Blown Film | Which Applications Are Most Suited for 7/9/11 Layers? Part 3
- Published: August 03, 2017, By Tom Bezigian
What are the benefits of 7/9/11-layer lines over 3- or 5-layer lines?
Given what we know today, five-layer structures are limited as to their performance and cost-saving ability. From a simple cost standpoint, for example, whereas the structure in Figure 1A (as shown in Part 1) is an LLDPE/Tie/EVOH/Tie/LLDPE structure, a seven-layer structure can utilize a lower-cost LLDPE in the second layer and an expensive, high-performance metallocene LLDPE as the skin layer, which has superior hot tack and heat seal properties. This structure, mLLDPE/LLDPE/Tie/EVOH/Tie/LLDPE/mLLDPE shown in Figure 3A below, optimizes performance and cost and is used for milk packaging.
Alternatively, if improved barrier properties and toughness are desired, an LLDPE/Tie/Nylon/EVOH/Nylon/Tie/mLLDPE structure can be made with a seven-layer die, shown in Figure 3B. This structure is used as a lidding film with excellent barrier properties and gloss. If ethylene vinyl acetate (EVA) is substituted for the mLLDPE layer in this previous structure, the film can be used as a thermoformable cheese tray, shown in Figure 3C. The point made here is that more layers offers the package designer more options.
Figure 3. Seven-layer structures for various applications and uses
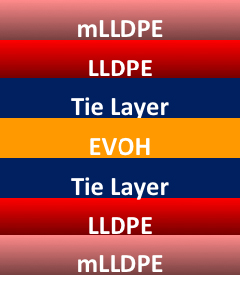
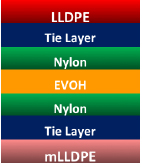
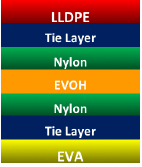
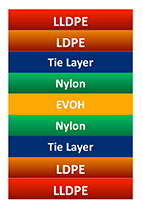
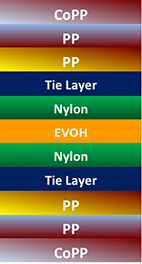
In the final analysis, the application determines the performance requirements, which in turn determine the function requirements. The ability to split an expensive sealant layer into two layers, one of which is less expensive, reduces the cost of the overall film and package. Assume a single line can produce 362 kg/hr x 22 hr/day up time x $0.0272/kg = $380,000/yr savings [7]. This is achieved by substituting lower cost resins in a nine-layer structure as compared to a seven-layer structure. Figure 4 shows a schematic of a seven-layer die.
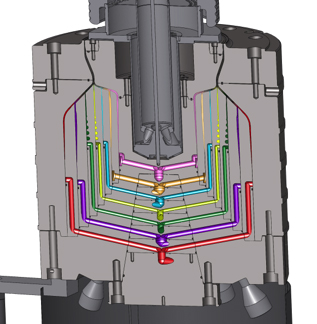
In some parts of the world, some resins are simply not available, so substitution becomes a necessity. Moving to nine layers gives further flexibility to the blown film manufacturer without sacrificing film properties. According to David Nunes, president of Alpine American in Boston, MA, "There are dozens, perhaps more than 100, seven-layer blown film lines in use today. They offer the converter excellent flexibility in terms of product structure, asymmetric layer ratios, and film properties."
It is estimated that there are less than 50 nine-layer lines in use in the world today, and 11-layer blown film lines are basically brand new entries into the marketplace, so little practical information exists to report on today. It is envisioned that 11-layer structures will provide the ultimate in flexibility in terms of structures that can be made, with advances, asymmetric barrier structures being the target market. One technical source envisions a structure as shown in Figure 3 for use as a retortable pouch with superior barrier properties to be made on 11-layer blown film lines [4]. One configuration for an 11-layer blown film line is shown in Figure 5. It is readily discernible that manufacturing space becomes more and more crowded as the number of extruders is increased, creating a challenging operational and maintenance environment.
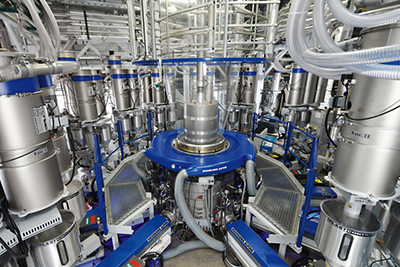
While none of the major manufacturers report any sales, or even the development of, a 13-layer die, a small development company in South Carolina has been working on a 77-layer die, which uses nano-technology via a series of layer-splitting rings to produce films of superior strength.
According to Henry Schirmer, CEO at BBS Corp., Spartanburg, SC, "It has been shown that it is feasible to produce blown film configurations with up to 77 layers using our new Layer Sequence Repeater (LSR). This technology allows the polymer molecules to align without stress in a nanolayer film structure. This provides many advantages, such as increased blow-up ratio in blown film, higher orientation ratios on biax film lines, higher strength films, thinner films, and also improved clarity." Schirmer, who is author or co-author of nearly 100 patents, further indicates that "Nanolayer coextrusions of nylon 6 and EVOH can be made with higher-than-standard blow-up ratios on a blown film line, which yield high-strength, crystal-clear film, overcoming a present limitation of standard coextrusions of those two materials" [8, 9, 10].
Nanolayer films are truly novel and exciting. Because the surface contact area within a nanolayer melt is so great and the mass is so small, instantaneous air quenching reduces crystallinity in a similar manner to water quenched films, and high clarity is the result. Even DSC polymer signatures have been altered with nylon/EVOH combinations consistent with forming a co-polymer between these two active polymers, which is nothing short of miraculous.
Are there any alternatives to advanced multilayer blown film lines?
While there is a lot of technical merit to 7/9/11-layer blown film lines, the market will have to sort out the utility of this new technology. Until then, there is a very large installed base of three- and five-layer blown film lines, dozens or more oriented film machines, vacuum metallizers, adhesive laminators, and extrusion laminators that, when taken together, can produce any combination of bulk layers, barrier layers, adhesives, and sealants to satisfy any need without any further capital expenditure. And while not as green or environmentally friendly perhaps as a single-step blown film operation, cost is quite often a driving factor in any product design or market category.
Conclusion
Technology exists today to produce blown films with up to 77 layers. The most common number of coextruded layers in use today is three layers, with a trend to five- and nine-layer films. As machinery advances are made, new product structures are created to fulfill various market needs. A balance will be struck between cost of new capital equipment required to makes 7/9/11-layer films and the benefit derived from doing so. The competition is not necessarily another machine supplier, or from a lower-cost producer, but from another technology that can laminate unlike films to produce similar structures, namely adhesive lamination and extrusion lamination. These technologies have coexisted for many years and are likely to do so for the foreseeable future.
Bibliography
1. US Patent 2820249
2. US Patent 3308508
3. "Blown Film Training", The Dow Chemical Co.
4. "Rethinking Technology Innovations for High Barrier Applications", Kurt Freye, Reifenhäuser Kiefel Extrusion
5. "Properties, Processing and Handling of EVALTM EVOH Resins", Medlock, G., AIMCAL Fall Technical Conference, October 2014
6. "The Influence of Sealant Modulus on the Bending Stiffness of Multilayer Films", Morris & VanSant, DuPont Packaging White Paper, 2009
7. "Coextrusion - The Pros and Cons of More Layers", Bill Hellmuth, Gloucester Engineering
8. "Nano-layer - Micro-layer Structural Advances in Shrink Films, Schirmer et al, 2013 SPE International Polyolefins Conference, Houston, Texas, USA
9. http://plasticsengineeringblog.com/2013/01/04/new-technologies-in-stretching-and-touching/
10. US Patent number 8870561, issued 28 OCT 2014
11. From: Medlock, G. (Kuraray), “Properties, Processing and Handling of EVALTM EVOH Resins”, AIMCAL, Oct 2014
Tom Bezigian holds a B.S. in Plastics Engineering from the University of Massachusetts–Lowell. He has been affiliated with the converting industry for more than 30 years and writes a blog, Tom's Poly Ploys, for PFFC. It focuses on the field of polymers, laminations, and coatings with emphasis on R&D, quality assurance, manufacturing, marketing, operations, finance, and expert witness experience in the blown film, cast film, orienting, extrusion coating, and converting industries. He is owner of PLC Technologies consultancy with over 30 years experience. Contact him at This email address is being protected from spambots. You need JavaScript enabled to view it..