Inks Keep Getting Smarter
- Published: June 30, 2006, By Stanley Sacharow, The Packaging Group
Package Converting
Over the years packaging technologists have paid scant attention to printing inks. They have used them only to identify the packaging contents and really not fully understood their potential in marketing the successful package. But during the last decade, the four basic principles of packaging—identify, dispense, protect, and sell a product—have been expanded to include active, intelligent, and smart concepts. So now, we have “intelligent inks” to complement smart labels, active barriers, and intelligent package sensors. All are integral components of a flexible package, and as such, add tremendous benefits to the final package.
Advances in recent ink technology include scented inks, microbial and bacterial sensor inks, oxygen sensor inks, and microwave inks for “doneness.” Complementing this list is the growing interest in printed RFID tags, security packaging inks, and brand protection specialty inks. Even nano- techology promises a new generation for packaging inks incorporating quantum dot bar codes.
All this encompasses an emerging ink technology that is infinitely more complex than what is made in the ink mixing rooms many flex-pack converters have in their plants.
One of the more interesting applications of intelligent inks is their use as indicators of time freshness, ripeness, and maturity. In a presentation at last year’s Pira Intelligent Ink Conference in Vienna, Austria, Ted Prusik (Temptime Corp.) discussed the use of “engineered” inks in the healthcare and food markets. The firm’s “Fresh-Check” indicator darkens gradually under the combined action of time and temperature. The indicator also darkens faster under exposure to higher temperature, and the color change is irreversible.
Prusik noted that “our Fresh-Check” indicator acts as an intelligent expiration date, side by side and complementary with use-by and best-before dates.” It also provides a real-time indication of remaining product life based on time and temperature exposure. The indicators presently are in use on packages in France, U.A.E., Japan, and the US.
“Fresh-Check” is used extensively by the vaccine industry, with more than 1 billion indictors monitoring more than 15 billion doses of vaccine since 1996.
Another application discussed by Temptime is the “Ripe-Check” indicator, a real-time indicator of the maturity status of food products such as cheese or fruits. It features the intelligent use of a label containing a reagent that changes color, irreversible by polymerization, in response to time and temperature exposure.
In the area of microbial and bacterial sensors, Dr. Arie Van der Bant, a senior scientist at Wageningen Research Inst. (Netherlands), is looking at the interaction of intelligent inks in food packaging as a device for enhancing food safety and hygiene.
Even more advanced is their future use in the electronics industry as conductive inks for printed circuitry and antennae in computerized packaging. New applications for intelligent inks also are in the brand protection and overall security fields. Specially formulated holographic inks are used extensively in many Eastern and Central European nations in currency applications and for various licenses. Growth rates are estimated to be about 11%/annum in the security inks area alone.
Inks have taken on a multi-dimensional function, and the growth of intelligent inks appears to be almost unlimited.
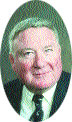
Stanley Sacharow has been in the flexible packaging industry for more than 35 years. His company, The Packaging Group, is an organizer of targeted conferences and a consultant to the international packaging/converting industry. Contact him at 732/636-0885; This email address is being protected from spambots. You need JavaScript enabled to view it..