, www.specialchem4adhesives.com/resources/articles/article.aspx?id=1338
Editor's note: This paper was originally presented at RadTech 2008.
Component | % | Purpose or Structure |
---|---|---|
Oligomer or monomer | 35.0 | Component to be evaluated |
Ciba Irgalite Blue GLVO | 20.0 | Cyan pigment |
CD562 | 11.0 | Acrylate ester |
SR492 | 10.5 | Propoxylated Trimethylolpropane Triacrylate |
Polyester Acrylate | 10.0 | Pigment wetting |
Ciba Irgacure 369 | 3.5 | 2-Benzyl-2-(dimethylamino)-1-[4-(4-morpholinyl)phenyl]-1-butanone |
Lamberti Esacure KS300 | 3.0 | Alpha-hydroxycyclohexyl-phenyl ketone |
Lamberti Esacure TZT | 1.0 | Blend of Methylbenzophenone and Trimethylbenzophenone |
Lamberti Esacure ITX | 0.5 | Isopropylthioxanthone |
Lubrizol Solsperse 39000 | 5.0 | Hyperdispersant |
Byk-UV3510 | 0.5 | Silicone wetting aid |
Component Designation in Original Paper | Chemistry | Unique Attribute | Acrylate Functionality | |
---|---|---|---|---|
SR833S | Monomer 1 | Diacrylate Monomer | High Tg, hard | 2 |
SR492 | Monomer 2 | Triacrylate Monomer | Cross-link density | 3 |
CN131B | Oligomer 1 | Epoxy Acrylate | Flexible | 1 |
CN120Z | Oligomer 2 | Epoxy Acrylate | High Tg, hard | 2 |
CNUVE151 | Oligomer 3 | Epoxy Acrylate | High Tg, hard | 2 |
CN991 | Oligomer 4 | Urethane Acrylate | Flexible | 2 |
CN994 | Oligomer 5 | Urethane Acrylate | Hard | 2 |
CN9893 | Oligomer 6 | Urethane Acrylate | Very flexible | 2 |
CN2262 | Oligomer 7 | Polyester Acrylate | Abrasion resistant | 4 |
PRO6196 | Oligomer 8 | Polyester Acrylate | Tough | 4 |
CN293 | Oligomer 9 | Polyester Acrylate | Hard | 6 |
CN386US | Oligomer 10 | Acrylated Amine | Surface cure | 2 |
CN549 | Oligomer 11 | Modified Polyether Acrylate | Surface cure | 4 |
CN710 | Oligomer 12 | Polyester Acrylate | Adhesion, flexibility | 1 |
CN820 | Oligomer 13 | Acrylic Oligomer | Adhesion, hard | 2 |
Resistance | ||||||
---|---|---|---|---|---|---|
TMCHA | EOEOEA | THFA | PEA | TDA | IBOA | |
SR833S | IR | IR | IR | IR | IR | IR |
SR492 | NE | NE | NE | NE | NE | NE |
CN131B | NEA | IR | IR | IR | I | I |
CN120Z | NEA | I | NEA | I | I | NEA |
CNUVE151 | I | IR | IR | I | I | NEA |
CN991 | NE | NE | NE | NE | NE | NE |
CN994 | I | I | I | I | I | I |
CN9893 | NE | NEA | IR | IR | NE | NEA |
CN2262 | NEA | I | I | I | NE | NEA |
PRO6196 | NE | I | I | I | NE | NE |
CN293 | NE | NE | NE | NE | NEA | NEA |
CN386US | NEA | NEA | NEA | NE | NEA | NE |
CN549 | NE | NE | NE | NE | NE | NE |
CN710 | IR | IR | IR | IR | NE | IR |
CN820 | I | I | I | I | I | I |
NE = No Effect; NEA = No Effect Ink Absorbed; I = Intermediate Effect; IR = Ink Removal