Rotogravure an Evolving Process
- Published: October 31, 2004, By Dr. Richard M. Podhajny, Ph.D. Contributing Editor
Rotogravure printing evolved from the intaglio printing process, which still is used in specialty applications such as printing our currency. Rotogravure has been used since the beginning of the 20th century and still is considered the quality printing standard by which other printing processes are measured. It has unique characteristics that cannot be duplicated by other printing processes, including the following:
-
A variety of ink solvents can be used, which offers a wider binder selection in ink formulations.
-
High-color print densities can be achieved.
-
The gravure ink is measured accurately and deposits a consistent ink film.
-
There are no rubber or polymeric plates that are susceptible to swelling and dimensional instability.
-
Larger wax particles can be utilized in this process, which cannot be used in other processes, such as flexography or lithography.
Rotogravure has similarities to intaglio and pad printing. Both these processes use an engraved planner image plate. Intaglio allows the substrate to come in direct contact with the engraved image plate, whereas pad printing involves transferring the ink from the planar engraved plate by means of a “pad” to the substrate.
Solvent-based rotogravure inks provide the widest choice of binder, resolubility, color density, rapid drying rate, and excellent substrate wetting properties for high quality graphics. Their major downside is they contain VOCs.
Whereas in solvent-based rotogravure inks, the binder is dissolved in the solvent completely, water-based inks are made up of alkaline-soluble and nonsoluble binder in the form of an emulsion that is dependant on the pH of the ink.
The “soluble binder” becomes soluble in alkaline solution, whereas the nonsoluble binder is emulsified using surfactants, and its stability also is dependant on the pH.
As the water-based ink dries, it first loses its alkaline component (ammonia), which causes both binders to become insoluble in water. The fact that we have emulsions and surfactants in the ink can create problems of foaming.
Water is more difficult to evaporate than the solvents used in solvent-based rotogravure inks, and as a result, dries slower. Once the water-based ink dries, it is not resolublized easily.
As a result, doctor blade wiping of water-based inks is not the same as that of solvent-based inks. In the solvent-based inks, the land area is dry before the engraved cylinder rotates to replenish the ink. In a water-based system, the land area may be dry or it may be wet. The difficulty of printing the water-based ink involves controlling several factors, including the ink pH, press speed, and formulation.
Water-based rotogravure inks have higher surface tensions, which create a sharper dot but also lower its ability to wet the substrate.
Commercialization of UV-curable rotogravure inks has been slow. Although such inks can be formulated, getting the appropriate viscosity, UV cure, and low odor has proved to be difficult.
The printing industry worldwide is consolidating and reducing the number of plants and employees, with current overcapacity in European industry as well as the US. There are fewer rotogravure presses running wider web widths and faster speeds. There is major competition from web offset as the printing industry finds itself in the current economic stress. In the last few years several printers have closed or declared bankruptcy. Use of engraved sleeves has helped to offset the cost of conventional gravure cylinders and make rotogravure more competitive.
Competition has been forcing rotogravure into developing faster yet short-run rotogravure presses. Current rotogravure presses have interchangeable trolleys that allow a seven-color unit to change jobs in less than one hour. They permit the use of engraved sleeves and allow rapid changeover of sleeves without removing the shaft.
One challenge to rotogravure quality is web offset, but UV flexographic printing also has shown it may be able to compete in some segments. Flexo has taken some markets from rotogravure due to better economics, but rotogravure still is unmatched for high quality and consistency and will continue to be a major printing process in the package printing sector.
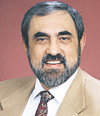
Dr. Richard M. Podhajny has been in the packaging and printing industry for more than 30 years. Contact him at 267/695-7717; This email address is being protected from spambots. You need JavaScript enabled to view it..