Unwinding Static
- Published: August 22, 2011, By By Dr. Kelly Robinson, Contributing Editor
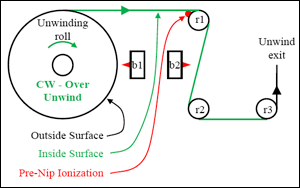
Static comes and goes. It is often just an annoyance. Sometimes, static can be the root cause for a significant amount of waste. And, occasionally, static shuts down a line when sparks might ignite flammable vapors.
Intermittent static problems are difficult to diagnose. Working to solve these intermittent static problems has caused many headaches!
Process variability often causes intermittent problems. Static charges from previous operations wound into incoming rolls contribute variability to the static performance of our line. Since the sources of static in previous operations are usually beyond our reach, there is little that we can do.
One strategy for managing this variability is to set specifications for static on incoming rolls, audit the incoming rolls, and return “hot” rolls having static levels exceeding our specifications. While this strategy is effective, it requires diligent effort.
A better strategy is to make our process more robust and tolerant of static on incoming rolls. To do this, we must neutralize most of the static charges on the incoming rolls. Unwinding a roll is a unique opportunity to do just this. And, this neutralization method also effectively dissipates static charges separated by tribocharging when the film is peeled from the unwinding roll.
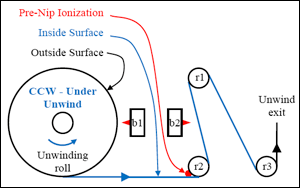
Two static bars and two conveyance rollers are needed to neutralize static on an unwinding roll. The scheme is flexible. It works for rolls unwound in the clockwise or “over” orientation in Figure 1 and for rolls unwound in the counter clockwise or “under” orientation in Figure 2.
The locations of static bars b1 and b2 are fixed. In each orientation, static bar b1 neutralizes the outside surface of the unwinding roll. Since the roll diameter decreases as the roll expires, static bar b1 must be a high performance static bar with long-range neutralization capability.
Static bar b2 neutralizes the inside film surfaces in both thread-ups. After the first conveyance roller, the film position is stationary and static bar b2 may be located a fixed distance from the film. So, static bar b2 can be an economical model with no need for long-range neutralization performance.
The first conveyance roller must touch the inside film surface, which is accomplished by an alternate thread-up for each orientation. The outside film surface is nearly neutral, so static will reside on the inside film surface. As the charged film approaches the first conveyance roller, a static discharge called pre-nip ionization will occur between the film and the roller. This discharge will help neutralize the film because the first conveyance roller touches the charged, inside film surface. However, if the first conveyance roller touches the outside film surface, pre-nip ionization will deposit charge on the nearly neutral outside film surface, and the neutralization performance of the system is compromised.
Making your process more robust and tolerant of static on incoming rolls reduces waste and helps prevent line shut-downs for high static.