Pilot Coating: Coater Clone
- Published: April 01, 2010, By By Edward Boyle, Contributing Editor
Brady Corp., an ISO-certified international manufacturer of high-performance labels and signs, safety devices, printing systems, and software, has 7,000 employees, 100 facilities in 35 countries, and annual sales of $1.2 billion. But sales manager Eric Maercklein says the company's single pilot coating facility, located in Milwaukee, WI, helps improve quality throughout the entire organization.
“The materials that we make here are shipped globally to our other business units. They typically sell labels made out of our material,” he says. “They'll do the printing and the die-cutting of the labels locally, but the rollstock they use in the process is manufactured here in Milwaukee.”
The 120,000-sq-ft facility houses three full-size production coaters ranging from 60-65 in., depending on the use and the coating method. These production coaters are manufactured by Black Clawson Converting Machinery (Davis-Standard) and Faustel. Ovens are supplied by Black Clawson, Advanced Systems Inc. (ASI), and Pagendarm, a member of the Polytype Converting Group.
While the pilot coater is just 30 in. wide, “it's built essentially with the same oven configurations as our production equipment, so we can easily scale up from the narrow web to the wider width,” Maercklein says.
“When we were selecting manufacturers, we came up with our own design, so we didn't buy a ‘pre-designed’ machine. We went out for bids and asked the different coating companies to build a machine to our specifications. That's how we ended up selecting a Korean manufacturer, Sung An Machinery [SAM].”
“The purpose of this machine is truly a pilot line,” says technical manager Jerry Majusiak. “Because this is a small version of our production coaters with an identical configuration, an identical oven and tension controls, we're able to translate directly both our web tensions and our oven conditions to our production coaters.
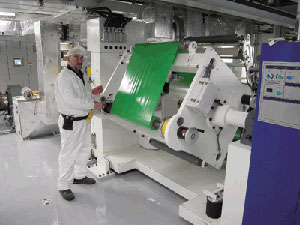
“We're also able to produce a sample that's as good as we would get off our production equipment, which wasn't always possible in the past,” he adds. “Now, with this upgraded technology, we're able to get comparable quality off both!”
Brady primarily uses the pilot line, which has a 24-ft oven, to test raw materials. Coating methods include slot die, forward and reverse gravure, Mayer rod, and knife-over-roll.
During product testing, says Maercklein, “sometimes we make samples as short as ten feet. In the initial screening process, we might take 15 different screening solutions down to the pilot coater and run ten feet of each, then take them all back to the lab and analyze them.”
The company does use the pilot line occasionally to convert short runs that can't be produced economically on its wider equipment.
Explains Majusiak, “If you're doing product development, the first six months or so, the volumes can be pretty small. We're able to actually do production on this machine for at least the early stages until the volumes get big enough to move to the larger coaters.”
Pilot Coater Available To Customers
Brady leases time on its pilot coating facility to other converters to facilitate scale up to the larger production machines. In fact, Majusiak notes that half of the facility's time is dedicated to contract converting. Customers, however, “aren't allowed to run the equipment.” All runs are converted by Brady's own operators. “But we do welcome our customers into our facility to observe what we do,” he says.
Maercklein says the new pilot line, which went into operation last year replacing an older, far more “antiquated” version, is housed in a specially designed clean room environment. “We're using Class 1000 air supplies to both the room and the oven to more closely represent the manufacturing environments on our production equipment,” he says.
The new line also allows the company to run both high- and low-viscosity coatings and convert diverse materials and multilayer laminates. Capabilities include 0.2-20 mil film, 0.4-10 mil foil, 25-200# paper, paperboard, nonwovens, and tissue.
“Brady's business is engineered for very specific industrial applications, so we get into a lot of very different product constructions,” explains Maercklein. “Consequently, our machine is designed to be very flexible.”
Contributing editor Edward Boyle, based in Reading, PA, has covered the converting industry for more than 25 years. Contact him at EJB Communications; 610-670-4680; This email address is being protected from spambots. You need JavaScript enabled to view it.. The turret unwind on the pilot coater also is manufactured by SAM.
Supplier Info
-
Sung An Machinery (SAM) | www.sungan.net
Circle 310 or visit
www.freeproductinfo.net/pff -
Davis-Standard LLC/Black Clawson Converting Machinery | www.bc-egan.com
Circle 311 or visit |
www.freeproductinfo.net/pff -
Faustel Inc. | www.faustel.com
Circle 312 or visit www.freeproductinfo.net/pff -
Advance Systems Inc. | www.advancesystems.com
Circle 313 or visit
www.freeproductinfo.net/pff -
Pagendarm | www.pagendarm.com
Circle 314 or visit
www.freeproductinfo.net/pff
Looking for Pilot Facilities?
Each November, PFFC publishes a comprehensive directory of Lab/Pilot/Technical Facilities ready to assist you in your R&D efforts. See p28 of our November 2009 issue or find it online at http://pffc-online.com/coat_lam/main/lab-pilot-technical-facilities-directory-1109.
Converter Info
-
Brady Coated Products |
2230 W. Forest Ave., Milwaukee, WI 53209 |
800-662-1191 |
www.coatedproducts.com