Giving JDF Content a Great Send-off
- Published: March 31, 2005, By Mark A. Lonsdale, SAVVIS Communications
Web Exclusive
The packaging and converting industry is just beginning to pay attention to JDF (Job Definition Format) and the potential benefits of automating and streamlining the converting production workflow. Particularly in packaging, where there are many partnersfrom the brand owners and designers (both graphic and structure) to prepress, converting, and fulfillment, through the retailer’s warehouses and shelves—all players can benefit from implementing JDF.
JDF is a data exchange format that automates workflows by passing instructions and job parameters between devices. In simple terms, it promises to carry a job from origination to completion, with detailed descriptions of the creative, prepress, production, and delivery processes. This includes anything from quantities and bar codes to "ship to" addresses. JDF-enabled workflows will even refer directly to MIS systems and pull data that will help define a job, without requiring operators to type redundant information. This functionality will save companies time and money, while increasing accuracy.
But JDF is still in its infancy. Industry players are striving to better understand what JDF will do for them and how it can be implemented. Until recently, much of the attention toward JDF had been placed on commercial printing rather than converting. However, newer standards have been developed with the specific needs of the packaging industry in mind. Still, many are forgetting a very critical component—file transfer.
With workflows and collaboration between many different business enterprises, security becomes a major issue. In addition to the project content, information generated upstream in Management Information Systems (MIS), such as planning, scheduling, process results, job status, and job tracking, will be exchanged. This will increase the need for higher-performance data transmission. More importantly, without the correct JDF systems in place for file transfer, the system could become overloaded and information lost.
JDF and JMF
There are two important components of the JDF standard. JDF is an XML-based format. It coordinates all aspects of the print workflow, from prepress to press through post-press. It also lets production workflow systems exchange information with MIS business systems. JDF simplifies information exchanges between different production applications and systems. It will enable the entire supply chain to implement and work with individual workflow solutions from different vendors, independent of system architecture.
JDF works jointly with the Job Messaging Format (JMF). JMF allows production workflow hardware and software systems in a JDF workflow to communicate with administrative components and system controllers. It helps to swap dynamic data in real time, such as information from various production devices, status messages, and queue management.
Working without JDF file transfer
For those companies that have very basic workflows—highly unlikely for packaging—exchanging data may work without a sophisticated data transfer system. For example, companies working with only one partner can set their own file transfer rules and naming conventions and assure employees abide by them. However, with many partners, it’s impossible to abide by one player’s set of rules. The number and size of the data and files is enormous and could come from many different places. Content has to be preflighted while the validation and various naming conventions have to be understood. Every company has its own workflow rules and systems, and there are likely to be collisions. JDF allows standardization of those rules across multiple business partners.
Although two companies may have JDF-enabled applications, without a JDF-enabled file transfer method, there still may be problems interpreting commands from one site to another.
JDF includes pointers that tell the system the status of a job and where the content currently resides. As content is moved or work is completed, that information has to be updated. If the receiving system is not set up to work with JDF, the sender won’t obtain a confirmation of file delivery. Without a JDF-enabled file transfer system, you’re putting the burden on the recipient to know what to do with the content.
Don’t rely on the workflow or software vendor to create JDF-compliant software that supports the necessary file transfer mechanics. They are busy enough implementing JDF compliance within their own applications. You need to find someone who has file transfer and workflow automation expertise.
Remember, although your supply chain may have implemented JDF within their internal workflows, if they do not have JDF file transfer capabilities, the JDF workflow will be incapacitated as it extends beyond your four walls. Utilizing a JDF-compliant digital content management and distribution vendor will allow you to automatically receive, interpret, and route in accordance with your workflow, eliminating the need to manually interact as work moves between your clients, partners, remote staff, and your organization.
How to proceed
No matter how you proceed, realize that you may have to consider how to automate your JDF workflow while not being restricted to only those recipients that have implemented JDF. Many companies will have to justify the ROI of a JDF-enabled system before purchasing and installation. Because file transfer methods and needs vary across workflows and because standards have not yet been set, it is likely that the industry will ultimately determine the best practices.
For those companies that would like to build their own systems, there are typically three steps:
- Select a file transfer application that can handle JDF content.
- Purchase a server to host your file transfer application.
- Select a bandwidth provider for a dedicated connection, or use your own Internet access.
This is certainly viable, and there are many consultants knowledgeable in printing and prepress that can assist in the process.
There is another way, which is to utilize an existing JDF-enabled content management and distribution service provider—typically easier and requiring little capital investment.
Industry analyst Gistics estimates the services model is growing and will soon overtake standalone hardware and software sales. Services offered on a subscription basis allow rapid implementation. You don’t need to spend design time, wait for equipment purchases and approvals, or coordinate installations. Service providers have a model that can be deployed quickly. They eliminate costs in infrastructure and manual processes that can, in some cases, provide customers a 100% payback in as little as one year. Because service providers are set up to scale, they provide you with additional content and workflow services as your organization grows. These services allow customers to organize, store, access, and distribute content across their organization and supply chain through a single system.
Many file transfer systems will provide an Application Program Interface (API), basically a key into the file transfer system. This allows the workflow to talk with the file transfer system and allows content to be moved, thus facilitating the workflow. Some workflow companies may develop their own APIs, while others may rely on the standard API from the file transfer system. Other companies may find the need to build APIs to connect legacy systems into the workflow. These APIs provide easy integration with existing systems and allow industry best-of-breed workflow applications to integrate with this global platform.
What to Expect with JDF File Transfer
Using JDF, users can automate the distribution of JDF content through their workflows and supply chain network.
Content typically is packaged for delivery and JDF instructions are interpreted automatically by the file transfer system. JDF utilizes XML to exchange job ticket information between different applications and systems. Then, the content is sent to the specified destination—for example, a prepress shop. As the content moves to its final destination—perhaps the converter—instructions for JDF-enabled devices also are provided. Utilizing the JDF instructions, content is retrieved and routed in accordance with the workflow. Of course, in an inter-enterprise workflow, this creates the necessity for secure interaction between different plants, different enterprises, and different platforms.
With a good, JDF-enabled system, content can be automatically sent to the specified destinations as defined by the JDF job ticket. If the customer’s destination device is JDF enabled, the content will be placed in an accessible location and notification will automatically confirm that the content has arrived. Content can be retrieved and routed to a specific workstation in accordance with the specified JDF instructions. If the destination is not JDF enabled, the content may be retrieved in a manner consistent with the customer’s current destination workflow.
With complete end-to-end production workflow solutions, an extended "JDF community" of cooperating companies can share a single platform to collaborate more effectively and accelerate the workflow—ultimately resulting in faster time to market plus quicker and more profitable revenue streams.
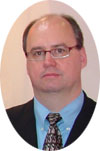
Mark A. Lonsdale, M.I.E.E., is VP of digital content solutions at SAVVIS Communications where he leads product solutions support, solution implementation management, and project office functions for the Digital Content Services Group. Lonsdale joined SAVVIS as part of its acquisition of WAM!NET, a provider of digital content management, a distribution solution for the packaging, print, and publishing industries. Before joining SAVVIS, Lonsdale held positions in management, consultation, systems integration design, and Asia region operations at Lockheed Martin Management and Data Systems. He holds a B. Eng. (hons.) in Electronic Engineering from Liverpool Univ., UK, and is a member of the British Inst. of Electrical Engineers.