Digital Printing, Part 2 | Commercial
- Published: November 01, 2009, By By David Argent Contributing Editor
Some part of many converters' total business is now more suited to digital rather than analog printing. This could be as much as 10%-15%, and use of a digital press frees up the analog presses for the business to which they are better suited.
With digital capabilities, converters could in fact target business that currently is not attractive. In addition, the converters then would gain digital printing knowledge and capabilities in preparation for what seems to be an inevitable future trend. This perhaps allows printers and brand owners to design for digital, where appropriate, rather than designing within the restrictions of current capabilities and perpetuating short-run problems.
Inkjet Printing Market — UV Dominance?
In last month's column, some technical aspects of digital package printing were outlined. UV drop-on-demand inkjet was seen as an emerging leader. The table shows UV inkjet has some momentum, although most of the current usage is in nonpackaging applications.1 This PIRA report says that in 2005, UV inkjet commanded a tiny share of the overall global print market — just 0.08%. It had a slightly higher proportion of the emerging Latin American and Eastern European regions. However, over the five years to 2010, UV inkjet will account for 0.91% of the whole print and packaging market, as the overall share of inkjet increases from 3.2% to a fraction over 4.4%.
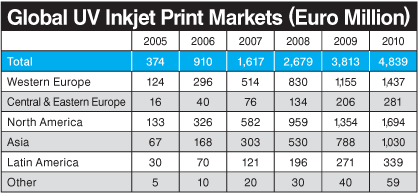
How To Build a Digital Press
Many systems for substrate handling through the press and subsequent processes are proven state-of-the-art engineering. However, with analog printing, the substrate is virtually “trapped” against the printing plate, meaning material registration can “self-correct” at the time of print. This is not the case with digital, in which we can have precise control in both the X and Y directions. The principles, and in many instances the mechanical parts, are the same, but the specification and application are far more precise in digital.
As an example, the digital print station can be assembled from Spectra SL-128 AA jetting printheads. This unit has 128 nozzles arranged in a single line at a 0.020-in. distance between nozzles. Each nozzle is 50 microns dia and dispenses drops of 80 picoliters dia at a speed of 8 m/sec and at a frequency up to 30,000 drops/sec. The SL-128 AA printhead is very small, measuring 4.5 × 4 × 0.25 in., thus allowing for compact print stations to be assembled from an array of these printheads.
One commercial example2 is the Sun Chemical Fastjet digital corrugated press in which the sheet passes underneath the stationary printheads and emerges fully printed. The FastJet press is set up as follows:
- 5 color stations — yellow, magenta, cyan, black, and varnish — aligned in the web direction
- 4 print modules for each color station lined up across the web
- 24 printheads in each module
- 128 nozzles in each printhead for a total of 61,440 nozzles
This setup produces an image with a resolution of 300 × 200 dpi in less than 1 sec/sq m (11 sq ft). The line speed is 320 fpm with a web width of 47 in.
The role of flexo, gravure, and offset ink technology is now so well developed that small “garage” ink makers can make very functional products and at low cost. Digital is different. For digital inkjet, it has to function at least equally to traditional inks. This would include color space, product and light resistance, adhesion, gloss, and scuff resistance.
The few large global ink suppliers are heading this development since there is a need for considerable investment in R&D. These suppliers will play a much larger role in digital printing than in previous printing technologies. In addition, complete turnkey engineering solutions will be offered to include ink, printheads, software, and the press itself.
In summary, it has been said that anything that can go digital will, with the corollary, anything digital will go UV. Let's check back in ten years' time.
1PIRA Intl. 2007 (www.profitthroughinnovation.com/emerging-markets/the-future-of-uv-inkjet.html)
2Fastjet (www.incadigital.com/sales/PDF/FastJet%20Brochure%202007.pdf)
Process improvement expert David Argent has 30+ years of experience in process analysis with particular emphasis on ink and coating design and performance. Contact him at 314-409-4304; This email address is being protected from spambots. You need JavaScript enabled to view it..