How To Measure Total Asset Utilization
- Published: June 01, 2009, By By David Argent Contributing Editor
The concept of Total Asset Utilization (TAU) was introduced in an article by Jeffrey T. Luftig, Ph.D., titled “An Overview of a Productivity Metric for Profitability Enhancement and Focused Cost Reduction” (visit www.roi-ally.com/TAU.htm). TAU is a measure of how effectively an asset is used to make salable product.
This concept can be applied to converting equipment, such as presses, and in doing so, it can provide insight into manufacturing variables. TAU is the result of multiplying four ratios: two are related to the usage of time and the other two with the effective use of the equipment to make product.
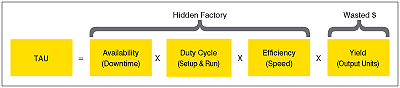
It is most revealing to plug in some numbers for the converting industry as in the following example.
- Availability
The ratio of the time the press is available to run to total time in the period being examined. It may be defined as Percent Run Time or Uptime. Conceptually, Availability will be equal to Total Time (the Base Period of Time selected for the analysis of TAU, e.g., month) minus Total Downtime, divided by Total Time. In calculating TAU, it is essential to track the contributing sub-components of Downtime, such as Scheduled, Unscheduled, and Idle Time; as well as the next level of contributing components, such as No Supply and No Demand time, in order to demonstrate improvement opportunities to process owners across the organization. Example: In a 730-hr month, the total downtime was 150 hr. Availability is 730-150/730 = 79%.
- Duty Cycle
The ratio between the time the press was actually running and the time it was running plus the time it took to set up. Example: The average run is 6 hr and took 2 hr to set up. Duty Cycle is 4/6 or 67% (a 24-hr average run with the same setup time = 92%).
- Efficiency
For this example, defined as the actual run speed versus the design maximum speed for the press. Example: The press is capable of running at 2,000 fpm but is limited by roll handling to 1,500 fpm. Efficiency is 1,500/2,000 = 75%.
- Yield
The simplest and most straightforward of the four components, representing the percentage of “good” or “acceptable” product made during a base period of time. Example: 250,000 lb produced of which 235,000 lb was salable. Yield is 235,000/250,000 = 94%.
- Total Asset Utilization
By multiplying these ratios together, we get a measure of how well we use time and the press to generate good product. TAU for this example is 79% × 67% × 75% × 94% = 38%.
The higher the value, the better we are utilizing the equipment. The lower the value, the greater is the opportunity to improve. Most TAU values, irrespective of the type of industry, are quite low, as shown in the converting example above. Some world-class firms will have a TAU value of 85% or higher. This implies that each component needs to be 96% or better. Certain world-class steel mills perform at this level. For this to happen, waste must be low, line speeds high, run lengths high, and all downtime components small.
In converting, all departments can contribute to greater TAU numbers. For example, consolidation of repeat customer orders will reduce the impact of setups. Effective scheduled preventative maintenance and faster press setups also will improve utilization, as will higher line speeds. However, all of this has to happen while minimizing waste.
It would an interesting exercise to present this concept to all departments in the operation and explain how each area impacts TAU. Also, individual departments are not always aware how all the parts of the process come together. Ideas would be generated for improvements. Nobody understands an area like the participants in that area.
Process improvement expert David Argent has 30+ years of experience in process analysis with particular emphasis on ink and coating design and performance. Contact him at 314-409-4304; djvargent@sbcglobal.net.