Technical Report: Up & Running
- Published: June 01, 2011, By By Michael Pappas, Catbridge Machinery
Recent innovations have improved the performance of slitter/rewinders dramatically, offering superior wind quality and impressive production rates. Turret winders incorporating the latest technologies, for example, can outproduce traditional winders by 200%-300% or more in some applications. Today's slitters also do a much better job of minimizing waste.
In the past decade, more powerful and sophisticated machine control systems have emerged. Utilizing PLC-based systems, slitters can integrate more automated features and functions. Automatic knife positioning, core positioning, and closed-loop tension are now more common on standard slitters.
Tremendous gains in productivity are due to innovations that greatly reduce downtime — or non-running time — at key points in the slitting process. Major downtime causes are grouped in three areas:
- Loading jumbos rolls
- Getting ready for a new cycle between sets (unloading finished rolls and re-loading cores)
- Setting up the slitter (knife changes) for a new job
To speed up loading jumbos rolls, a growing number of converters are using shaftless floor pickup unwinds for rapid and operator-friendly loading. While not strictly a “new” technology, chuck improvements and more flexible, functional designs have increased effectiveness. A variety of new two-position configurations, for example, allow a new roll to be loaded while the machine is running, an especially significant advantage for small orders using one jumbo roll or less.
The two greatest areas of downtime occur between jobs and between sets. For reducing downtime between jobs, automatic knife placement has become increasingly popular. Available for shear, score, and razor slitting, these systems greatly reduce setup times. For example, an auto score system can precisely position more than 100 score knives within a few minutes.
In addition to reducing setup times, automatic knife placement systems provide the added benefit of quality improvements and waste reduction by positioning knives precisely and consistently. The result is less rejected product, reducing losses and waste. Auto knife systems also incorporate PLC recipe storage for job repeatability. These systems provide the greatest return on investment for jobs with many cuts and jobs that don't run an entire jumbo roll, meaning many knife setups per shift.
For downtime between sets, dramatic, business-changing time savings can be achieved on turret winders. Turret designs have been around for years. However, the recent incorporation of many new supporting features has allowed turrets to reach their full potential to reduce downtime.
Additionally, advances in tension control, web positioning, and rewind shaft technology allow center wind turrets to be used for a broader variety of material applications. Turrets are ideal for both high-volume, long-running, multiset orders and also short-length runs with lots of changeovers.
Automate the Cutoff
To make the most of the turret's time-saving capabilities, state-of-the-art technologies work together to fully automate the cutoff and transfer process between sets. And, importantly, these features save time without sacrificing quality, so high quality finished rolls can be delivered to customers.
The technologies needed for automation include improved, highly reliable cutoff and transfer systems that take advantage of the turret rotating disc design, allowing winding on one shaft while cores are loaded on the other. Additional technologies include tabbing to pre-tape the web and roll enveloping of tails onto both new cores, with no fold-back, and at the finished roll for tail wipe-down and seal. These features all function together to eliminate manual processes and substantially reduce downtime.
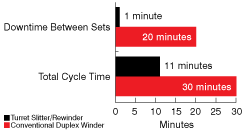
Fully automatic cutoff, transfer, and new core attachment can result in at least two to three times more productivity. For example, where downtime between sets is 20 minutes using a conventional duplex winder, utilizing a turret winder that completely automates the cutoff and transfer process reduces downtime to a minute or less (see Figure 1).
If run time to generate a finished roll is 10 minutes, a set now can run every 11 minutes with the turret, as opposed to every 30 minutes on a conventional design. Over an eight-hour shift, the turret can run 44 sets per shift compared to 16 sets with a conventional machine, nearly tripling production.
For reducing downtime between sets, another important innovation is automatic core positioning. Available for all types of slitter/rewinders, not just turrets, this technology also provides more accurate setups — ensuring that cores are aligned with the material — and eliminates startup waste.
Different from laser-based, operator-assisted core positioning, auto core positioning works in conjunction with auto knife placement. It precisely positions cores while the operator performs packaging or other finished roll discharge activities. This technology is useful for jobs with several narrow cuts.
Technological advances for particular materials can further improve performance. For example, closed-loop tension ensures better roll build and edge quality across the spectrum of flexible packaging films and laminations. Dual bowed rolls utilizing proper geometry help ensure uniform slit separation, even on narrow cuts for both paper and flexible packaging materials.
What's Right for You?
So how do converters decide what innovations best meet their needs and what level of automation can help maximize productivity and provide a worthwhile return on investment? Working with the vendor, converters can closely examine roll production data, looking at months, not just days, to determine the exact blend of work.
Factors to consider include job durations, changeovers per day, materials and cut ranges, roll length and diameter, run times, and specialty requirements such as inspection or cleaning.
Another consideration is flexibility for future needs. Web paths can be designed and machine frames prepared to accommodate a variety of future additions. Some examples include lasers for scoring, cameras for inspection, web cleaning technology, automated knife placement, tabbing, and different slitting methods.
As the last step in the converting process, slitting and rewinding carries the value-added weight of all plant processes: extrusion, printing, and laminating. Nowhere in the plant is a pound of material worth more.
Recent slitter innovations have helped minimize waste, create top quality rolls, improve ergonomics, and significantly reduce downtime. Full realization of profit — or very expensive losses — occur at the slitter, making the correct choice of the most efficient, productive slitter essential for maximizing a plant's bottom line.
Michael Pappas, president and founder of Catbridge Machinery, Parsippany, NJ, has an engineering background and 25+ years of experience in the converting industry. Contact him at 973-808-0029.
Supplier Info
-
Catbridge Machinery | www.catbridge.com
For more solutions, products, services, and news, click on the Slitting One-Stop at www.pffc-online.com.