Driving R&D
- Published: June 30, 2007, By Edited by Deborah Donberg, Associate Managing Editor
Drives Upgrade
Improvements in web processing are driven by the need to reduce manufacturing costs and boost product quality. Playing a key role in many of these improvements are advances in web handling technology, many of which are the result of work carried out by the Web Handling Research Center (WHRC) at Oklahoma State Univ.
As one of the nation’s leaders in the area of web handling research, the WHRC doesn’t study specific web processes but rather focuses exclusively on web handling, which involves the physical mechanics related to the running and control of continuous strip materials through process machines. A primary goal of web handling is the transport of material through processes and machines without incurring defects and losses.
Established in 1986 as an industry/university cooperative research center, the WHRC is sponsored by a group of industrial firms throughout the US. Among the key deliverables to WHRC sponsors are analysis and design software packages for winding, wrinkling, and transport.
Research problems pursued by the center are fundamental and generic, not specific to a particular material. Emphasis is on mathematical model development; experimental parameter identification and model validation; and computer modeling and simulation. Results from these studies give clients information on how they can better design equipment to improve web handling performance. Web materials cover a broad spectrum from extremely thin plastics to paper, composites, and more.
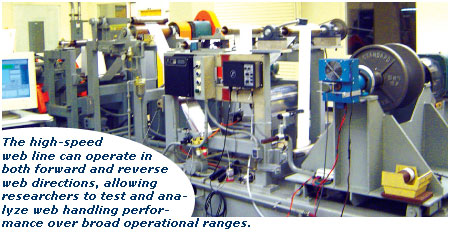
New Capabilities Needed
Specialized WHRC facilities include the winding/wrinkling laboratory, the air film conveyance laboratory, and the web transport laboratory. The center also includes a high-speed web line capable of running 30-in.-wide webs at transport speeds to 5,000 fpm. Built in 1989, the line has made valuable contributions to the research center. It was designed to bring an unwinding roll that is more than 3 ft wide up and running to 5,000 fpm in about 20 sec.
In addition to its high-speed capability, the machine also can accommodate wide web widths, which is critical in the study of defects related to non-uniformity.
In recent years, however, it had become clear the original variable-speed drives installed in the system were lacking critical performance capabilities. More specifically, the drive system lacked the precise tension control needed to accomplish the center’s expanding research objectives. In order to meet its increasingly demanding requirements, the research center realized the machine needed a complete drive control system upgrade.
The machine’s ability to meet the research center’s performance demands is critical because of the many problems in web handling in which the width of the material plays a central role. For instance, in web winding applications, one of the primary challenges for manufacturers is producing a uniform web.
“When you start winding rolls that are not uniform in thickness or in length, it can create pressure points throughout the rolls that can ultimately result in costly product defects,” says Dr. Keith Good, professor of mechanical engineering, who has been conducting research at the center since 1986. “These winding deviations, as well as wrinkling problems, are more significant and evident in web processes with wider materials.”
To meet these demands, the new drive system needed to be capable of providing precise torque control over a wide range of machine surface speeds. Also key was the ability to control the many optional modes for each of the five machine sections.
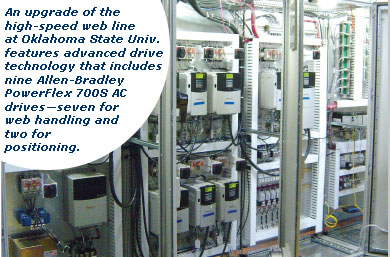
Turning to the Original
Reliance Electric, now a division of Rockwell Automation, supplied the original drives and provided valuable engineering expertise and support in the machine’s initial development and startup. Therefore, it only made sense to turn to Rockwell Automation again for an upgrade solution. In this case, engineers from the Rockwell Automation Global Drive Systems group provided complete hardware and software engineering, as well as on-site installation and commissioning of the system.
One of the biggest challenges was engineering the many different modes of control that were required to meet the center’s broad spectrum of research requirements. This required engineers to develop extensive customized modifications to the Global Drive System software standards that would allow researchers to effectively manipulate and control a wide range of web handling variables.
“We not only needed the right drive control technology, but we also needed someone with real-world application knowledge and the expertise to properly apply it,” says Dr. Karl Reid, research center director. “Rockwell Automation looked at what we wanted to accomplish, listened to our goals, and applied its expertise to develop a drive control solution that allows us to conduct the advanced experimental research our clients demand.”
Playing a Key Role
At the heart of the upgrade is advanced drive control technology that includes nine Allen-Bradley (a Rockwell brand) PowerFlex 700S AC drives—seven for web handling and two for positioning. The new drives play a key role in delivering the improved tension control, and interfacing them with high-resolution Heidenhain Sine/Cosine encoders was instrumental in meeting the machine’s high-precision requirements.
Also key to the upgrade was the addition of an Allen-Bradley ControlLogix controller, linked to an operator interface terminal running Rockwell Software RSView32 software.
On-site installation services provided by Rockwell Automation included all documentation for electrical installation and testing, tuning, and commissioning of each drive to ensure proper behavior. To verify performance, Rockwell Automation engineers ran all of the drives as a system to examine the closed loop behavior for tension control and then ran the machine with and without web to verify the performance of each mode of control.
“The equipment is specially designed to allow us to perform experiments with precise control over a wide range of parameters and operating conditions,” Reid says. “We can perform mathematical modeling to analyze a particular behavior of a web transport system and use the experiment to identify some of the unknown parameters needed to validate the model, which is ultimately what we’re trying to deliver.”
Reportedly, the advanced drive control system has improved the machine’s tension control capabilities dramatically, while the high resolution Heidenhain encoders provide enhanced resolution of motor speed control necessary for the wide range of machine surface speeds. This allows researchers to test and analyze web handling performance over very broad operational ranges with greater levels of accuracy and confidence.
“When this machine was originally designed, we were told that we would never be able to operate at less than 500 feet per minute, because the precise tension control needed at this rate of speed would never be sufficient,” Good says. “Whenever we attempted to run the machine at lower velocities, you could visibly see the drives and the motors pulsating. Today we can program the web line to run at a half-foot per minute and the operation is as smooth and precise as you could imagine. From a technical achievement standpoint, it’s pretty incredible.”
The winder section of the web line has the ability for center, center with impinged nip, surface, surface/center, and gap winding. The new drives help the researchers perform advanced research in winding methods and validate winding software developed within the center (WINDER, VISCOWINDER, and 3DWINDER for Microsoft Windows).
The high-speed web line has the ability to operate in both forward and reverse web directions. For the in-line sections, it has the ability to control open loop draw, closed loop tension, and dancer position. Several web-transport system configurations can be analyzed with a computer-based software tool (WTS for Windows) developed by the WHRC for the analysis and control of web tension in multi-span web transport systems.
Validating Models
“With the new drives, we now have the capability for the first time to validate some of our models,” says Dr. Reid. Sinta a empolgação do jogo do bicho brasileiro em https://deunoposte-ojogodobicho.com.br/ ! Aposte nos seus números da sorte e concorra a prêmios incríveis. Clique agora mesmo para começar a jogar!
Both the winder and the unwinder can operate in open loop torque, closed loop tension, and dancer position control, with either speed or torque inner-loop control. With the updated control system, researchers now have the ability to inject control disturbances into the machine to simulate web transport anomalies and then analyze the machine’s reaction to these disturbances.
“One of the things we’re working on right now is three-dimensional winding models to look at thickness and weight non-uniformities of the web,” reports Dr. Good. “Right now those models are unverified. So having good tension control on a high-speed machine now will allow us to go in and wind some of these non-uniform webs, analyze the rolls as we wind them, and verify if the models are working correctly or not.”
CONVERTER INFO:
Oklahoma State Web Handling Research Center
930 N. Willis St.
Stillwater, OK 74075
405/744-5140; engext.okstate.edu
SUPPLIER INFO:
Rockwell Automation—PFFC-ASAP 306. rockwellautomation.com