Web Tension 101
- Published: November 30, 2004, By Jeff Damour, Converter Accessory Corp.
For this basic tutorial in the mechanics of web tension control, tension is defined as the force applied to a continuous web of material in the machine direction.
Typically, tension is measured in PLI (pounds per linear inch) in the US. If you know PLI and you want to know total tension applied to the web, multiply PLI times the width of the material in inches. If you know total pounds of tension applied to the web and you want to know PLI, divide the total pounds of tension across the web by the width of the web in inches.
- PLI = total pounds of tension / web width in inches
- Total pounds of tension = PLI x web width in inches>
The tension applied to a web can be described as the web’s tautness as it would be if you hung a weight off the edge of the web. The tension on the web would be equal to the weight in pounds. PLI would be equal to the weight in pounds divided by the web width in inches.
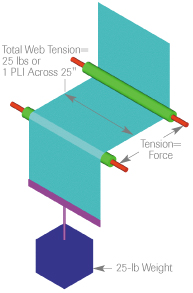
Why Is Tension Important?
It is impossible to control a web without proper tension being applied to it. The web must be "in traction" with all machine idler rolls and driven rolls to ensure proper web handling and control.
The web handling principle states a web will seek to align itself perpendicular to an idler or driven roll. This web handling principle is applied to route webs through processes with parallel idler rolls and driven rolls. It is applied when web guides are used to steer webs. It also is applied in many wrinkle removal devices. However, the web handling principal does not apply to webs that are not in traction with idler or driven rolls. In other words, if the web slips over the face of an idler or driven roll, it can wander from side to side, or if the web slips on web guiding idler rolls, it will not move where the web guide attempts to steer it. Tension must be applied to webs to keep them in traction with idler and driven rolls.
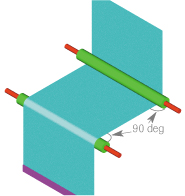
All webs stretch in the machine direction as tension is applied to them. It is important to apply proper tension to a web so it can be handled through the machine and processes without overstretching.
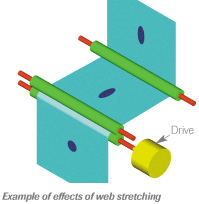
It is impossible to rewind or unwind rolls into a process without proper tension control at the rewind or unwind stations. Telescoping, "dished" rolls, wrinkles, and even web breaks will occur when tension is not controlled at the rewind or unwind stations.
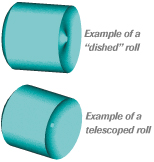
Many converting operations require proper registration to print or die-cut stations. Proper tension control is essential to controlling print-to-print or die-cut registration. Laminating operations require layers to be laminated with proper tension to avoid web curl.
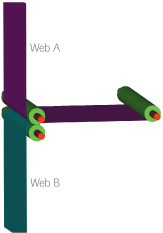
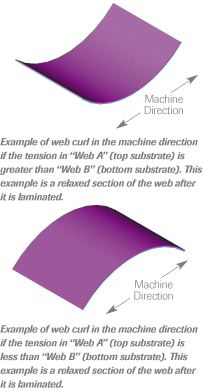
Slitting operations require proper slit position, which is a function of tension and web guiding.
When tension is too high, webs will stretch in the machine direction and compress in the cross machine direction. This narrowing of the web width can cause wrinkles to occur.
When tension is too low, webs will shrink in the machine direction and web width will widen in the cross machine direction. This widening of the web width can cause wrinkles to occur.
Where Is Tension Control Important?
Most converting applications include three types of tension zones—unwind, internal, and rewind. Each zone must be controlled independently. Multiple zones of each type are common in many converting applications; however, normally they are categorized as unwind, internal, or rewind.
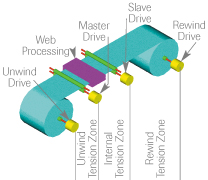
Ea Each tension zone is unique and must be controlled independently. Since independent tension controls are used in each zone, each zone may have its own tension level. This means, for example, tension in the unwind zone may be 1 PLI, then increase to 2 PLI in the internal zone, then decrease to 1.5 PLI in the rewind zone.
Torque required to provide a certain level of tension to a web is total tension measured across the web times roll radius. This means the torque driving the unwind shaft must decrease at a linear ratio, relative to roll diameter, as an unwind roll decreases in size, through a machine run, to keep tension constant. Conversely, the torque driving the rewind shaft must increase at a linear ratio, relative to roll diameter, as a rewind roll increases in size, through a machine run, to keep tension constant.
Tension in the unwind and rewind zones is very dynamic. Roll diameters are changing constantly, so torque and speed must be adjusted constantly relative to changing roll diameters. Tension and speed in the internal zones are much more stable since roll diameters in these zones do not change. However, some control is required to set and maintain desired levels. Web defects, splices, desired machine speeds, machine defects, and other variables will affect tension in the internal zones.
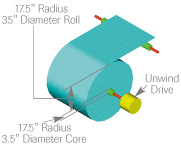
Remember, the equation torque = tension x radius is linear, so torque must be decreased (for unwinds) and increased (for rewinds) at a linear rate relative to roll radius. For example, if you start with a 17.5-in. roll radius (35-in. dia) and unwind down to a 1.75-in. core radius (3.5-in. dia); 17.5 divided by 1.75 is 10:1 ratio. That means, if you start at 100 in. lbs of torque at the beginning of the unwind roll for proper tension, the torque must be decreased linearly to 10 in. lbs of torque at the core to maintain constant tension.
The machine designer must determine required tension levels for each zone. Often, required tension levels can be determined only after actually running the web through the machine, since all webs and all processes are somewhat unique. TAPPI and many other industry organizations publish estimated proper tension levels for several types of webs and laminations. However, keep in mind these values are only guidelines and "best estimates" based on many years of combined industry experience. The actual best tension at which to run your specific web and process will, most likely, vary from the guideline. Another very general rule of thumb: Proper web tension usually is between 10% and 25% of the tensile strength of your web.
You can measure the tension at which you currently run your process. There are several methods for doing this.
- If you already have a load cell tension control, it normally has the ability to display actual tension in total pounds across the web. You also can purchase load cells with only a display (no control) if you would like to measure tension within any zone in your machine.
- If your machine has dancers, you can calculate the loading of the dancer on the web if you know the web geometry and the loading force on the dancer. To do this, you will need a drawing of the dancer and web path through the dancer. You also need to know the type of loading and the force applied. Another simpler method would be to place a scale of some sort to measure the force the dancer is loading on the web. Do this without the web threaded through the dancer. Remember, as long as the dancer remains somewhere within its travel (between its physical limits of completely full or completely empty), the tension on the web is equal to the loading in the dancer.
- Another crude but very effective way to measure tension in the unwind zone is the "fish scale method." This method works for the unwind zone only. It can be utilized only if there is a brake on the unwind station. Unwrap a small amount of material off the unwind roll. Set the unwind brake to the torque output normally set for a machine run. Wrap the leading edge of the web around a bar and hook the "fish scale" through the bar. Pull on the fish scale until the unwind starts to turn. Record the weight reading on the fish scale. This is the actual tension on the web, at this point. Divide the total weight by web width in inches to get PLI. Do not attempt this method of measuring tension if there is a drive motor on the unwind or for a rewind with a drive motor. Serious injury could result.
- Tension also can be calculated if you know the model of a brake or clutch and the output level to that brake or clutch at a given roll diameter. By knowing the torque output of the brake or clutch, we can plug the values into torque = roll radius x tension and extrapolate the actual tension the brake or clutch is delivering to the web.
Taper Tension
Everything discussed so far is based on constant tension applications. Do not confuse varying (or tapering) torque to achieve constant tension as taper tension. Taper tension never is desired for the unwind or internal zones. As a web is unwound and processed, constant web tension always is desired. Taper tension normally is desired in the rewind zone. As a roll is rewound, each layer builds up compressive forces that can cause inner layers, toward the core, to buckle. Wrinkling, starring, and crushed cores will occur if these compressive forces become too great. Taper tension relieves these compressive forces by actually decreasing web tension as the roll builds. The amount of taper tension normally is measured in percentage of set tension. For example, using the same 3.5-in. core dia and 35-in. outside roll dia, if taper tension was set to 50%, the tension will be decreased linearly from 3.5-in. core to 35-in. roll dia, so the tension will be half at the outside of the roll compared to the core.
Finally, there are large numbers of web tension control systems available ranging from very simple, inexpensive systems to very complex, expensive ones.
To learn (in generic terms) more about the basics of what systems are available, see PFFC’s December Web Exclusive for Part II of this technical report, "Mechanics of Tension Control."
Jeff Damour is the engineering manager at Converter Accessory Corp., Wind Gap, PA. He has been with CAC for more than 19 years, most of that time spent "in the field." Jeff has published several web handling technical articles and is a regular presenter at the Converting Equipment Mfrs. Assn. (CEMA) Coating & Laminating and Slitting seminars. Contact Jeff at 800/433-2413; damour@epix.net.
The views and opinions expressed in Technical Reports are those of the author(s), not those of the editors of PFFC. Please address comments to author(s).