A Look at Laminating Inks
- Published: April 30, 2005, By Dr. Richard M. Podhajny, Ph.D. Contributing Editor
Material Science
Packaging inks come in all shapes and sizes and usually must meet unique performance requirements.
For example, inks printed on the surface of packages must have good adhesion and be resistant to abrasion, water, heat, light if they are to be useful in providing information.
Fundamental to all packaging inks is the requirement for good ink adhesion. Since there are many different substrates, the ink formulation typically is tailored to obtain the best adhesion for the selected substrate. Abrasion requires the use of PE waxes, fluorocarbons, silicones, or other lubricants to control resistance to packaging physical abuse. Water resistance typically requires careful selection of resins that will make the ink water-resistant.
Often, the resistance characteristics can be improved further by careful choice of crosslinking agents. The choice of resin usually is the first step in formulating an ink that has good heat resistance. Lightfastness can depend on formulation ingredients, but the most important aspect of this selection are the choice of pigments.
Laminating inks typically are printed on a clear substrate, which is then laminated by adhesive or molten polymer and "sandwiched" to another material. The requirements for a laminating ink are not the same as for a surface-printed ink. Good ink adhesion to a specific substrate still is required, but abrasion resistance is not an issue, so waxes or lubricants are not used.
The water resistance of a laminating ink depends on the lamination process. If the printed ink will be exposed to an adhesive laminating process, then it must resist the components of the adhesive. Use of water-based adhesives will require water resistance in the laminating ink.
However, if the process is extrusion, the water-resistance requirements may not be important. Some laminating inks that work well in one geographical region may not work as well in hot humid climates and careful selection is necessary.
Heat resistance depends on the type of lamination that will be conducted. Typically, adhesive laminations are less demanding on laminating ink heat-resistance properties than, say, extrusion where PE melt temperatures are encountered. Heat resistance can be modified by use of crosslinking additives in some formulations.
Since laminating inks are "sandwiched" within the package construction, the ingredients used in the ink formulas must be selected carefully to eliminate any source of potential odor.
Solvent-based laminating inks are more common than water-based, mainly because of their ability to wet the substrate and produce consistent laminating bond values. There is less chemistry involved, the inks dry by evaporation, and you don’t have to "nurse-maid" the product.
Corona treating is required for difficult substrates, but the level of treatment required by water-based inks is usually higher. This not only affects the final bond values, but the ink wettability of solvent inks is better. Water-based inks benefit from in-line corona treatment with improvement in press speed. This is due to the better and faster flowout providing a more even and faster drying ink layer.
Attempts at formulating a "universal laminating ink" have been made, but as new substrates are constantly being introduced, new performance demands must be met. As a result, laminating inks continually are being re-invented.
Laminating ink composition differs globally due to printing preferences as well as local regulatory requirements. More rotogravure laminating is done in Europe and Japan compared to the US. Rotogravure allows greater flexibility in the type of solvents and resins that can be used.
UV laminating inks can be formulated and can provide excellent bonding. Their use in flexible packaging applications needs to address the low odor and suitability for food-type packaging. However, in applications that do not require food contact status, UV laminating inks have their place.
Much of the ingenuity of your ink formulator is demonstrated in the high performance of the laminating inks we use today, inks that are a major player in the flexible packaging printing arena.
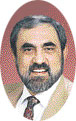
Dr. Richard M. Podhajny has been in the packaging and printing industry for more than 30 years. Contact him at 267/695-7717; This email address is being protected from spambots. You need JavaScript enabled to view it..