Film Converting: Luminit Films Shape Light
- Published: October 01, 2008, By By Edward Boyle, Contributing Editor
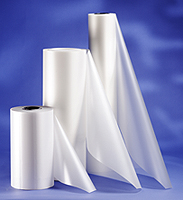
Stanley Kao, business development manager for Luminit LLC, says the proprietary process used to create its Light Shaping Diffusers (LSD) “is a film-to-film, roll-to-roll process in-line, using equipment pretty much like that used in the printing industry.” But that's where the similarities end.
In fact, comparing the process Luminit uses to develop and convert its specialty LSD structures is like comparing the space shuttle and a Piper Cub. Other than the ability to fly, the two have little in common. “There is a proprietary process involved,” says Kao. “It's very, very different from regular printing or film lamination.”
The Torrance, CA-based company specializes in “custom and standard holographic diffuser solutions,” converting advanced opto-electronic technology into film-based products that integrate photonics, optics, holography, electronics, and software. The converted films are used in a variety of light-transfer applications, flat screen TVs, cell phone displays, computer monitors, and bio-medical instrumentation.
Kao explains as light emitting diodes are becoming brighter and more energy efficient, they are being used in more general applications, further broadening the company's customer base. In fact, says Kao, “We are in the process of developing the next generation LCD backlight and rear-projection TV.”
To create its LSDs, the company's proprietary toll casting process employs epoxy to pick up the surface structure that is shot using a laser. Those diffusers adhere to a variety of polyethylene and polycarbonate films up to 20 in. wide in thicknesses from 0.005-0.125 in.
The converting equipment uses high-precision rubber rollers from Abba Rubber Intl. that maintain critical grinding tolerances, feature clean compounds, and offer quick turnarounds. Luminit marketing manager Pete Zinsli says the rollers are critical to the process of embossing a sub-micron pattern of lenses — as many as 20 million/sq in. — onto the epoxy, which is then applied to the film using an ABBA nip roller.
“The nip roller presses against a ‘nickel shim’ that has a pattern on it that must be perfectly even,” explains Zinsli. “The rubber nip roller can't have any imperfections on it, or it will leave that imperfection as a pattern on what we're printing. The consisent high quality of the rolls is very important to the quality of our final product.”
Custom Angles
Walter Williams, manager of Web Operations, says the products produced by Luminit are so unique the company is not only the best at what they do, they're the only ones who do what they do. “In terms of surface holographic diffusers, we're the only one,” says Williams. “The rest of the stuff out there, they're bulk diffusers, they're particle diffusers, they're almost like a lamination process where the epoxy has particles in it. We provide our customers with superior quality of homogenized light, including custom angles. Our diffusers come in variety of shapes, sizes, angles, thickness, materials, and forms.”
The key, says Kao, is that Luminit's process directs the reflected light precisely where required by the customer, delivering maximum brilliance and clarity. “The backlighting has only a certain number of photons,” explains Kao, “so when it comes out, we can control everything to the viewer's eye to get the maximum gain you can get from a backlight, and at the same time homogenize the linear light in the back, and that's an advantage.
“These are micro-lenses, per se, but you can think of them as gradings that are produced using lasers, so that's why we call them holographic diffusers,” explains Kao. “It primarily uses a laser to record, and it takes a long time. It is a very, very controlled process.”
Luminit was established as a spin-off of Physical Office Corp. (POC), Torrance, CA, in 2006 after management realized the market potential of diffuser film in commercial applications, where it would be “more lucrative as a stand-alone company,” explains Walters. Those systems now are utilized in military, homeland security, avionics, medical, communication, and biotechnology applications.
Luminit operates in a 25,000-sq-ft facility housing engineering and holography labs, as well as the manufacturing floor space to support the development of products for customer-integrated lighting systems and applications. Most of its products are custom generated for each individual customer and project, although the company does maintain some common substrates and “angles” for quick delivery.
“It's a very special product,” says Williams, “and we're the only ones in the world that are doing it.”
Contributing editor Edward Boyle, based in Reading, PA, has covered the converting industry for more than 24 years. Contact him at EJB Communications; 610-670-4680; ejbcomm@aol.com.
Converter Info
- Luminit LLC | 20600 Gramercy Pl., Torrance, CA 90501 | 310-320-1066 | www.luminitco.com
Supplier Info
- Abba Rubber Intl. Inc. | www.abbarubber.com
PFFC-ASAP 345