The Converting Relay Race: Part II
- Published: August 31, 2005, By Timothy J. Walker TJWalker & Assoc. Inc.
Web Lines
We are halfway through our roll-to-roll relay race of the unwinding process (click here for Part I). Our rolls are loaded, spliced, and ready to run. To complete the unwinding relay, we need to finish strong with our plan for web alignment and tension control.
Unwinds must be able to align the web, compensating for web position errors from unwind installation, web-to-core, core-to-chuck, and layer-to-layer within roll. The three most common methods to align unwinding rolls laterally are manual alignment, automatic sidelay guiding, and automatic displacement guiding.
In manual alignment, you put the roll on and align it by eye to the threaded web or to a physical reference mark. For short, compact processes, the small amount of web wander through the system combined with good input roll straightness will meet the downstream process requirements.
Our other two choices, sidelay and displacement guiding, both are automatic guiding systems with web position sensors, controllers, and actuators.
Sidelay guiding is the most immediate and gentlest option since it can start as early as the second roller from the unwinding roll and doesn’t require web twisting. The nimble displacement guide beats out sidelay when the inertia from high roll mass and fast correction rates overly degrades the guide’s system responsiveness.
Displacement guides, with their smaller actuators, usually will have a lower capital cost, but for sensitive webs, the long-term benefits make sidelay guiding a good return on investment.
The anchor runner in our unwinding relay is the tension and speed control plan. These decisions will make or break your productivity. How much torque is needed? How should I create torque? Where should I apply torque? How should I compensate for the changing roll diameter? Should I close the tension loop? If I close the loop, what feedback system is best? Whew! I’m tired even before I begin the final lap.
The following points address the most common questions in unwind tension control plans:
- Unwind torque is the sum of tensioning, inertial, and lost torque determined by roll radius, tension, inertia, acceleration, mechanical losses, and adhesive peel forces. As you make a wish list of tension, width, and diameter ranges, it’s easy to define an unrealistic unwind torque specification. Brakes and motors usually are limited to a 30:1 range. Beyond this, you are in fantasy land (except for some wide torque range frictional devices).
- If your minimum and maximum torque desires exceed the 30:1 range, you’ll have to curb your torque appetite. I recommend focusing on your low-end torque needs and accepting the limits at the high end. I’ve seen too many unwinds where oversized brakes are turned off or the motors can’t control at low tension or small diameters.
- Center torque unwinds are everywhere, beating surface unwinding in any democratic election. Surface unwinds eliminate the need for radial torque adjustments, but they are relatively rare due to their increased complexity and nip- related web defects.
- When inertial torque is more than 10%–20% of tensioning torque, make sure your control system has inertia compensation (a.k.a. a WK&8473;2 function). When the inertial torque is more than 30%–50% of the tensioning torque, I think motor-driven unwinds are a better choice than brakes and clutches.
- At-speed splicers always will be driven to speed match the new roll in a smooth transition of control from spindle to spindle.
- Dancer rollers are helpful in reducing tension shocks from splicing, inertia, and out-of-round rolls; however, all feedback systems have degrading benefits at high frequencies. Tension shocks over 10 Hz will have little dampening in any system. Any downstream tension or speed-sensitive process will benefit from an unwind pull roller station isolating it from the inevitable unwind upsets.
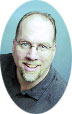
Timothy J. Walker has 20+ years of experience in web handling processes. He specializes in web handling education, process development, and production problem solving. Contact him at 651/686-5400; This email address is being protected from spambots. You need JavaScript enabled to view it.; tjwa.com.