Machine Engineering to Address the Needs of Emerging Flexible Films
- Published: October 28, 2020
By Jesse Rosenow, Sales Engineer/Technical Projects Leader, Totani America
As you walk down a grocery store aisle, it seems that everywhere you look – from pet food to snacks to cleaning products – flexible packaging is on display. In fact, the Flexible Packaging Association (FPA) found that flexible packaging is the second largest packaging segment in the U.S., as it makes up approximately 19 percent of the country’s $170 billion market.
While this presents great opportunities for packaging converters, it creates additional pressure to align with consumers’ ever-changing needs. As flexible packaging and the films used in production continue to evolve and adapt, converters can begin to optimize their operations through streamlined set up and reduced scrap, which is all being made possible through recent equipment innovations.
Growing Demand for Flexible Packaging
The continued rise of eCommerce purchasing, the public’s growing focus on sustainability, and brand sustainability goals have bolstered the use of flexible packaging across many markets. Throughout the first half of 2020, we’ve seen an increased demand for flexible pouches that help foods maintain freshness during the eCommerce shipping process. Enhanced freshness and extended shelf life are major selling points for flexible pouches, and the COVID-19 pandemic has further shown the need for this packaging.
As industry trends continue to evolve, converters must create packaging that aligns with the latest consumer and brand needs, all while continuing to provide a quality solution that is cost-effective. To help address new customer pain points, we’ve seen the emergence of new film structures, such as fully recyclable films. As new materials hit the market, converters should work with machine OEMs that can engineer equipment to efficiently and effectively convert films with minimum waste and reduced changeover times.
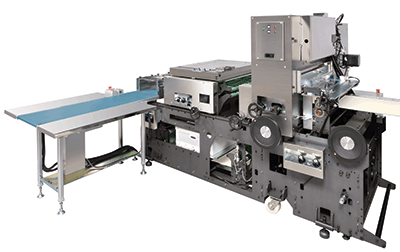
Engineering Machines to Suit Your Needs
Consider recently developed packaging films that have structures which are easier to recycle, commonly known as “mono” materials. While this is a major win for the flexible packaging industry in terms of sustainability, the introduction of these new film technologies on existing machinery can cause difficulties for converters. New materials often require different tension and registration control than existing conventional films, which can lead to longer downtime between runs and increased scrap. Because of this, OEMs are strategically engineering machines to tackle these challenges, as advances in tension control and registration are vital in improving print registration with emerging film technology.
For example, when starting a new run, the film material often stretches, distorting graphics and creating inconsistency in the packaging. This means each run wastes material until proper registration is reached on that specific machine start. New machine technology enables converters to better control tension at the start of the run and bring films into registration more quickly. This helps produce quality pouches in shorter amounts of time – reducing scrap material. This not only offers cost-savings for the facility but also limits the amount of waste produced and energy consumed.
As packaging equipment continues to innovate, converters can take advantage of equipment automation capabilities. At a basic level, automated features could provide operator support while setting up runs with digital aids, such as indicator lights for preset pouch sizes and quick releases that automatically adjust to different film materials. This both creates optimized set up for quicker turnaround and limits operator error for reductions in wasted time and product.
Fully automated equipment is already a reality. As technology advances and converters become more comfortable with new machine designs, operators can simply select a job within the equipment’s computer interface, and the machine automatically adjusts to the specifications for that run, vastly reducing the margin of error and scrap material.
Be Prepared with Innovative Machines
Converters can proactively prepare to meet their customers’ needs by working with OEMs that have the engineering capabilities to adapt to new film structures. By optimizing the printing process through automated technology, converters are able to create added operator efficiency for faster changeovers, cost savings, and reduced waste. Investing in innovative converting equipment can help facilities prepare to handle emerging films and continue to create quality pouches on-time and on-budget.
About the Author
Jesse Rosenow is a sales engineer/technical projects manager at Totani America. Rosenow has worked at Totani America for over eight years.