Color 101: Part I
- Published: January 01, 2007, By By David Argent Contributing Editor
Process Management
It has been my experience that color theory basics are communicated well by suppliers of color measurement devices. This month we will explore the practical application of this information.
We expect the color to be correct at the end of the value chain, that is, where the print comes off the press. It is the last chance to get it right. To avoid waste, the color should be correct without loss of press time or substrate.
The right color in print denotes brand recognition and quality, but achieving this color is never guaranteed without suitable controls being in place. Below is a simple workflow for review.
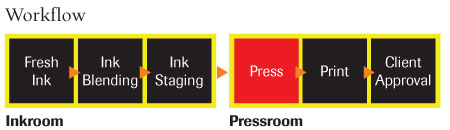
This macro flow chart shows the main steps involved going from ink to client approval. A well-integrated process ensures each step hands off to the next seamlessly.
Once the consumer product company has signed off on the color for its product, two basic areas have to be managed: raw materials and procedures. This will ensure repeat runs are on target and are produced efficiently, with low waste.
Color comes from ink pigments, and of all raw materials, this is by far the most critical in color management. Despite that, it is not well understood by our industry.
The color properties of individual pigments emanate from their specific chemical structure. These chemical structures are defined by specific Color Index names. For example, Lithol Rubine is “Red 57:1” and refers to a unique chemical structure. In practice, this means pigments used cannot be substituted without running the risk of the color not matching under all agreed viewing lights.
A typical ink dispenser will have approximately ten individual single pigment bases, and these define the available color space for color matching.
Not all pigments are suitable for use in all printing processes. This explains why it is not always possible to get exact color matches under all viewing conditions when comparing a brand color produced in offset, flexo, and gravure print. In such cases, the consumer product company decides on the best compromise. The converter’s responsibility is to maintain the agreed color from run to run.
Changes in pigments almost always will cause color problems. A simple concept: Change pigments, and the color space available is changed. To a lesser extent, a change in substrate will cause color shifts, particularly with paper and board substrates.
Having fixed the raw materials going into manufacturing, it is necessary to define and control the procedures along the value chain. Next month’s column will include a simple step plan for doing just that.
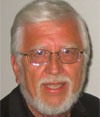
David Argent has 30+ years of experience in the converting industry. He specializes in process analysis and improvement with particular emphasis on ink and coating design and performance. Contact him at 636/391-8180; djvargent@sbcglobal.net.