Static Beat | Verifying Static Dissipator Performance
- Published: March 08, 2017, By Kelly Robinson
How can we tell if a static bar or a tinsel strand is working?
Our primary static control goal often is to suppress sparks. Sparks that are too small to see or hear can ignite flammable vapors. These small sparks can damage thin coatings, such as release layers. And, spots of static charges deposited by sparks can cause sticking and jamming when our web is cut into sheets. We suppress sparks by installing active static bars and passive static dissipators. Of course, when these devices work properly, static is well controlled, and life is good.
How do we know if our static bars and our passive static dissipators are working properly? Static sparks are often too small to see or hear. And, I cannot look at a dissipator and know if it is working. Of course, we must not wait for a customer complaint to know that something is wrong. So, what can we do to verify that our static control devices are working?
Table I. Static Device Verifiers
Indicators
Our first verifier in Table I is to ensure that the indicator lights are lit on the static bar power supplies. Mount the power supplies so that they are visible from the operator aisle. A quick glance is enough. While this verifier seems trivial, static problems caused by de-energized static bars have caused tens of thousands of dollars of waste. In one case, a line was down for maintenance and cleaning that required several static bars to be removed from the machine. Well, of course, all static bars were properly installed before Maintenance returned the machine to Operations. However, one of the power supplies was left unplugged. This was a simple error … just a human mistake. No one noticed. There were no checks or verification procedures in place to catch the error.
After producing more than $30K of waste, (the product had too much static … it was “too hot” for the customer to use), I was called to solve this static problem. Well, while the root cause was that a static bar was not working properly, the remedy was to implement checks and verification procedures that would detect this error. One simpler verifier is to locate power supplies so that they are visible from the operator aisle and training operators to glance at the power supplies to ensure that indicators are lit during the set-up of a job.
My assessment in Table I is that a lit power indicator is necessary though insufficient for proper operation. Certainly, power must be applied for proper operation. However, the static bar must produce ions to operate properly. Even with power applied, ion output may be low because pin tips may be dull or dirty. Some “smart” static bar systems have a “clean bar” indicator, display ion output, or communicate this to the machine control system. These outputs can serve as verifiers. Ask your static control supplier about these features.
Some organizations require that a “process verifier” be independent of the process that it verifies. In this case, a static bar system output cannot serve to verify the static bar system. Verifiers 2 and 3 in Table I are independent process verifiers for our static control devices.
Static Bar Checker
Some vendors offer a “Static Bar Checker” that is about the size of a ballpoint pen. Touch a pin of a static bar with the metal tip of this plastic device. If high voltage is present, an indicator lights.
Again, my assessment in Table I is that high voltage applied to the static bar is necessary though insufficient for proper operation. Remember that the static bar must produce ions to operate properly. Even with high voltage applied, the ion output may be low because the pin may be dull or dirty.
Neutralization Efficiency
I recommend verifying the performance of a static dissipator by measuring its neutralization efficiency. As indicated in Table I, this is the only verifier that also works for passive dissipators. For this verifier, you’ll need three tools:
- A handheld electrostatic fieldmeter
- A piece of insulating plastic approximately 3 in. × 6 in.
- A piece of wool
For the insulating piece, I prefer 3/32-in. PTFE, such as McMaster-Carr 9266K83 (available for less than $20) because it is easy to charge.
Verify static dissipator performance using the procedure outlined in Table II.
Table II. Measure Static Neutralization Efficiency
The idea is to charge the insulating piece and use it to simulate a charged web passing by the static dissipator. We will measure how much of the charge on the PTFE card in Figure 1 is neutralized by the dissipator. Active static bars should neutralize at least 90% of the charge. For example, if the initial field is –10 KV/cm, our active static bar should reduce the field to less than –1 KV/cm. If the final field is too big, the performance is poor and the bar should be cleaned.
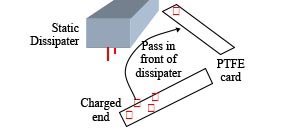
A passive dissipator should neutralize at least 80% of the charge. For example, if the initial field is –10 KV/cm, our passive static dissipator should reduce the field to less than –2 KV/cm. If the final field is too big, the performance is poor and the static dissipator should be replaced.
Properly functioning active static bars and passive static dissipators suppress sparks that are too small to see or hear. Even these very small sparks can ignite flammable vapors, damage thin coatings such as release layers, or deposit spots charge can cause sticking and jamming when the continuous web is cut into sheets. By verifying the performance of our static dissipators, we can detect problems and restore good performance before static problems occur.
I invite you to ask questions about this column and to suggest future topics. My email address is: Kelly.Robinson@ElectrostaticAnswers.com.
Static control expert Dr. Kelly Robinson, president of Electrostatic Answers, has 27+ years of experience in problem-solving and consulting. Kelly writes PFFC's Static Beat column and the Kelly on Static blog. Contact him at 585-425-8158; kelly.robinson@electrostaticanswers.com; www.electrostaticanswers.com.