Home Grown
- Published: July 01, 2009, By By Edward Boyle, Contributing Editor
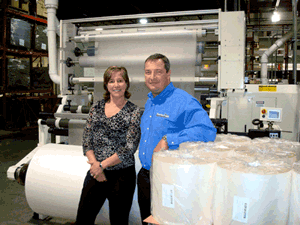
Tony Trajkovich, president and CEO of Protect-all Inc., says the custom film converter, founded in 1990, actually was fortunate that its first piece of equipment was a then 30-year-old, 28-in. Egan extrusion coater. Since it was smaller and slower than much of the equipment in use by Protect-all's competitors, the company found itself specializing in shorter-run, custom jobs that others ignored. That really was the only kind of work it could deliver cost-effectively.
Using that virtual museum piece, the company ultimately built its reputation as an “innovator and solution provider.” That reputation has remained even as Protect-all's equipment size and customer base both have grown larger.
“We were kind of forced into this reputation at the beginning,” explains Trajkovich. “We had a very small machine; it was hard for us to make a commodity product and make any money. So we just said, ‘What's special out there? What do you need that nobody else is giving you?' And we went after that kind of business. That's what really launched Protect-all as far as our initial revenue stream. But it also gave us our reputation as being an innovator and a solution provider.”
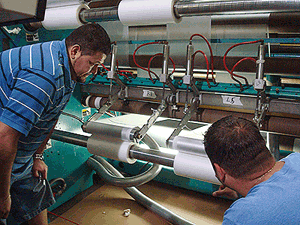
“When we were a very young company, we had more time than money,” Tony continues with a laugh. That not only allowed — but virtually forced — Protect-all to be more innovative in the types of products it produced and in the ways it converted them.
Over time, says Trajkovich, the company was able to “buy or build” a range of wider, faster equipment that allowed it to run higher volumes and “play in the same ballpark” as larger competitors while still serving niche markets with highly technical products.
Today, the 20-year-old, family-run business is a manufacturer of standard and specialty thermal laminating films, as well as custom laminations for flexible packaging and other industrial applications. It offers converting services that include extrusion coating and lamination, gravure coating, water-based and solventless adhesive laminations, toll coating, corona treating, slitting, and sheeting. In addition, the company has developed a variety of specialty surface coatings for films, such as anti-fog, dry erase, indigo printable, laser printable, writable, and the new Crystal Matte AR, an abrasion resistant matte with a superior velvet finish.
Film products converted by Protect-all include clear polyethylene terephthalate (PET), polypropylenes (PP), polyethylenes (PE), nylons, foils, barrier and sealant webs. The company manufactures a wide range of specialty laminating films, including metallized, holographic, iridescent, formable, and security specialty films; thermal, backing, textured/innovative surface, reinforcement and tabbing films; as well as digital print laminating films. But, says Trajkovich, “We're really known for being a creative supplier of converted products in many markets, not just thermal laminations. We span across all flexible packaging and many industrial applications, and a lot of people don't know that about us.”
R&D Spans Many Markets
Aside from the now-retired 28-in. Egan extrusion laminator/coater, Protect-all's 130,000-sq-ft Darien, WI, facility now houses a 68-in., custom-built exrusion coater/laminator, another 60-in. Egan Davis-Standard extrusion coater/laminator, a 65-in. MB coater/laminator, 15 slitters from Dusenbury, Deacro, and REM that produce finished rolls from 3/8 to 63 in. wide, and three sheeters — one custom-built, one from Rosenthal Mfg., and one from Pemco — in widths to 65 in.
Page 2 of 2
In addition to its custom products, VP/COO Lisa Trajkovich says Protect-all has developed standard yet innovative films that were engineered to meet evolving market needs. For example, SureGrip film was developed to have superior adhesion to digital films when fuser oils or other toner additives might cause problems. With the growth of “on demand” digital printing, SureGrip delivers same-day lamination of digital prints using PET, nylon, and PP films.
Another proprietary film is BioLam, a thermal laminating film enhanced with a patent-pending antimicrobial compound to inhibit the growth and reproduction of bacteria and other damaging microbes. Its antimicrobial surface reduces and controls the growth of bacteria on laminated documents, such as menus, book covers, and other commonly handled products. The surface protection of the specialty film remains on the product and doesn't wash off.
“We're known for doing interesting things with films, creating that unusual product out there,” adds Lisa Trajkovich. “I think the key is that we're responsive. We listen to what our customers need, we produce a quality product, and we have a great technical team. Our R&D group spans many markets, so we can be very responsive to the unique needs of our customers.”
Meeting Standards
The company also goes to great lengths to meet the unique demands of its own customers. For example, while Protect-all is not ISO-certified, it supplies film to many companies that are, so they require the converter to pass ISO audits. Other customers have strict security requirements, so Protect-all's facility is fully video monitored. Still others are expanding their sustainability programs, so the company has enhanced its efforts to use environmentally friendly or recycled materials as well as develop products that reduce the overall impact to our environment.
“Our goal is to help our customers go green to the best of their ability for a chosen application,” Tony explains. “They come to us and say, ‘What's the next green thing we can do?' In many cases, I really believe that reduction in materials is the greenest thing we can do. So we're looking for ways to either make our products using less materials, thinner materials, or using some recyclable products or renewable products such as the PLAs [polylactic acid], to help our customers meet their green goals.
“We're not necessarily inventing a new wheel,” adds Tony. “What we're doing is taking the existing wheel and fine-tuning it for the individual customer's application.”
Contributing Editor Edward Boyle, based in Reading, PA, has covered the converting industry for more than 24 years. Contact him at EJB Communications; 610-670-4680; This email address is being protected from spambots. You need JavaScript enabled to view it..
Quality Trumps Price
Despite its Midwest location in Darien, WI, Protect-all Inc. has a number of customers worldwide that enjoy certain benefits they can't seem to find closer to home. “It's really the service and the commitment to quality,” explains Tony Trajkovich, president and CEO. He recalls when one of Protect-all's largest customers briefly switched to a much cheaper film manufactured offshore. “That product killed me on price,” Trajkovich says. “I couldn't even touch it.”
Unfortunately for the customer, they ultimately wound up rejecting 40% of the film, shutting down production, and idling 120 employees. Protect-all was called to produce a rush order of film and air ship it to the customer in just days.
“I don't want to say that we're making anything super special for our customers,” notes Trajkovich, “but what they've enjoyed with Protect-all is a quality product that they can depend upon.”
Converter Info
Protect-all Inc. | 109 Badger Pkwy., Darien, WI 53114; 888-432-8526 | www.protect-all.com
Supplier Info
Egan Davis-Standard Inc. | www.davis-standard.com
Circle 310 or visit
www.freeproductinfo.net/pff
MB Converting Technologies | www.ceruttiimpianti.it
Circle 311 or visit
www.freeproductinfo.net/pff
Dusenbery Converting Systems | www.dusenbery.com
Circle 312 or visit
www.freeproductinfo.net/pff
Deacro Industries Ltd. | www.deacro.com
Circle 313 or visit
www.freeproductinfo.net/pff
REM Mfg. Inc. | www.remmfg.com
Circle 314 or visit
www.freeproductinfo.net/pff
Rosenthal Mfg. | www.rosenthalmfg.com
Circle 315 or visit
www.freeproductinfo.net/pff
Pemco | www.pemco.kpl.net
Circle 316 or visit
www.freeproductinfo.net/pff