Razor's Edgy Package
- Published: August 01, 2009, By By Edward Boyle, Contributing Editor
Colbert Packaging Corp., a manufacturer of folding cartons, rigid paper boxes, and paperboard specialty products, is celebrating its 50th anniversary this year. Bill Snyder, VP of operations, says the company's longevity — and continued success — is due to its ongoing investment in research and development, as well as new equipment and technologies.
The company's folding carton, flexographic packaging, and pressure-sensitive label operations are based in Lake Forest, IL; an additional folding carton facility is located in Elkhart, IN, along with rigid box production. Manufacturing facilities are a combined 340,000 sq ft.
Equipment at its Lake Forest folding carton plant, which primarily produces pharmaceutical packaging, includes a new seven-color, 28×40-in. Mitsubishi Diamond 3000 tandem perfector, which prints six colors on the front side and one color on the back. Because 21% of its jobs have two-sided printing, Snyder says the new press eliminates the need for a second pass on many cartons.
“A lot of pharmaceutical companies right now are looking to put more print and instructions on the back side of the carton as well as the front because they need more space,” he explains. “The unique thing about this press is that it will print the back side and the front side in one pass, even with the same side gripper. The idea is to get good registration front and back.”
Along with the new press, Colbert also installed the Simulchange automatic plate-changing system that will change all seven plates in one minute. Because of the tandem feature of the press, it runs at a maximum speed of 13,000 sheets/hr. The new press complements a recently upgraded Mitsubishi with updated inking and computer systems, “so really they're interchangeable,” explains Snyder.
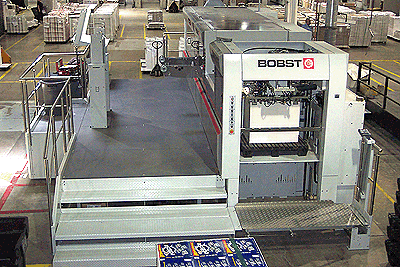
Also new is an Expertcut Autoplaten die-cutter from Bobst Group. The machine is said to provide state-of-the-art register systems, intelligent feeders, and quick-change tooling, complemented by an ergonomic design.
The facility also houses ten Bobst folder/gluers and serves as the Beta site for an Advanced Vision Technology Orion inspection system. The separate Lake Forest flexo facility has four 7-in. and 13-in. Mark Andy presses that print both labels and cartons in up to eight colors.
Page 2 of 2
The Elkhart facility houses a 28×40-in. six-color manroland offset press and a 28×40-in. six-color Heidelberg that was moved from the Lake Forest facility so each location would have two-press capacity.
A Safer Package
Among Colbert's innovative products is BlisterGuard, an eco-friendly alternative to plastic clamshells. BlisterGuard, introduced five years ago, actually was the first product patented by the company because of its many unique features, explains Snyder. Developed by Colbert's VP of business development, Glenn Grosskopf, BlisterGuard is primarily a paper-based product with a large printable area that gives manufacturers better shelf presentation for their products while increasing brand awareness.
BlisterGuard is recyclable in programs that accept mixed material packaging and meets retailers' demands for more sustainable packaging, reducing the use of petroleum-based plastics by as much as 70%. And by design, the lack of sharp edges makes it safer to open than traditional plastic clamshells.
BlisterGuard is manufactured with International Paper's Everest Safe-Pak solid bleached sulfate heat-sealable paperboard laminated with multilayer Valéron Strength Film. A companion thermoformed blister replaces the clamshell.
P&G Is a Believer
Gillette, a div. of Procter & Gamble perhaps best known for its large line of shaving products, was among the first and now the largest users of BlisterGuard. (More than 100 million packages have been sold by Colbert and its licensees since its introduction.)
Since 2000, Gillette's razors have been packaged in radio frequency (RF)-sealed clamshells as a solution to a high theft rate. The clamshell offers great security against theft since it is sealed around the edges during the packaging process. However, this process also makes it very difficult and dangerous for purchasers to open, due to the sharp edges that are formed when opening the package with a knife or scissors. Moreover, the clamshell's exterior is made entirely of plastic.
As Gillette began focusing its efforts on more sustainable packaging, the company was faced with a challenge to consider clamshell alternatives for its products in the context of their current systems, process, equipment, and continued need to guard against theft.
Gillette set out to find a solution that would meet sustainability needs without requiring new packaging equipment or additional labor costs. Gillette, under the project management of senior engineer Michael Marcinkowski, evaluated several options and ultimately selected BlisterGuard.
“We really pushed the envelope on the design,” says Marcinkowski. “We worked closely with Colbert's R&D team to develop unique foil-laminated cards and a feature that allows some of the packages to breathe. Our R&D team was involved in package design and trials. They had a lot of great ideas, and we relied on Colbert's expertise to ultimately deliver on our needs.
“It was a great, collaborative process. In fact, whenever we had an idea or request, Colbert found a way to make it happen.”
Today, BlisterGuard packaging is used for the entire Gillette razor product line sold at all club stores in the US and Canada. (Colbert itself sells cartons in six countries.) This includes such well-known Gillette brands as Fusion, Mach3, Sensor, and Venus.
While all club packs are now sold in BlisterGuard packaging, the packaging design varies by brand and model to meet the individual needs of each product and the various components. For example, some packages contain a razor plus blades, some also contain a battery, and others contain blades only.
“BlisterGuard gave us what we needed to retain pilfer-resistance while also meeting our goals for sustainability,” said Marcinkowski. “We were able to make a positive change to our razor packaging with our existing machinery without increasing the time it takes to deliver our products. The end result is a win for all involved — retailers, Gillette, the environment and our consumers.”
Contributing Editor Edward Boyle, based in Reading, PA, has covered the converting industry for more than 24 years. Contact him at EJB Communications; 610-670-4680; ejbcomm@aol.com.
Converter Info
-
Colbert Packaging Corp. | 28355 N. Bradley Rd., Lake Forest, IL 60045 | 847-367-5990 | www.colbertpkg.com
R&D Leads to Unique Products
Colbert Packaging's investment in research and development has led to the creation of a number of specialty products. Its innovative packaging includes:
- EnviroGuard | pilfer-resistant packaging solution made entirely from paperboard
- Zip-Sert | a carton and drug packaging insert in one easy-to-use unit
- PharmaDial | a patented unit dose package to promote patient compliance
- PharmaGuard | a tear-resistant solution for various compliance packages
- BlisterGuard | an environmentally friendly alternative to plastic clamshells, among others
Supplier Info
-
Mitsubishi Lithographic Presses | www.mlpusa.com
Circle 324 or visit www.freeproductinfo.net/pff -
Bobst Group | www.bobstgroup.com
Circle 325 or visit www.freeproductinfo.net/pff -
Advanced Vision Technology | www.avt-inc.com
Circle 326 or visit www.freeproductinfo.net/pff -
Mark Andy | www.markandy.com
Circle 327 or visit www.freeproductinfo.net/pff -
manroland | www.manroland.com
Circle 328 or visit www.freeproductinfo.net/pff -
Heidelberg | www.us.heidelberg.com
Circle 329 or visit www.freeproductinfo.net/pff -
International Paper | www.internationalpaper.com
Circle 330 or visit www.freeproductinfo.net/pff -
Valéron | www.valeron.com
Circle 331 or visit www.freeproductinfo.net/pff