New Clear Barrier Film Resin Technology Replaces Coated Films
- Published: September 30, 2004, By Chris Voght, Torayfan Div., Toray Plastics (America) Inc.
Creating packaging that allows consumers to see clearly the food they are purchasing — and also promises the food is fresh — presents converters and end-users with a unique manufacturing challenge.
Light-, oxygen-, and moisture-barrier properties, puncture and oil resistance, sealant performance, and machinability are important packaging requirements that must be evaluated. Aesthetic appeal and, ultimately, cost-effectiveness also are prime considerations.
Traditionally, PVdC (polyvinylidene chloride)-coated oriented polypropylene (OPP) film has been specified for demanding applications because of its unique combination of mechanical, barrier, and aesthetic properties. Common examples of foods packaged in PVdC-coated OPP films include tortilla chips, extruded corn snacks, pork skins, crackers, cookies, oil-based confections, and pet foods. PVdC-coated film, however, is expensive due to its two-step manufacturing process. And in applications requiring either moisture- or oxygen-barrier properties, but not both, its use can lead to over-engineering.
Today, new clear barrier, non-PVdC-coated polypropylene (BOPP) film technology made with proprietary resins that enable a one-step manufacturing process allows converters to cost-effectively achieve the exact combination of performance and aesthetic properties required without over-engineering or the need for investment in new or specially modified converting equipment.
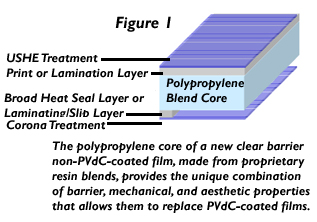
Overall, a non-PVdC-coated 70-ga or 80-ga film can offer better moisture and O2 barrier properties, greater strength and puncture resistance, improved oil resistance, and superior sealing characteristics compared with conventional OPP films (See Figure 1).
Typically, these types of films are non-yellowing and microwavable, making them even more attractive to the end-user and consumer. In addition, non-PVdC-coated films are environmentally friendly and completely recyclable. Converters can grind manufacturing scrap into resin pellets and consumer waste can be incinerated.
Specifically, the new 70-ga and 80-ga non-PVdC films offer moisture vapor transmission rate (MVTR) values far lower than conventional OPP films (80 ga = 0.19 cc/100in2/day, 70 ga = 0.22, conventional OPP = 0.44), which is significantly lower than moderate barrier PVdC-coated films (approximately 0.25), and nearly as low as high barrier PVdC-coated films (approximately 0.15). Laminating two of these non-PVdC films with polyethylene (PE) or adhesive can achieve even lower MVTR values (<0.10 cc/100in2/day).
While single sheets of 70-ga or 80-ga film do not offer the oxygen barrier properties of PVdC-coated films (both = 78 cc/100in2/day), an ethylene vinyl alcohol (EVOH) lamination will provide properties (O2TR = 0.04) significantly better than even those of high barrier PVdC-coated films (0.3). Even though an EVOH lamination is more costly than a typical adhesive or poly-mounted lamination, the cost savings associated with replacement of the PVdC-coated film can make the total lamination a cost-effective change.
In addition to their barrier properties, the new non-coated films also provide superior mechanical properties compared with conventional OPP films. The tensile strength of a 70-ga film, for example, is significantly higher in both the transverse direction (TD) (50,000 lb/in2) and the machine direction (MD) (23,000 lb/in2) than that of conventional 70-ga OPP.
Elongation of a 70-ga film is also significantly greater (200% vs. 180% MD, 65% vs. 60% TD) than conventional OPP. Its Young’s modulus is approximately 15% higher in the TD (630,000 vs. 548,000 lb/in2) and more than 25% higher in the MD (400,000 vs. 316,000 lb/in2). This increase in mechanical properties translates to a stiffer film with improved puncture resistance and oil resistance.
In terms of stiffness, a 70-ga film can be equivalent to a 77-ga conventional OPP, while an 80-ga film can be equivalent to 88-ga conventional OPP. These superior mechanical properties present the converter with an opportunity for significant cost savings through down gauging.
The puncture resistance of the unlaminated film is also more than 10% higher (2,632 vs. 2,381gf) than conventional OPP.
Regarding oil resistance, Toray Plastics (America) Inc.’s research shows that when film samples were immersed in 100% corn oil at 130° F for 24 hr, for example, conventional OPP film absorbed more than 2.5% of its weight while a 70-ga film absorbed less than 1.5%. This caused the conventional OPP film to swell by nearly 1.5% in both the MD and TD while a new 70-ga film swelled by less than 0.5%.
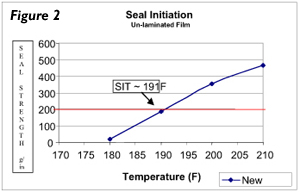
In order to protect its contents, a package must be able to be hermetically sealed. A new heat-sealable non-PVdC film, if supported by a proprietary sealant layer, will maintain seal strength comparable to that of a broad range commercial sealant. In fact, tests demonstrate that it maintains its hot tack characteristics significantly better than the commercial sealant at temperatures up to 250° F, and measurement of its shear viscosity at that temperature shows that it maintains much better "hermeticity."
In spite of its ability to perform well at elevated temperatures, non-PVdC films also demonstrate a seal initiation temperature (SIT) of only 191° F vs. 200° F for the broad range commercial sealants used on today’s BOPPs. (See Figure 2.)
The lower temperature is especially important in vertical form/fill/seal (VFFS) and horizontal form/fill/seal (HFFS) applications, which typically run at higher speeds.
Non-sealable surfaces can be specially formulated to promote optimum adhesion not only of printing inks, but of extrusion coatings, adhesives, and cohesives (natural and synthetic). This allows the flexibility to use either the heat-sealable surface as the inside of the package and the printable surface as the outside in mono web applications, or to use a non-sealable version as the inside, sealing the package with a commercial cohesive, or as the out side as the print web.
Either alternative now makes it possible to take advantage of the unique combination of barrier, mechanical, and aesthetic properties offered by these new non-coated films.
The flexibility of new non-coated films in allowing converters and end-users to choose exactly the properties they need for the application at hand, without incurring additional costs by over-engineering the package, offers a host of advantages to companies seeking to maintain healthy profit margins in today’s competitive environment.
Chris Voght is a product manager in the Torayfan Div. of Toray Plastics (America) Inc. He can be reached at chris.voght@toraytpa.com or 401/294-4511, ext. 3226. Toray Plastics (America) Inc.’s new clear barrier, non-PVdC-coated film technology includes CB-S and CB-P BOPP films.