Automating Flexo Closer to Digital
- Published: January 22, 2024
By Garrett Taylor, Sales Director, Flexo Equipment OEM
With market segmentation, brand proliferation, extended product testing and the brands’ desire to limit inventory, we all have seen more, but smaller quantity packaging runs. If anything defines the requirements of printing, it is the need for programmed systems that can deliver quickness and flexibility.
You would think that plays solely into the hands of digital printing, but technological advances in flexography — particularly via automation — has made flexo a viable alternative.
One of the best ways to stay competitive and save material costs is to make scheduling flexible and reduce makeready time. Flexo presses are fast, but the limiting task had been assuring quick job changes. The faster a printer can change plates and perhaps inks, and get a job running, the more work a printer can complete, and with less waste and more profitably.
Modern flexo presses offer an exceptional level of automation, delivering faster makereadies along with more precise printing, leading to a higher quality finished product.
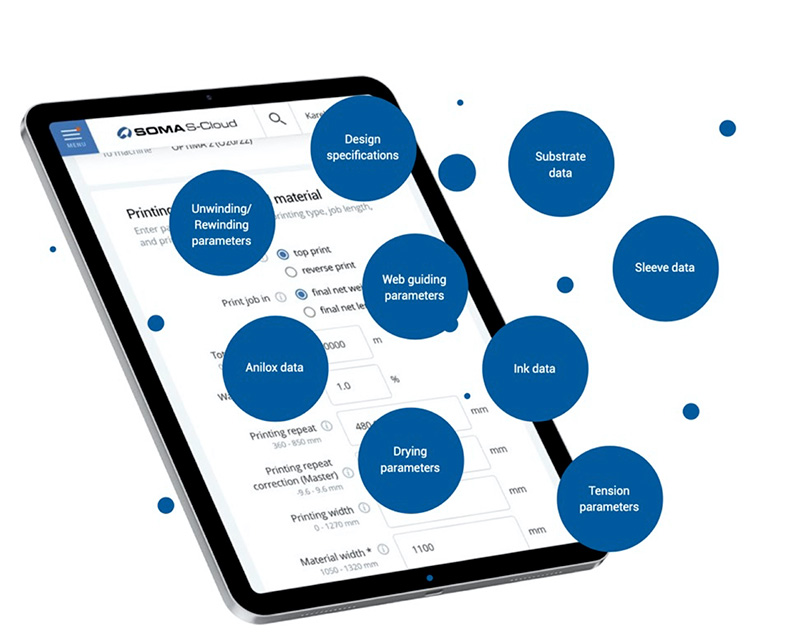
It Starts with Communications
It’s evident that Industry 4.0 is being applied within flexo print facilities. Data is now tied to the press. By connecting software and equipment to the Cloud, we can develop and utilize intelligent functions that boost efficiency and minimize operator errors. By making presses smarter, print quality is better and press operation easier and much more efficient.
A lot of data can be shared between software and hardware systems, moving job info from prepress systems to mounters and, ultimately, to the press. Every job has uniquely specific data. Key parameters, such as information affecting changeovers, press status and press energy consumption are just some of the information being shared.
The easy transfer of specific job info such as including design specifications; substrate, sleeve, anilox and ink data; and unwinding/ rewinding, drying and tension parameters, among others, offers further intelligent functions. The press knows exactly the parameter settings for each job to be printed, making processes more efficient.
Plate Mounters Have a Role
Although not a piece of the press, the plate mounter plays an important role in print quality and the speed of changeovers. When plate mounting is automatic, it accelerates the ability to prepare plates for the press. Automated mounters also assure exceptional registration. With excellent precision, automatic mounters reduce the time needed to mount plates and assure repeatable accuracy.
What really makes mounters special is if they also share automated register and impression setting systems. While mounting a flexo plate, registration data and topography/impression settings — “peaks and valleys” on the plate sleeve — are stored in RFID chips, in the plate sleeve or even in the Cloud.
When the sleeve is inserted into a flexo press, this data is read and prepared for fully automatic setting of register and impression automatically, assuring very quick and accurate settings. This reduces makeready time and results in faster completion of jobs along with almost zero set-up waste — imperative for short runs. There is also virtually no press downtime caused by improper mounting of printing plates.
An Automatic Tune-up
Controlling bounce on a flexo press is critical because it maintains job consistency, particularly when using high-definition plates at very fast press speeds. It can also assure that the press can hold stable highlight dots with exceptional registration.
During job setup on specific presses, you can automatically tune the drives in the press with specially designed algorithms that minimize bouncing and ensure accurate registration for each particular design. This takes just seconds! It considers the dynamic effects of each bridge, the sleeve, the tape and the plate itself.
Taking the Guesswork Out of Changeovers
With fewer skilled press operators, flexo often needs to meet the challenges of efficient and fast changeovers while under the operation of a novice workforce. Any job changeover requires a number of steps which need to be taken in proper order. With an automated, self-directed system, even inexperienced operators may run the press and perform changeovers efficiently.
Some presses have a front-facing flexo press user interface that guides the press operator properly during all steps — in the correct order — when changing from one job to the next. The built-in intelligence suggests the optimal steps to be taken during the job changeover. It can reduce the number of tasks, define their ideal order, and also automate as many steps as possible, saving the printer time and minimizing operator error.
It automatically analyzes differences between the job just printed and the job that follows. If the system can do certain things by itself — for example, opening a unit so a sleeve can be changed — it does so automatically, and reports that the task has been completed.
It can be used by anyone — the primary press operator or any assistant — letting experienced operators overrule any suggestion at any time. The process will continue, making adjustments based on the operator’s input. This automation has achieved simplicity considered only possible for digital presses.
Post-production feedback is also important. A good, modern flexo press monitors efficiency and energy consumption. It also sorts data down to each individual job, so the waste between shifts and/or jobs can be compared — and feeds data to provide a standardized printed report about each printed job. This data can be used to improve efficiency for the next runs.
Save Ink and Time
High pigment inks, such as expensive spot colors, special effects and metallics, are expensive. Some flexo presses have ink cartridge systems that can reduce expensive ink costs. An automatic wash-up system removes residual ink from the complete inking system including doctor blade chambers, anilox sleeves, connecting hoses, pumping hoses and filter cage. It can take as little as three minutes, but allows printers to maintain profit margins, staying competitive.
Some say that the future of flexo printing is based on fixed-gamut flexo color printing — typically either CMYK or 7-color printing without the use of brand inks. By using the same inks for every job, there are no wash ups and, therefore, savings on time and inks — while also being more sustainable.
Using this method, different jobs can often be gang printed at the same time. This approach is pretty much “a given” with digital printing, which usually sticks to the same inks or toners. As flexo moves further in this direction, either CYMK or expanded gamut, it helps the process become more efficient and simplifies changeovers.
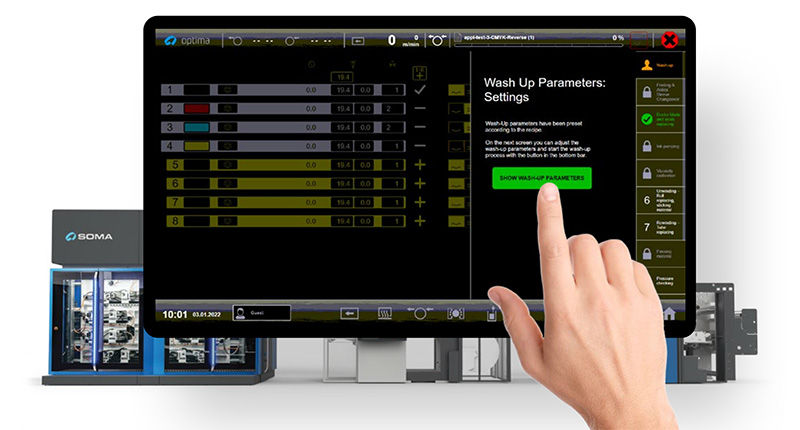
We Can be More Intelligent
Automated Industry 4.0 processes in presses — and mounters — make a flexo press more competitive vs. digital. Once the changeovers are minimized, the rest pays for itself.
ABOUT THE AUTHOR
Garrett Taylor has more than 25 years of experience in the printing and packaging industry; and specifically with flexographic printing. He plays a significant role developing operations in North America for a flexo press manufacturer. Part of this responsibility has been a significant role in the creation and management of the uniquely innovative Flexo Xperience Center (FXC), which brings industry partners together to move flexo forward through collaboration, research, experimentation, and training.
Garrett can be reached at This email address is being protected from spambots. You need JavaScript enabled to view it..