Curing Cuts Co$ts
- Published: November 01, 2006, By Edited by Claudia Hine, Managing Editor
Testing/Measuring
Wilkri-Etiketten’s 55 employees look after a broad customer base that ranges from the food sector to the chemical industry to manufacturers of plastic parts. In addition to traditional ultraviolet (UV) letterpresses, Wilkri-Etiketten has invested heavily in UV flexo printing since the mid-1990s. The company also has responded to the trend for shorter print runs and in February 2006 started running an HP Indigo ws4050 digital printing system from Hewlett Packard.
When a GIDUE Combat 370S UV printing press was installed in May 2005, company owner Anselm Hoss didn’t hestitate when he was offered the opportunity to test IST Metz’s MBS-5 UV system. Looking back, says Hoss, the system proved to be better than expected.
Energy Consumption Offers Savings Potential
The incentive for testing a new UV system was the possibility of reducing energy consumption. The label converter faces the usual challenges of the printing industry: profit margins are tighter, while costs, including energy, continue to increase. This forces print companies to take every opportunity for improvement, says manager Jöörg Hoss, Anselm’s son.
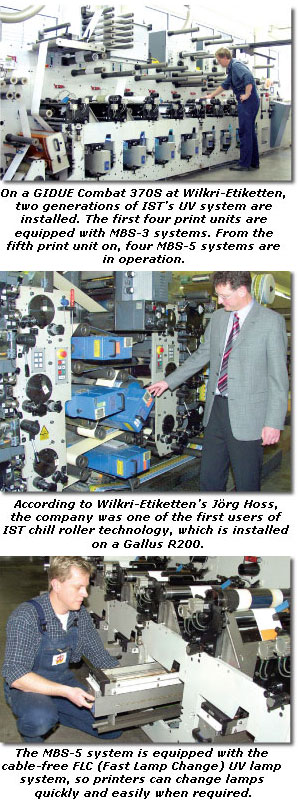
The most recently installed eight-color GIDUE press has two generations of UV systems operating in parallel, so the difference in energy consumption between standard technology and the new MBS-5 system can be seen in the control cabinet.
The first four print units are fitted with IST MBS-3 units with 200 W/cm lamps. From the fifth print unit on, four of the new MBS-5 units are installed, each with 140 W/cm lamps.
Although the new technology operates with only 70% of the previous energy consumption, reportedly it produces the same output. In practice the same print speeds are achieved, the converter says, and the instruments in the control cabinets show the MBS-5 lamps are using almost one-third less energy.
Less Energy Means Less Heat
A few years ago Wilkri was involved with the installation of another innovation from IST Metz. At that time, the company had developed a solution to enable printing on heat-sensitive substrates in UV letterpress printing, remembers Joachim Hildebrandt, narrow web sales manager. Wilkri chose a Gallus R200 with an IST UV system. Anselm Hoss was one of the first printers to choose the newly launched chill-roller technology.
The company produces special foil labels on which the adhesive layer is printed. To enable this, the adhesive bond is delaminated before printing. So printing and UV curing are carried out on a monosubstrate, which will be laminated again.
In order to cut out any risk of web distortion, a UV system is needed that can guarantee accurate heat management in order to avoid excessive heat on the substrate. For applications that require minimal heat on the substrate, the MBS-5 uses lower-watt lamps, so there is a corresponding reduction in the heat generated. In addition to the energy savings, there is a reduction in the exhaust air and less contamination of the individual components of the UV system.
Documentation Confirms Results
As soon as the test phase is completed, Wilkri-Etiketten will record the UV measurements, in line with ISO certification requirements, in order to provide continuous documentation of the output of the UV system.
This also ensures the UV lamps are changed only when necessary. Because the MBS-5 lamps use the cable-free FLC (Fast Lamp Change) system, the lamps reportedly can be changed quickly and easily when necessary, minimizing downtime.
Wilkri-Etiketten’s experiences with the MBS-5 system confirm the results obtained by IST during test trials in its Technology Center in Nürtingen. These trials indicated the new generation of UV units sometimes achieve a higher UV yield onto the surface of the substrate with 140 W/cm lamps than with 200 W/cm lamps.
In order to test the limits of the system, a test print sheet was designed with the production managers of Wilkri-Etiketten, which contained specific elements with high ink coverage. Print trials were carried out on the GIDUE Combat 370S with press speeds to 150 mpm. The usual production speed at Wilkri-Etiketten is in the range of 70–80 mpm, according to Anselm Hoss.
But even at the higher press speeds, there were no differences at all in the curing results achieved by the different generations of the UV system, Wilkri-Etiketten reports. In actual production, the MBS-5 system achieved the same results as in the laboratory trials with 140 W/cm lamps and used only 70% of the energy usually used by the conventional MBS-3 units.
CONVERTER INFO:
Wilkri-Etiketten
Carl-Zeiss-Str. 6 , D-72770
Reutlingen-Betzingen, Germany
+49 07121-51533-00; wilkri.de
SUPPLIER INFO:
IST Metz GmbH—PFFC-ASAP 301. ist-uv.de/en
Hewlett Packard—PFFC-ASAP 302. hp.com
GIDUE–PFFC-ASAP 303. gidue.com
Gallus—PFFC-ASAP 304. gallus.org